«Традиционными» материалами для применения внутри жилища
давно стали цельная или клееная составная древесина и композиты на базе
цельной древесины — сэндвич-панели, паркетная доска, ДСП, фанера и MDF.
Сейчас пришло время для массового применения внутри жилища «нетрадиционных»
материалов. Этому есть ряд причин, одна из них — сокращение лесонасаждений
и дороговизна изделий из выскосортной древесины и связанная с этим необходимость
более полного использования древесной массы — от веток и тонкомеров до
пней, щепы, стружки, опилок и сучковатых фрагментов, отбракованных при
производстве клееных бессучковых погонажных изделий и брусьев, а также
для утилизации б/у древесины.
Тот факт, что при изготовлении фасонного пиловочника в мелкофракционные
опилки и стружку уходит на разных этапах от 15% до 50% древесной массы,
определяет необходимость продуктивного использования отходов процессов
пиления и строгания на новом уровне.
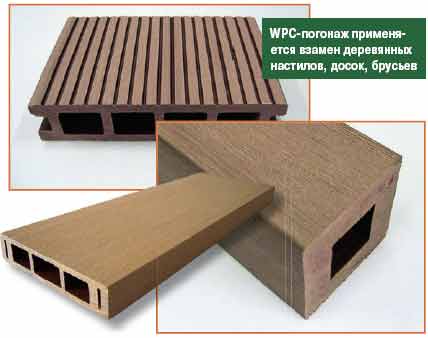
Все большее лидерство в применении для напольных покрытий,
в качестве погонажа для финишных работ (плинтусы, наличники, внутренние
и наружные уголки, молдинги, рустик, раскладки и т.п.) и для отделки жилья
и офисов, для изготовления встроенной и корпусной мебели занимает WPC
— Wood-Plastic-Composites (Дерево-Пластик-Композит).
Мы уже писали о WPC в подробной статье (см. «Окна.Двери.Витражи», №1-2007,
стр. 112-116). Этот композитный материал состоит из смеси древесной пыли
или микроволокон древесины и пластической массы, обычно PP (полипропилен),
PE (полиэтилен), ABS (акрилонитрил-бутадиен-стирен, АБС), PVC (ПВХ) или
PS (полистирен).
В соответствии с результатами исследований, проведенных исследовательской
группой Principia Partners (США), WPC были разработаны и начали бурно
применяться в начале 50-х годов прошлого века, когда в автомобильной индустрии
начали применять добавки из древесной муки в пластиковую массу для изготовления
стабильных жестких, прочных и легких настилов в багажниках легковых машин
и в кузовах пикапов, для направляющих сдвижных дверей, для объемных деталей
сидений и внутренней отделки дверей. Позже, в 80-х, благодаря изысканиям
Mobil Oil (США), появился материал под маркой Trex для траповых и палубных
настилов. Сейчас декинг (траповые и палубные настилы) продолжают оставаться
для WPC сферой применения №1.
Развитие в области деревообработки и появление новых поколений машин для
производства WPC-изделий привели к огромному росту возможностей применния
этого материала, отмечает Лу Росси (Lou Rossi), директор программы WPC
фирмы Principia Partners (США). Особый рост интереса наблюдается в использовании
декоративных накладок, отделочных панелей, мебели и деталей для нее, других
прикладных изделий, сделанных из этих композитов (см. таблицу). По данным
Principia Partners общий объем реализации WPC-изделий превысил в США $1000
млн. еще в 2002 г., а к 2010 г. превысит $10 млрд. — это настилы, погонаж
и штучные изделия.
В рамках дискуссии, которая разгорелась 21 января на VI Международном
Конгрессе «ОКНА. ДВЕРИ. ФАСАДНЫЕ СИСТЕМЫ 2009», соорганизаторами которого
выступили Министерство регионального развития и строительства Украины
и Институт ift Rosenheim (Германия), был поднят немаловажный вопрос —
а насколько WPC экологичны, начиная с производства, во время эксплуатации
и при утилизации/переработке? В этой статье мы попытаемся дать ответ и
на вопрос об экологичности этого безусловно перспективного материала.
