Сегодня мы хотели бы познакомить Вас с опытом остекления
высотного здания, выполненного фирмой ИгЛА. Выигранный тендер на остекление высотного здания в центре Одессы поставил перед компанией ряд вопросов, требующих нестандартного решения, так как высотное строительство в Украине далеко не так распространено, как в Европе, да и нормативная база не спешит приноравливаться к новым условиям строительства. Поэтому каждый объект, предусматривающий сверхнормативную этажность, должен прорабатываться индивидуально. Основная часть фасадного остекления здания — это самонесущий алюминиевый фасад. В его угловые стоечно-ригельные части интегрирована композитная фасадная система. Каркасная бетонная стоечно-ригельная система, на которую нужно было устанавливать крепления фасадных стоек, изначально не имела ни одной пары ортогональных плоскостей. Поэтому остеклению предшествовал анализ состояния здания и тщательные измерения. Чтобы определить отклонения от нормалей, лазером наносились реперные точки. |
![]() |
Впоследствии компьютерный анализ данных позволил “примерить” ортогональный колпак из алюминиевого профиля и стекла на здание. С помощью современных программ был рассчитан оптимальный раскрой стекла и композита, что позволило существенно снизить себестоимость фасадной системы.Чтобы нивелировать дефекты здания, неизбежные у нас при строительстве, были разработаны специальные системы креплений, позволяющие практически в любых плоскостях выставлять идеально ортогональную стоечно-ригельную систему. Используя вместо алюминия более прочную оцинкованную сталь, удалось повысить прочность креплений, а заодно и уменьшить их себестоимость.
На следующем этапе было выполнено остекление угловых частей здания, для
облицовки, утепления и гидроизоляции которых были использованы композитные
панели ALUCOBOND (DIBOND, ITALBOND).
Чтобы выполнить качественный монтаж на больших высотах, было применено
собственное нестандартное решение. Специалисты компании разработали системы
крепления композита к бетонным плоскостям, а также варианты гидро- и теплоизоляции
вертикальных пустот между бетоном и фальш-фасадами.
Шахты, образованные фальш-фасадами и бетонными конструкциями, вместо стандартных
твердых теплоизоляторов наполнили специальной пеной. Такая пена обеспечивает
надежную теплоизоляцию, устойчива во всех климатических средах, не имеет
теплового расширения и, в отличие от обычных монтажных пен, не расширяется
при заполнении, что могло бы деформировать фасадную облицовку.
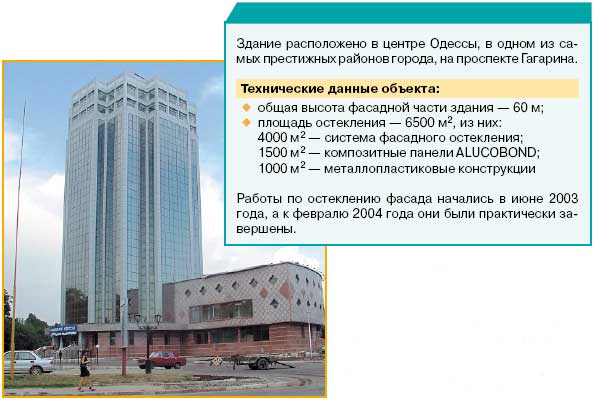
В конце были выполнены встроенные усиленные металлопластиковые конструкции, установленные на верхних этажах здания. Эти конструкции призваны, с одной стороны, обеспечивать панорамный обзор, а с другой — быть устойчивыми к ветровым нагрузкам.
В проемах 15 и 16 этажей, на высоте 55 м, были установлены окна из профиля REHAU с максимальным размером стеклопакета на 16-ом этаже 1,44X2,54 м (6:12:8 — наружу).
На нижних этажах были смонтированы металлопластиковые системы высотой около 3-х метров также с использованием соответствующих систем усиления. В качестве базовой использовалась фурнитура GU с системами дистанционного открывания Ventus.
В 2000 году специалистами фирмы “ИгЛА” был
изготовлен первый станок для производства ПВХ-конструкций. В дальнейшем
оба этих направления — производство ПВХ-конструкций и оборудования
— развивались параллельно.
В 2001 году была выпущена первая линия, а в 2002 году фирма вышла на первое место в Украине по поставкам оборудования отечественного производства. Одновременно изготавливалось остекление сложных объектов из профилей ПВХ. Впоследствии было освоено производство алюминиевых фасадных конструкций |
В остеклении двух первых и двух последних этажей были использованы прозрачные
стекла, для остальных этажей — зеркальные стекла “Stopsol”. В качестве
основного наружного стекла применили “шестерку” с жестким рефлекторным
нанесением. Основные требования, предъявляемые к стеклопакету, — это способность
выдерживать повышенные ветровые и термические нагрузки, не подвергаясь
термошоку. Эти требования и выполнило наружное стекло. Наружный рефлекторный
слой исключает прогрев массы стекла, а жесткость этого слоя позволяет
при правильном уходе эксплуатировать стекло более 10 лет.
Между стеклом и внутренней отделкой примыканий был установлен гипсокартон,
окрашенный в черный цвет стойкими к выцветанию красителями. Такое решение
позволяло обеспечить хорошую теплопроводность и избежать термошока, вероятность
которого в замкнутой камере велика, тем более в южном регионе.
![]() |
Однин из примеров многогранности работ, выполняемых фирмой “ИгЛА”,
— это арки для одесского Привоза. |
|
Уже после остекления высотного здания
в центре Одессы ООО “Игла” успела выполнить работы по целому ряду
крупных и интересных объектов. Например, 31 августа в Одессе прошло торжественное открытие нового рыбного корпуса рынка “Привоз” и реконструированного здания головного офиса АКБ “Имэксбанк”, выполненных ООО “ИгЛА” в кратчайшие сроки. В церемонии открытия приняли участие мэр Одессы — Боделан Руслан Борисович, а также почетный президент ФК “Черноморец” Климов Л. М., председатель правления АКБ “Имэксбанк” Скорик Н. Л. и другие гости. |
![]() |
Двустороннее открывание реализовали при помощи сочетания верхнего и напольного доводчиков Dorma. Уже более 2-х лет конструкция работает бесперебойно, тогда как стандартно выполненные двери несколько раз менялись. |
Монтаж
Высота здания превышала 60 м, поэтому монтаж фасадной конструкции проводили
высотные бригады, умевшие работать как с обычными монтажными люльками
или строительными лесами, так и с альпинистским снаряжением.
Стекло подавалось на объект поэтажно при помощи подъемно-транспортных
механизмов, в том числе и башенного крана. Стеклопакеты устанавливались
на специально сконструированную платформу, которая и перемещала с этажа
на этаж вес, достигающий 2-х тонн. Стекло подавалось вертикально, так,
чтобы и монтажники-высотники могли работать по вертикали. По горизонтали
такую конструкцию монтировать просто невозможно: это потребовало бы непрерывной
перестановки люлек, что отнимает львиную долю времени.
![]() |
|
Организация подготовительного производства
Масса алюминиевого профиля, который нужно было “навесить” на фасад, составляла
20 тонн. Эту массу нужно было привезти на производство, распилить, профрезеровать,
после чего доставить на стройплощадку, где происходил монтаж.
Чтобы избежать непродуктивной потери времени и усилий, было решено цех
по производству алюминиевых конструкций оборудовать прямо на территории
строящегося здания. Благодаря этому решению удалось сократить транспортные
потери и существенно уменьшить повреждения при транспортировке.