В этой статье рассматриваются особенности разрушения и технической прочности стекломатериалов, таких как листовое стекло и стеклокерамические изделия с поверхностными, внутренними и смешанными типами критических дефектов1. Флоат-стекло и множество других строительных материалов, в состав которых входит стекло, имеют поверхностные дефекты — микротрещины, другие повреждения на поверхности, которые определяют техническую прочность изделий под действием эксплуатационных нагрузок.
1 Критический дефект – дефект, могущий привести к разрушению системы (Прим. редакции).
Характерные разновидности критических дефектов стеклокерамических структур могут существенно изменяться под влиянием особенностей отдельных технологических способов производства, что позволяет управлять технической прочностью элементов конструкций при условии внедрения соответствующих методов производственного контроля дефектности и механических свойств на промышленных предприятиях.
ВВЕДЕНИЕ
Стекло и керамика — особые конструкционные материалы с трудно предсказуемым уровнем прочности. Главное их отличие от обычных строительных материалов — недостаточная пластичность и крайне малый размер дефектов (например, трещин), которые могут стать причиной хрупкого разрушения [1, 2]. Контроль критических дефектов и действительные параметры прочности для стекла и керамики — особая сфера науки о прочности, которая до сих пор недостаточно развита. Поэтому прочность и долговечность строительного и транспортного стекла и керамики недостаточно пронормированы по сравнению с металлическими и другими традиционными конструкционными материалами. Производители стекла обычно не гарантируют фактическую прочность их изделий. У наиболее технически развитых фирм базой для обеспечения прочности конструкций является совокупность отработанных технологических и конструкционных решений, проверенных надлежащими экспериментальными методами и являющихся фирменным «know-how».
Проблема может быть решена путем внедрения знаний в области конструкционной прочности стекла и керамики на предприятиях отрасли и эффективного использования опыта создания долговечных изделий особого назначения — для авиации, оптоэлектронных устройств, космической и подводной техники [1–4]. Последние исследования технической прочности стекла и керамики для строительных конструкций показывают многообещающие способы увеличения характеристик опорных элементов, сделанных из данных материалов [5–7]. Однако комплекс имеющихся знаний в этой области до сих пор остается неизвестным широкому кругу специалистов в области архитектуры и автотранспорта. Это снижает эффективность и масштабы применения стекла и керамики в качестве конструкционного материала.
Техническая прочность этого класса материалов зависит от множества технических, технологических, конструктивных и эксплуатационных факторов [3, 4]. Для создания несущих элементов из стекла и стеклокерамики с заданным уровнем несущей способности и долговечности нужен интегральный технический подход. Управление прочностью стеклянных изделий путем контроля возникновения дефектов и оптимизация технологии производства исходя из критерия прочности — основная часть такого подхода. Этот подход позволяет учитывать влияние основных технологических, конструктивных и эксплуатационных факторов на работоспособность конструкций.
В статье рассматриваются поверхностные и внутренние дефекты в стекле и керамике. Показано превалирующее влияние поверхностных дефектов на прочность аморфных материалов, таких как стекло с наноразмерными дефектами во внутренней структуре. Обнаружено увеличение роли внутренних технологических дефектов в изделиях из стеклокерамики, полученных разными технологическими способами.
Повышение неоднородности и нарушений структуры хрупкого материала сильнее всего влияет на возникновение внутренних дефектов. В результате чего наблюдается смешанный характер возникновения и распространения критических источников разрушения вокруг внутренних концентраторов напряжений в существенно неоднородных и дефектных керамических изделиях из-за недостатков общепринятых технологий их производства, связанных с недостаточным контролем структурных дефектов, трещин, пор и повреждений, возникающих на различных стадиях изготовления и при эксплуатации конструкций.
Показано, что данные о механических свойствах элементов несущих стеклянных и стеклокерамических конструкций могут быть непосредственно использованы для разработки надлежащих технологий их изготовления, методов контроля состояния критических дефектов и для мониторинга прочности непосредственно в процессе производства. Результаты исследования и положительный опыт проектирования прочных элементов типа плит, стержней и оболочек показывают возможность полностью гарантировать заданную несущую способность нагруженных конструкций, несмотря на хрупкость и ограниченную прочность при разрыве стекла и стеклокерамики.