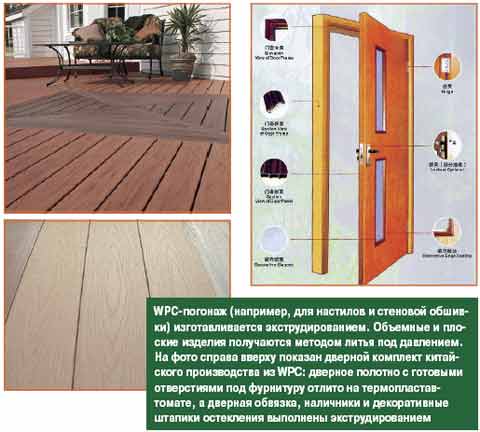
Перемещаясь снаружи внутрь
Один из примеров использования WPC в интерьере — материал EinWood Composite,
который был разработан EIN Engineering, США, и использовался в качестве
отделочных панелей, полов, настилов и профилей. Сейчас этот материал по
лицензии выпускается в Японии и сертифицирован по всем строительным и
гигиеническим нормам для рынка Северной Америки благодаря усовершенствованиям
Inteque Resources.
«Материал выпускается методом экструзии или налива с последующей прокаткой
и помимо профилирования в размер может быть колерован и текстурирован
для точной имитации любых сортов древесины, что важно для погонажных и
листовых отделочных изделий», — поясняет Томо Сакагучи (Tomo Sakaguchi),
управляющий компании Inteque Resources. «Материал EinWood composite по
свойствам скорее похож на дерево, чем на пластик: обычный состав — 55%
древесины и 45% пластика по весу. Объемное же содержание древесины превышает
80%», — добавляет Сакагучи.
Благодаря имеющимся возможностям на рынке, продолжает Сакагучи, «…мы прогнозируем
увеличение объемов продаж отделочных изделий такого типа. Меняя количество
древесной муки и степень обжатия, мы можем добиться различной твердости
поверхностного слоя, которая будет много тверже поверхности у обычной
древесины. Подмешивая к древесной субстанции, к примеру, полипропилен,
мы добиваемся такой твердости поверхности, которая значительно выше, чем
у любой экзотической породы или чем у других композитных материалов. С
учетом малого влагопоглощения, характерного для WPC, это открывает новые
возможности для применения внутри интерьеров жилищ — для кухонь, ванных
и мест с повышенной влажностью, например, в подвальных помещениях».
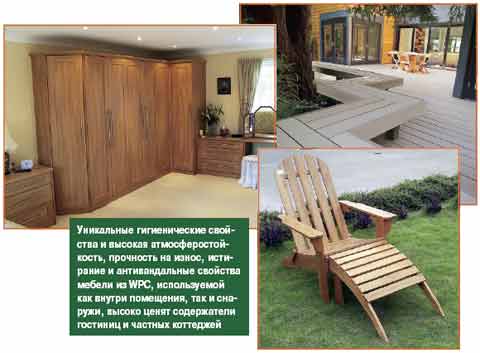
«Думается, такая отрасль, как производство окон и дверей пока еще недостаточно
обратила свое внимание на WPC, зациклившись на «чистых по составу» материалах
— дереве, пластике или металле», — выразил свое мнение Терри Лэйер (Terry
Layer), президент Strande Corn., другого разработчика технологии производства
WPC. «Преимущества использования WPC в том, что мы получаем конечные изделия
более высокого качества, но в большинстве случаев по меньшей цене. Если
вы заменяете изготовление множества деревянных деталей для оконной рамы
или двери простым экструдированием профиля нужного сечения, то экономия
в приложении к конечному изделию оказывается огромной». Утверждение Терри
тем более актуально, если учесть, что цены на пластик и холоднокатаный
металл для усилителей, высокосортный бессучковый клееный брус из древесины
и алюминиевый профиль постоянно растут.
