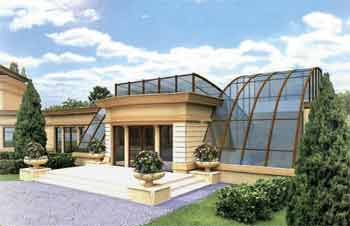
Рис. 1. Кровля бассейна
Рассмотрен процесс разрушения однокамерных стеклопакетов из гнутого закаленного стекла, которые применялись для остекления арочной кровли плавательного бассейна в Московском регионе России. Вскоре после завершения монтажа стеклопакетов начался процесс их саморазрушения, который продолжался несколько месяцев. Разрушалось только внешнее прозрачное стекло, спонтанно, в любое время суток, на различных хаотически расположенных местах кровли. Проанализированы возможные причины разрушения: влияние климатических факторов (температуры и давления наружного воздуха), механические воздействия из-за деформаций оснований и фундамента сооружения и при монтаже, влияние метода моллирования, процессов термического нагрева и охлаждения стекла при закалке и др. и найдена причина саморазрушения.
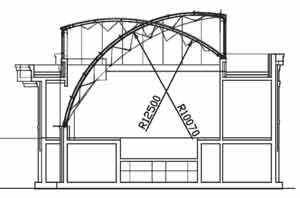
Рис. 2. Конструкция несущей части кровли
Введение
В сентябре-ноябре 2006 года в строительном проекте плавательного бассейна
с арочной (цилиндрической) светопрозрачной кровлей (площадь кровли ~280
м2) начался монтаж стеклопакетов из гнутого закаленного стекла, которые
использовались в качестве элементов остекления. Формула стеклопакетов:
(прозрачное закаленное 6М1)–(18 воздух)–(6К с твердым низкоэмиссионным
покрытием, закаленное).
По замыслу архитектора полностью прозрачная цилиндрической формы трехсекционная
кровля сооружения (см. рис. 1) должна была зрительно увеличить объем
внутренних помещений, обеспечить визуальную связь с окружающей ландшафтной
средой, освещенность помещения естественным светом практически в течение
всего дня, плавность линий и оригинальность проекта в целом.
На стадии строительного проектирования в качестве несущих конструкций
были использованы системные фасадные профили из алюминиевых сплавов компании
«Schuco International» (Германия). Вантовая несущая конструкция кровли
прошла соответствующую экспертизу на прочность, жесткость и пространственную
неизменяемость (устойчивость) и была принята к производству.
Стеклопакеты были спроектированы, исходя из проектного радиуса кривизны
гнутых алюминиевых профилей ферм (стоек) и были изготовлены на производстве
по обработке стекла с использованием гравитационного метода осаждения
стекла в процессе термического нагрева в печи в металлическую неподвижную
негативную форму и последующего охлаждения вне печи в «чиллере».
После монтажа стеклопакетов на кровле сооружения начался процесс их саморазрушения.
Разрушения носили спонтанный и хаотический характер, происходили в различное
время суток и на различных участках кровли. Разрушалось только наружное
прозрачное стекло. Были рассмотрены и проанализированы возможные причины
и механизмы разрушения закаленного стекла.
Самопроизвольное разрушение остекления, в том числе одинарных гнутых закаленных
стекол, панелей из многослойного моллированного термоупрочненного стекла
в различных строительных проектах, при возведении и эксплуатации светопрозрачных
фасадных и кровельных конструкций является серьезной проблемой. Эта проблема
обсуждалась на прошлой конференции GPD-2007 в докладах [1], [2], [3] и
не потеряла свою актуальность и на сегодняшний день.
Таблица 1. Геометрические параметры применяемых стеклопакетов
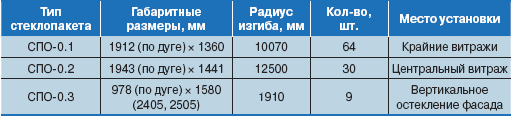
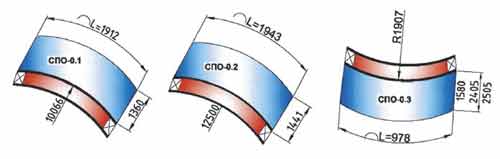
Конструкция кровли
В конструкции несущей части кровли (см. рис. 2) использовались алюминиевые
профили со строительной глубиной (высотой) 175 мм, шириной 50 мм и толщиной
стенки 6 мм из фасадной системы «Schьco FW50+». В качестве ригелей — алюминиевые
профили размером 110 Ч 50 мм и толщиной стенки 10 мм. Конструкция кровли
состояла из трех секций: центральный витраж с радиусом дуги R = 12,48
м (по внешней поверхности); количество ферм — 6 шт., каждая ферма состоит
из трех частей, размер в проекции — 12,7 м. Периферийные витражи — северный
и южный с радиусом дуги R = 10,04 м, количество ферм 5+5 шт., каждая ферма
из 3-х частей, размер в проекции — 14,1 м.