РАЗРУШЕНИЕ И ПРОЧНОСТЬ ОДНОРОДНЫХ МАТЕРИАЛОВ ИЗ-ЗА ПОВЕРХНОСТНЫХ ДЕФЕКТОВ
Флоат-стекло и высококачественная термостойкая стеклокерамика, произведенная по традиционному «стекольному» способу формования изделий — материалы, чувствительные к влиянию поверхностных дефектов. Известно, что поверхностные микротрещины, существующие в трещиноватом поверхностном слое изделий, являются главным источником разрушения, возникающего в несущих элементах под воздействием механической и термической нагрузки [1, 6]. Внутренние нано- и микро-размерные дефекты структуры этих материалов редко приводят к разрушению деталей. Было показано, что источником разрушения чаще всего является типичная для упругих хрупких материалов полуэллиптическая микротрещина [1]. Она обычно располагается в центре зеркальной зоны поверхности излома, как показано на рис. 1. При этом прочность и долговечность деталей из поверхностно дефектных материалов прямо зависят от глубины трещины или подобного повреждения поверхности.
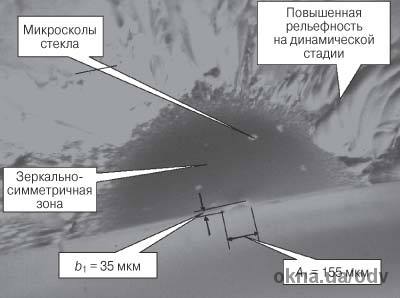
Рис. 1. Микротрещины в центре зеркально-симметричной зоны разрушения поверхности закаленного флоат-стекла
На рисунке показана практически плоская зеркальная зона излома, ориентированная по нормали к направлению напряжений разрыва, повышенная рельефность излома на фазе нестабильного быстрого роста трещины и отдельные микросколы стекла. Критическая глубина микротрещины b1 и ширина А1.
Форму, глубину b1, ширину А1 и другие параметры разрушенного поверхностного слоя можно проконтролировать с помощью микрофотографий разрушенной поверхности, чтобы гарантировать определенный уровень прочности флоат-стекла. Рис. 2 показывает трещиноватый поверхностный слой толщиной 30–45 мкм, определенный при контрольном разрушении образца стекла из партии. Результаты испытаний можно использовать для отбора качественного стекла или наилучших участков поверхности листа, тем самым производитель получает возможность контролировать качество несущих конструктивных элементов в процессе производства, дефектность и, соответственно, гарантировать уровень прочности конструкций.
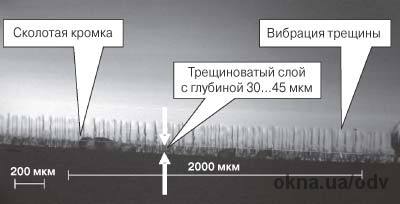
Рис. 2. Метод контроля качества флоат-стекла измерением глубины трещиноватого слоя. Показана глубина слоя флоат-стекла с трещинами, которые трудно обнаружить другими методами
За счет использования нового способа контроля качества листового стекла и изучения изломов изделий при изгибе и разрыве, был обнаружен докритический рост длинномерных поверхностных микротрещин на стеклянных пластинах при нагрузках, близких к предельным значениям. Рис. 3 показывает, что величина роста трещины достигает 84% от ее первоначальной глубины. Проблема состоит в выборе базового геометрического параметра — первоначальной глубины b0 или критической глубины bcr для определения долговечности и степени сопротивляемости несущих стеклянных элементов с использованием уравнений механики разрушений [6]. Критические размеры микротрещин соответствуют кратковременной финальной фазе процесса разрушения стекла. Их контроль более труден, чем контроль параметров первоначальных трещин, приводящих к разрушению. Таким образом, для определения ожидаемого сопротивления росту трещин и прочности материала с дефектами поверхности, а также для упрощения оценки прочности и долговечности изделий в качестве базового параметра может быть принята именно глубина первоначальных трещин.