«Наши потребители заказывают такие изделия, как лестничные сходни, перила,
наличники, плинтусы, пороги, поручни, балясины — профилированные или «точеные»
изделия, которые полностью заменяют деревянные детали из древесины любого
сорта», — говорит Билл Кростик (Bill Crostic) президент фирмы Onaga Composites
LLC, имеющей свое развитое научно-исследователькое подразделение. Изюминка
технологии Onaga в том, что для приготовления композита используются обычные
древесные топливные пеллеты в смеси с чистым полиэтиленом или полипропиленом
для последующего экструдирования или формовки в литьевой машине. «Мы используем
древесную муку из определенного сорта дерева только как антифрикционную
присадку в процессе экструдирования или литья под давлением подобно тальку
или доломитовой муке. Но она формирует практически неотличимый от натуральной
древесины поверхностный слой», — говорит Кростик.
«Преимущество WPC кроется в высоких технологических свойствах пластика.
Вы можете например сформовать филенчатое дверное полотно нужного размера
и дизайна без какой бы то ни было последующей механической обработки.
Изделие в итоге может быть плоским, раскатанным в лист. Все, что можно
делать с пластиком, можно делать и с WPC. Важно — у WPC более высокая
жесткость на единицу веса, чем у пластика или у дерева!», — добавляет
Билл.
Кростик разъясняет, что чем выше «закладка», т.е. концентрация волокон
древесины в WPC, тем меньше проявляются вязкие и нежесткие свойства пластика,
его текучесть и релаксационные свойства со временем. Для изделий, которым
требуется высокая жесткость, весовая закладка древесины составляет от
50% до 70%. Изделиям, которым нужна большая гибкость и нежесткость (плинтусы
или молдинги, например) свойственно большее содержание пластмассы.
Таблица. Спрос на погонаж из дерева и его заменителей (млн. погонных
футов) в США

Сравнение характеристик: дерево и древесный композит
Способность «манипулировать» жесткостью изделий — это еще одно преимущество,
обнаруженное производителями WPC. По информации фирмы Principia Partners,
WPC имеют множество других характеристик, которые не имеет цельная древесина
или традиционные клееные материалы из дерева. Например, добавки к пластику
помогают WPC-изделиям сопротивляться насекомым и грибку, делая их практически
идеальными для применения в качестве погонажных деталей для изготовления
дверей и окон. Вдобавок, WPC-материалы практически не поглощают влагу
и по сравнению с деревом имеют значительно бoльшую стабильность размеров:
будучи однажды экструдированными, длинномерные детали не коробит, не ведет,
они не растрескиваются и не расщепляются.
«WPC-изделия весьма недороги в производстве, но продаются несколько дороже,
чем их аналоги из дерева. Но материалы из WPC значительно легче обрабатывать
и меньше риска их повредить (расколоть, расщепить, меньше отходов и т.д.),
т.е. индивидуальное изделие вместе с установкой зачастую обходится дешевле
деревянного», — таково мнение Лу Росси из Principia Partners. «Дверям
или панелям из WPC начительно легче придать «обрамленный» вид с помощью
накладных молдингов или резных филенок, чем выполнить то же, но из дерева».
Одно из последних направлений деятельности WPC-фирм — это отделочные панели.
По мнению докладчиков на Международной конференции по древесно-волоконным-пластиковым
композитам — Роберта Фалька (Robert H. Falk, USDA Forest Service, инженер),
Дэна Воса (Dan Vos, инженер из Berger/Abam Engineers), Стивена Крамера
(Steven M. Cramer, профессор кафедры гражданского строительства и экологической
инженерии, Университет штата Висконсин, США) — WPC намного лучше панелей
из дерева или из других известных деревосодержащих композитов.