При экспертизе и обследовании объекта строительства было установлено,
что гибка исходных алюминиевых профилей происходила без должного контроля,
на неаттестованном технологическом оборудовании, без оформления паспортов
качества и определения допустимых отклонений по геометрическим размерам
отдельных секций несущих ферм, в частности, по радиусу дуги. Это в итоге
привело к соответствующим сложностям при сборке составных ферм. Практически
не только каждая ферма, но и ее отдельная секция имели свой индивидуальный
радиус изгиба, который по предельным отклонениям не всегда соответствовал
проектным решениям и не был учтен при изготовлении стеклопакетов. Это
первая ошибка при реализации проекта.
![]() Рис. 3. Северная сторона фасада. Видны места крепления прокладок из EPDM саморезами через металлические прокладки |
![]() Рис. 4. Северная сторона фасада. Виден деревянный настил-лестница для монтажа остекления |
Конструкция стеклопакетов
Для остекления кровли были изготовлены однокамерные стеклопакеты формулы:
(6М1, прозрачное закаленное)–(18, воздух)–(6К, с твердым низкоэмиссионным
покрытием, закаленное) трех типоразмеров (см. табл. 1).
Монтаж стеклопакетов
Установка стеклопакетов на кровле была осуществлена в период с октября
по ноябрь 2006 года с целью закрытия теплового контура здания. Монтаж
изделий производился, начиная снизу вверх по вертикали и продолжая по
горизонтали, по временной схеме: укладка стеклопакетов на стоечно-ригельную
рамочную конструкцию из алюминиевых профилей на штатные уплотнительные
прокладки из EPDM по всему периметру рамы с точечной механической фиксацией
стеклопакета саморезами через металлические прокладки (см. рис. 3) по
кромке с наружной стороны (от 2 до 4 точек). Герметизация и уплотнение
узлов примыканий при этом не производились.
И хотя монтаж осуществлялся с применением подъемного крана и специальной
траверсы с вакуумными присосками, рабочие-монтажники поднимались на кровлю
по лестницам, которые опирались на поверхность ранее смонтированных стеклопакетов
(см. рис. 4).
Монтаж по осуществленной схеме — это вторая ошибка при реализации проекта.
Таблица 2. Таблица-протокол
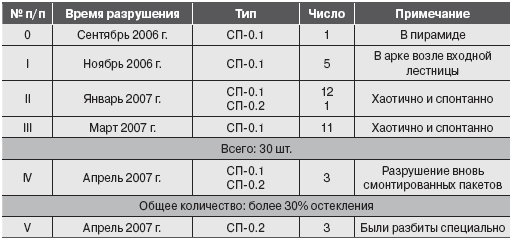
Разрушение стеклопакетов
Через три дня после окончания монтажа стеклопакетов, т.е. с октября 2006
г., начался процесс их спонтанного разрушения (растрескивания), который
продолжался до июня 2007 года. Разрушения носили по месту расположения
стеклопакетов хаотический характер и никакой закономерности не было выявлено
(см. фото на рис. 5).
Разрушалось только наружное прозрачное закаленное стекло, стекло разрушалось
на мелкие фрагменты в виде «сетки», которые имели вытянутую форму вдоль
дуги изгиба стекла (рис. 6). Разрушений внутреннего закаленного стекла
с твердым низкоэмиссионным покрытием не наблюдалось. После замены поврежденных
стеклопакетов процесс разрушений продолжался, причем разрушались и заново
смонтированные стеклопакеты.
До мая 2007 г. включительно общее число разрушившихся стеклопакетов составило
31 единицу (более 30% от общего числа), причем только 2 стеклопакета были
типа 2 (СПО -02), которые устанавливались в центральной части кровли (табл.
2).