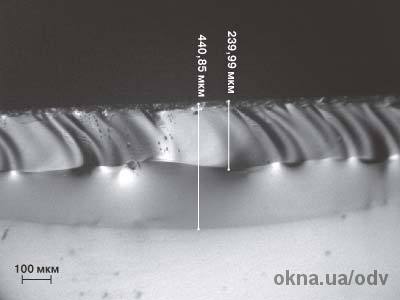
Рис. 3. Докритический рост длинномерной трещины на поверхности стеклянной пластины при 95% от предельной нагрузки при испытании на изгиб
В исследованиях [1, 6] было показано, что контроль дефектности поверхности, прочности и сопротивления разрушению стекла и высококачественной термостойкой стеклокерамики, производимой по технологии стекла, необходим на всех этапах производства элементов несущих конструкций, как показано на рис. 4.
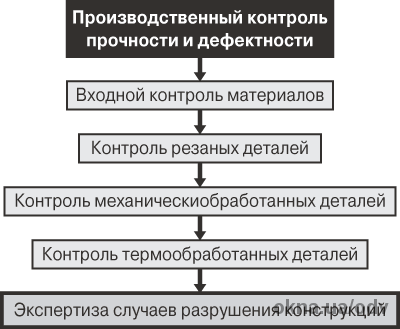
Рис. 4. Схема производственного контроля прочности и дефектности конструкционных деталей из стекла
Эта система производственного контроля включает ряд методик испытаний — оптический контроль дефектов поверхности и поверхности излома испытанных образцов, механические тесты на прочность и сопротивление росту трещин при изгибе, оценку прочности и долговечности несущей конструкции, опираясь на результаты испытаний образцов, а также на результаты испытаний реальной конструкции. Влияние масштабного эффекта, технологических и конструктивных факторов, так же как и предельных условий эксплуатации можно рассчитать при внедрении такого подхода. Число и последовательность этапов испытаний изделий из стекла и стеклокерамики зависит от метода и основных этапов на производстве.
ДЕФЕКТЫ И ПРОЧНОСТЬ ШЛИКЕРНОЙ СТЕКЛОКЕРАМИКИ
Указанный подход и методика контроля прочности и дефектов изделий из стекла нуждается в улучшении путем учета особенностей внутренней и поверхностной структуры стеклокерамики. Механическая прочность деталей из стеклокерамики во многом зависит от микродефектов поверхности, а также внутренней структуры, существенно связанной с фактическим качеством, обеспечиваемом используемой технологией, механической и термической обработкой [8, 9]. Известно, что замена микрочастиц наночастицами в составе шликера приводит к улучшению эксплуатационных свойств. Авторы исследовали прочность и характер разрушений литой термостойкой стеклокерамики с добавками в шликер наночастиц SiO2 и TiO2.
Несколько коротких примечаний о недостатках шликера на водной основе из литий-алюмо-силикатного стекла:
- высокое влагосодержание в суспензии необходимо для гарантирования надлежащего уровня текучести;
- тенденция к осаждению крупных частиц и неоднородному загущению;
- недостаточная плотность и прочность литых изделий.
Разработанная технология литья термостойкой стеклокерамики с наноразмерными наполнителями улучшает внутреннюю и поверхностную структуру материала и увеличивает прочность оболочки при эксплуатации при более жестких условиях. Авторы исследовали возможность добавления наночастиц SiO2 и TiO2 в количестве10–30% в водный шликер для производства улучшенных изделий из стеклокерамики.
Был тщательно разработан специальный комплекс неразрушающих и разрушающих методов контроля [7–10], позволяющих убедиться в долговечности конструкций из стеклокерамики в обычных и предельных условиях эксплуатации при температуре до 1000°C. Методы основаны на прецизионных испытаниях контрольных образцов, моделей и реальных конструктивных элементов — оболочек и пластин — в сочетании с другими нестандартными методами испытаний для эффективного их использования непосредственно в условиях производства высокотермостойкой стеклокерамики.
В результате этого исследования было показано, что существенная неоднородность, склонность к порообразованию и появлению технологических дефектов спеченной заготовки уменьшают прочность и несущую способность стеклокерамических оболочек в обычных и экстремальных условиях эксплуатации. Характеристики влияния нано- и микроразмерных добавок на структуру исходного стекла и спеченных заготовок для стеклокерамического изделия были изучены путем микрографии на атомно-силовом микроскопе. Было показано, что гомогенность структуры специального исходного стекла близка к аморфной структуре флоат-стекла (рис. 5) Но, при исследовании поверхности разрушений заготовок из специального стекла, там были обнаружены центры первичной кристаллизации.