Производитель стеклопакетов утверждал, что все партии поставленной однотипной
продукции изготавливались при одинаковых технологических режимах нагрева
и охлаждения исходных стекол-заготовок с использованием одних и тех же
статических форм-изложниц моллирования на одном и том же оборудовании
в соответствии с рекомендациями производителя оборудования.
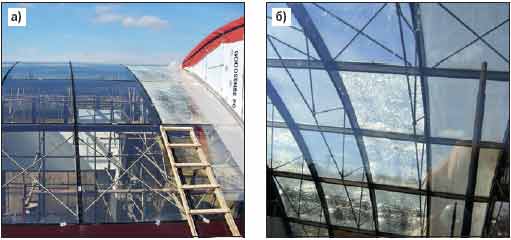
Рис. 5. Характер трещин и разломов стекла при саморазрушении:
а) центральный фасад, б) вид на трещины северного фасада изнутри
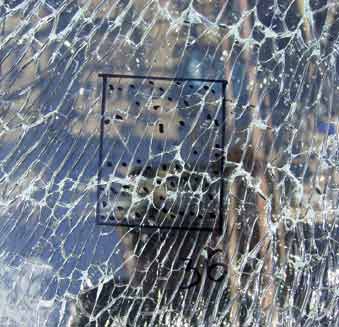
Рис. 6. Рисунок трещин стекла, характерный для закаленного стекла
Причины разрушения

Результаты внешнего визуального осмотра разрушившихся стеклопакетов, проведенного как на кровле, так и после демонтажа изделий, не выявили причину разрушения. Внешние механические повреждения (следы от ударов) на наружных стеклах отсутствовали.
При транспортировании и хранении соблюдались все необходимые меры, исключающие воздействие внешних нагрузок (кроме собственного веса) на моллированные стеклопакеты. Во время хранения на строительной площадке разрушился только один стеклопакет.

Стеклопакет при монтаже на кровле должен был опираться на уплотнительные прокладки из эластомера, установленные по всему периметру рамы из алюминиевых профилей и исключающие контакт моллированного стекла с металлом. Однако результаты обследования показали, что для части стеклопакетов это условие не выполнялось. Внутреннее стекло опиралось на подкладки только средней частью вдоль гнутых сторон из-за несоответствия радиусов изгиба стеклянных панелей и алюминиевых профилей. Зазор между кромкой короткой стороны нижнего стекла и прокладкой составлял от 2-3 мм до 5 мм. Как уже отмечалось выше, использованный способ монтажа предусматривал временное закрепление изделий на крыше на период зимних холодов с помощью точечных винтовых креплений на кромках стеклопакетов с механическим устранением зазоров. Это могло приводить к неконтролируемым опасным напряжениям на кромках стекла. Отметим, что при изготовлении изделий кромки стекол не обрабатывались.

Ветровых экстремальных нагрузок не было. Снег и нагрузки от обледенения можно исключить. Критических отрицательных температур также не было. Изменения атмосферного давления не контролировались, однако они не превышали обычных среднесуточных значений по данным метеоконтроля для этой поры года.

Инспекция производства показала, что изготовление моллированных стекол осуществляется на печи моллирования и закалки с использованием метода термического нагрева стекла и его гравитационного формования в металлическую статическую негативную форму (см. рис. 7). Детальный анализ недостатков данного метода изготовления моллированного стекла приведен в работах [1,3].
Так как производство не располагает соответствующими инструментальными методами контроля внутренних напряжений в стекле, были проведены только качественные исследования напряжений в поляризованном свете. Результаты исследований свидетельствовали о том, что в моллированном прозрачном стекле распределение напряжений имеет неравномерный и неоднородный характер, на поверхности стекла имеются ярко выраженные локальные напряжения растяжения.
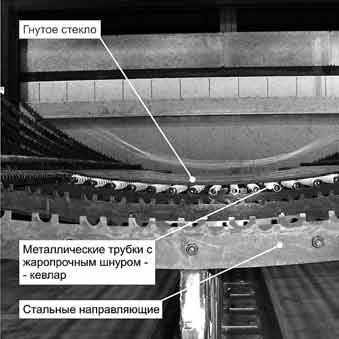
Рис. 7. Форма для гнутья стекла
Нормативная база
В настоящее время не существует российского нормативного документа на
моллированное термоупрочненное и (или) закаленное стекло, впрочем, нам
неизвестны и европейские нормы, где были бы установлены требования к изделию,
его характеристики, например, степень закалки, допустимые напряжения сжатия-растяжения
и т.п., правила приемки и, главное, методы контроля, испытательное оборудование
и средства количественных измерений. Отметим, что в России термин «термоупрочненное
стекло» не определен никакими официальными нормами, равно как и область
его применения, характеристики, требования к технологическому процессу
производства и др.
Существующий государственный стандарт на закаленное стекло ГОСТ 30698-2000
[4] не содержит, к сожалению, требований и характеристик, позволяющих
оценить качество закалки с позиций прочности и устойчивости стекла к воздействию
эксплуатационных нагрузок. Положение усугубляется также отсутствием норм
на проектирование изделий из закаленного и моллированного стекла, способы
монтажа стеклопакетов из таких стекол при устройстве светопрозрачных фасадных
конструкций и покрытий. И здесь мы можем согласиться с мнением господина
M. Eckhout [1], что каждый раз при реализации строительного проекта с
применением специальных архитектурных стеклопакетов больших размеров,
в том числе из моллированных закаленных стекол, мы вынуждены проводить
дорогостоящие «продуманные натурные испытания на спонтанные разрушения
(своего рода, Heat Soak Test), что для моллированного стекла не предусмотрено».
Исправление ситуации. Замена стеклопакетов
Возможные механизмы и причины разрушения моллированных термоупрочненных
стекол (пластин) обстоятельно и достаточно наглядно приведены в работах
[1, 3]. В нашем случае не имелось возможности заказать новые стеклопакеты
у другого производителя, обладающего другим оборудованием и другим методом
моллирования стекла.
По требованию заказчика компания, осуществлявшая строительное проектирование
и монтаж светопрозрачной кровли, и производитель моллированного стекла
и стеклопакетов на основании соответствующего соглашения подготовили программу
совместных работ и создали рабочую группу из представителей обеих компаний
с приглашением независимых экспертов (февраль 2007 г.) с целью изготовления
новой партии стеклопакетов и замены тех, которые разрушились. Заметим,
что на основании изучения Программы конференции GPD-2007 было принято
решение об участии в работе данной конференции одного из экспертов (Станислав
Тихомирнов). Необходимо отметить, что данное решение оказалось очень полезным,
своевременным и полностью оправдало себя как в научно-техническом, практическом,
так и в финансовом аспектах.
Основное содержание данной совместной акции состояло в следующем:
Проектная документация: анализ, оценка и корректировка технических
решений по несущей и светопрозрачной конструкциям кровли, в том числе
допускам по геометрическим размерам и форме, с учетом воздействия эксплуатационных
нагрузок — ветровой, собственного веса, с учетом изменений температуры
наружного воздуха и атмосферного давления.
Производство моллированного стекла: ревизия и наладка печи для
моллирования и закалки, оптимизация режимов термического нагрева и охлаждения,
контроль температуры в печи, равномерности нагрева поверхности стекла,
контроль температуры стекла в момент его подачи в секцию охлаждения, контроль
момента проседания разогретого стекла в форму моллирования.
Контроль качества моллированного стекла: детальный контроль пороков
стеклянных пластин, состояния кромок, геометрических размеров и их номинальных
отклонений; изготовление изделий малыми партиями (не более 11 штук), контроль
характера разрушения на малоразмерных образцах стекол при обработке режимов
нагрева и охлаждения и на одном полноразмерном стекле из каждой партии,
сплошной контроль по радиусу изгиба, включая краевые области (прямые кромки),
испытания на ударные и другие нагрузки.
Производство стеклопакетов: подбор по радиусу изгиба пары — наружное
и внутреннее стекло; оптимизация технологии сборки, контроль геометрических
размеров по индивидуальным шаблонам (для каждой секции кровли), идентификация
и маркировка каждого изделия, приемочные испытания при участии представителя
заказчика.
Монтаж: свободная укладка стеклопакетов на каркасе кровли, устранение
обнаруженных зазоров с помощью силиконового герметика, стабилизация формы
смонтированных стеклопакетов под действием собственного веса в течение
24 часов. И только потом — окончательная герметизация и установка декоративных
профилей.