Характер, увеличенные размеры структурных элементов и дефекты внутреннего строения спеченного изделия из стеклокерамики видны на рис. 6. Размеры зерен примерно 5…10 мкм. Размеры кристаллических агрегатов были около 20…30 мкм. Поры и другие внутренние технологические дефекты вместе с микроскопическими включениями и дефектами структуры стеклокерамики — типичные источники возникновения разрушений.
![]() |
![]() |
Рис. 5. Структура разрушенной поверхности исходного специального стекла с центрами первичной кристаллизации и линейчатыми следами прерывистого роста трещины | Рис. 6. Характер поверхности излома спеченной стеклокерамики с увеличенными поликристаллическими образованиями в структуре и дефектами |
Образование поверхности излома и трещинообразование обычно происходят по границам расположения поликристаллических агрегатов внутри стеклокерамики. Поры и другие технологические дефекты можно контролировать по специальной технологии, путем механических испытаний, оптического тестирования и применения технологических методов. Типичные форма и соотношение размеров b/2c критической микротрещины в фокусе излома показаны на рис. 7a. Поры и крупные скопления зерен в изломе спеченной шликерной стеклокерамики показаны на рис. 7b.
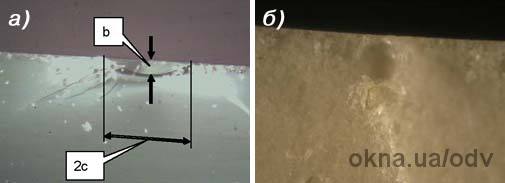
Рис. 7. Отличие в природе возникновения разрушений в стекле (а) и шликерной стеклокерамике (б) при изгибе
Для повышения возможностей производства и ограничения отрицательного влияния типичных дефектов при подготовке шликера для стеклокерамики был разработан новый инженерный подход. Этот подход предполагает использование новых нанокомпонентов в составе шихты для шликера, из которого формируется заготовка для последующего спекания и получения стеклокерамического изделия. Основная идея заключалась в том, чтобы заменить в составе микрочастицы из SiO2 нано-размерными частицами, что приводит к улучшению механических свойств изделия.
Технический контроль изделий из стеклокерамики и их прочности включает комплекс оценок параметров прочности на изгиб и твердости образцов, полученных на различных этапах производственного процесса из реальных оболочек, а также из фрагментов их заготовок.
Результаты исследований показывают, что добавка предложенных наноразмерных компонентов ограничивает проявление выпадения в осадок частиц шликера, повышает однородность суспензии и степень уплотненности шликера при формировании заготовки стеклокерамическиго изделия, полученного путем последующего спекания. Прочность на изгиб 120 МПа при этом гарантируется, и сопротивление разрушению (трещиностойкость) увеличивается на 15…20%. Были получены корреляционные кривые между этими данными непосредственно в условиях реального производства. Корреляционные кривые для динамической твердости и температуры термообработки стеклокерамики показаны на рис. 8. Оптимальные условия термообработки были выбраны с использованием этих экспериментальных закономерностей для шликера разного состава.
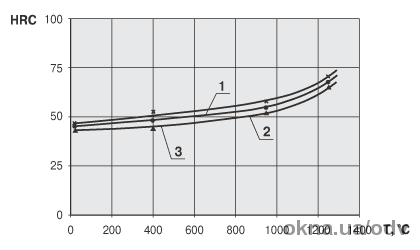
Рис. 8. Данные динамической твердости в зависимости от температуры термообработки изделий из стеклокерамики: 1 – минимальные величины; 2 – максимальные величины; 3 – значимые величины
В результате исследований обнаружено, что добавка наночастиц в состав шихты для получения шликера для изготовления стеклокерамики путем спекания литой заготовки увеличивает плотность и однородность внутренней структуры и прочность деталей, улучшает физические свойства и обеспечивает более высокую стабильность стеклокерамики. Показано, что комплекс инженерных мероприятий, основанных на результатах испытаний качества и прочности, дает возможность обосновать новые технические решения и оптимизировать технологию стекольного и керамического производства, ориентируясь на данные этих испытаний и критерии прочности.