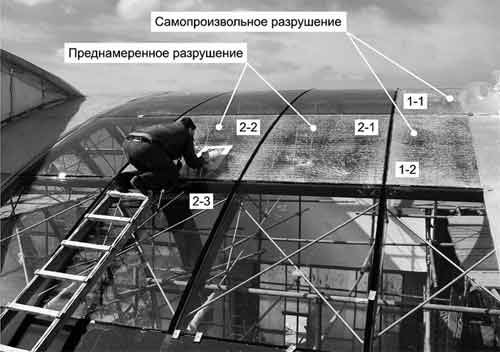
Рис. 8. Преднамеренное разрушение после монтажа
Заключение
Всего было изготовлено вновь 64 стеклопакета (СПО-01) с радиусом изгиба
10070 мм и 5 стеклопакетов (СПО-02) для центральной секции кровли с радиусом
изгиба 12500 мм.
Так как на центральной секции кровли за 8 месяцев с момента установки
разрушилось только 2 стеклопакета, было решено с целью самопроверки провести
выборочное преднамеренное механическое разрушение 3-х стеклопакетов СПО-02
непосредственно на кровле с целью оценки характера разрушения и косвенного
установления полноты (степени) закалки наружных стекол (см. рис. 8).
По результатам данных испытаний было решено о замене 5-ти дефектных стеклопакетов
на вновь изготовленные, остальные стеклопакеты оставить на месте.
Окончательная замена стеклопакетов на кровле была завершена в сентябре
2007 г. (рис. 9).
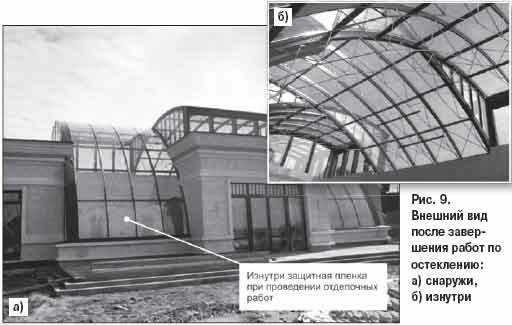
Выводы
Использованное производителем оборудование и метод гравитационного формования
моллированного стекла при нагреве в неподвижную металлическую форму приводит
к неоднородному прогреву стекла как по поверхности, так и в толще. Это
приводит к возникновению локальных напряжений растяжения на выпускной
поверхности стекла, которая контактирует с элементами стальной формы,
снижению прочности стекла при изгибе.
Процент саморазрушения стеклопакетов из моллированного закаленного стекла,
первоначально смонтированных на кровле бассейна, превысил 30%. Причины
разрушения состояли в ошибках в технологическом процессе производства,
в неправильном выборе оборудования и метода моллирования, в ошибках при
монтаже.
Случаи разрушения остекления в строительных проектах, в том числе из моллированного
закаленного или термоупрочненного стекла, далеко не единичны, они происходят
в разных местах, в различное время и могут привести к серьезному материальному
ущербу, нанести вред здоровью и жизни людей.
Разработка нормативных документов на моллированное закаленное и термоупрочненное
стекло и изделия с его применением является актуальной задачей, в которой
заинтересованы архитекторы, проектировщики, компании-производители фасадных
конструкций, строители и заказчики-инвесторы.
Процесс моллирования и закалки стекла в статической металлической форме
— сложная и трудоемкая задача, предъявляющая высокие требования к уровню
профессиональной подготовки, мастерству и ответственности персонала, к
организации технологического процесса. И, тем не менее, данный метод позволяет
при выполнении определенных условий производить изделия из архитектурного
моллированного стекла, пригодные с определенной степенью риска к применению
в строительстве.
Данный случай разрушения моллированных стеклопакетов в конструкции арочной
кровли можно сравнить с незапланированным дорогостоящим натурным испытанием
по определению устойчивости остекления к внешним нагрузкам.
Ссылки
Mick Ekhout, Stepphan Niderehe. Spontaneous glass breakage in hot bent,
heat-strengthened, laminated glass panels. Glass Performance days 2007,
p. 679
Jurgen Neugebauer, Gerhard Espich. Geometrical transformation of glass.
Glass Performance days 2007, p. 708
J.V. Colvin. The analysis of bent heat treated glass breakages. Glass
Performance days 2007, p. 685
ГОСТ 30698-2000 «Стекло закаленное. Технические условия»
С. Тихомирнов, с.н.с., к.т.н., А. Шеховцов, магистр,
Научно-исследовательский институт строительной физики Российской Академии
Архитектуры
и Строительных наук (НИИСФ РААСН), Москва, РФ. Доклад на GLASS PERFORMANCE
DAYS 2009, Тампере, Финляндия