Результаты данных исследований были внедрены на основных стадиях процесса производства изделий из термостойкого нанокомпонентного стеклокерамического материала для экстремальных условий эксплуатации.
ЗАКЛЮЧЕНИЕ
Из результатов следует, что:
- особенности и характер разрушения, и техническая прочность, установленные путем анализа поверхностных, внутренних и смешанных критических дефектов материала при механических испытаниях, зависят от структуры материала, которая в свою очередь зависит от технологических, конструктивных и эксплуатационных факторов;
- реализованный эффективный технический подход и методы контроля прочности и обнаружения дефектов в изделиях из стекла с разным типом дефектов можно внедрить непосредственно на основных стадиях производства изделий из стекла и термостойкой нанокомпонентной стеклокерамики для обычных и экстремальных условий эксплуатации;
- глубина трещиноватого поверхностного слоя и характеристики микротрещин — важные параметры качества флоат-стекла и производства элементов несущих конструкций, которые требуют оптимизации параметров производства для гарантирования заданной работоспособности ответственных конструкций из стекла и керамики.
- Rodichev Yu., Tregubov N. The Challenge of Quality and Strength of the Hardened Architectural Glass // Proceedings GPD. – 2009. – Р. 827–830.
- Veer F.A., Rodichev Yu.M. Glass failure, science fiction, science fact and hypothesis // Proceedings of International Conference «Glass Processing Days 2009». – Р. 819–823.
- Pointer publications of the G.S. Pisarenko Institute for Problems of Strength on the strength of non-metallic materials and structural elements/ Ed. Y.M. Rodichev. – Kiev: G.S. Pisarenko Institute for Problems of Strength, NAS of Ukraine, 2010. – 204 p. (rus).
- Strength of materials and structures/ Rodichev Yu.M. // Chapter 9.2 Structural strength of glass and ceramics/ Ed. Troshenko V.T. — Кiev.: Academperiodika, 2005. — P. 955–992, (rus).
- Veer F.A., Louter P.C., Bos F.P. The strength of architectural glass. – Challenging Glass. Conference on Architectural and Structural Applications of glass. – Faculty of Architecture, Delft University of Technology. – May 2008. – P.P. 419–428.
- Rodichev Yu., Veer F. Fracture resistance, surface defects and structural strength of glass. – Challenging Glass 2 – Conference on architectural and structural application of glass. – 2010. – TU Delft. – P. 363–373.
- Rodichev Yu. Assessment and Management of Strength and Durability of Composite Glass Elements. – Proc. of Int. Conf. Challenge Glass 2. on Architectural and Structural Applications of Glass. – 2010. – TU Delft. – Р. 351–362.
- Rodichev Yu.M., Maslov V.P., Netychuk A.V., Bodunov V.P., Yevplov Yu.N. Bending Strength and Fracture of Glass Materials under the Different Loading Conditions, «Glass Performance Days» Conf. Proc., Tampere, Finland, 2007. – P.P. 615–618.
- Maslov V.P., Rodichev Yu.M., Demaille D., Zheng Y. , Lacaze E., Roditchev D. Strength and Fracture of Nano-Joints for Glassceramics Materials and Elements. – Proc. Intern. Conf. «Nansis 2007», Kyiv, 2007, С. 495.
- Rodichev Yu.M., Maslov V.P., Bodunov V.P., Yevplov Yu.N. Methods of Composite Glass Materials Quality and Strength Testing, «Glass Performance Days» Conf. Proc., Tampere, Finland, 2007. – P.P. 624–625.
К.т.н. Ю.М. Родичев, Институт проблем прочности
им. Г.С. Писаренко НАНУ, г. Киев, Украина,
д.э.н. Н.Ф. Трегубов, Костантиновское НПП «Кварсит»,
г. Константиновка Донецкой обл. Украина,
д-р Ф.А. Веер (Frederic A. Veer) Технологический университет,
г. Дельфт, Нидерланды,
д.т.н. В.П. Маслов, Институт физики полупроводников
им. В.Е. Лашкарева, НАНУ, г. Киев, Украина.
По материалам доклада на Glass Performance Days,
июнь 2011 г., Тампере, Финляндия