Материал, который они исследовали, состоял из «стандартной» для WPC смеси
из 50% гранулированной до размера 40 мэш (40 отверстий на дюйм длины сита
в сортировочном грохоте, т.е. размер гранулы около 430 мкм — прим. ред.)
древесной муки из сосны и 50% по весу полиэтилена низкого давления или
полипропилена, продавленной через фильеры на двухвинтовом экструдере фирмы
North Wood Plastics Inc. Смесь изменяли, достигая весового соотношения
древесной массы к пластику от 20% до 60%. Изделие — панель толщиной 0,5
дюйма и размерами 20?Ч?20 дюймов, произведенная в Forest Products Laboratory
— сравнивалось с клееной фанерой, OSB, ДСП, ДВП и MDF.
Исследование состояло в определении характеристик и поведении материала
в качестве отделки интерьера, изучались изменения модуля упругости и модуля
изгибной жесткости до момента разрушения и коэффициент теплового расширения.
Однако, из-за высоких предела прочности на разрыв, предела прочности при
сдвиге и показателях жесткости, WPC-панели оказались на уровне лучших
показателей для других типов панелей на древесной основе, а в общем сочетании
— их характеристики превышают данные для всех остальных типов плит. Наилучший
показатель — влагопоглощение как изменение веса при погружении в воду
на 24 часа — максимум 1% против 40% у древесных плит. Исследование также
показало, что только MDF-панели имеют стабильность характеристик, сопоставимую
с WPC-панелями разного состава.
![]() Одновинтовой экструзионный агрегат |
![]() Конический двухвинтовой экструдер |
Особенности производства WPC
Характеристики получаемых WPC-изделий часто зависят от способа их производства.
Обычно эти материалы производят методами экструзии на экструзионных машинах
или литья под давлением на термопластавтоматах.
В типичном экструзионном процессе необходимая концентрация древесной массы
достигается смешиванием с гранулами высковязкого пластика. Волоконные
добавки, которые служат для армирования материала, подмешиваются в компаунд
«дерево-пластик», и все вместе затем продавливается через стальную фильеру
экструдера.
Отклонение от технологии приготовления смеси может привести к несоответствию
в конечном результате. «Когда имеется два различных типа смешиваемых материалов,
таких как дерево и пластик, без необходимой тщательной подготовки смеси
можно получить брак», — говорит Джон Ши (John Shea, президент Canon &
Shea Assoc.), который представляет поставщиков сырья для этой отрасли.
«Кручение и прогибы, непостоянство сечения по длине профиля случаются
обычно тогда, когда экструдируемая масса была недостаточно перемешана
и не была достаточно «гомогенизирована» в процессе производства».
Дополнительные приемы обработки могут быть в итоге полезны. «Инструмент
Quill’s Equaflow, например, расщепляет общий поток перед головкой на отдельные
закрученные в пучок струи таким образом, чтобы добиться большей равномерности
распределения смешанного материала по сечению перед фильерой, что сказывается
на стабильности размеров экструдированного изделия», — поясняет Ши.
В большинстве случаев технология отработана и по лицензии передается производителю.
Так, технология композитов EinWood перед смешиванием в экструдере предполагает
высушивание муки до 0% влажности. Она также предполагает предварительное
смешивание и сплавление большого количества муки и малого количества пластика,
затем используется процесс тиксотропной экструзии (обратимый переход вязких
гелей в жидкое состояние при механическом воздействии — прим. ред.) «заготовок»
с остальным количеством пластика на высокопроизводительных экструдерах.
А, например, техпроцесс фирмы Strandex, по словам Терри Лэйера, был разработан
на основе использования уникальной экструдерной головки и особой рецептуры
компаунда. В целом, смесь по этой рецептуре содержит помимо высокого содержания
древесной муки и целлюлозных волокон термопластичную смолу и специальные
присадки, улучшающие реологию экструдируемой массы.
Древесная мука: основной ингредиент WPC
В древесную муку добавляются такие пластмассы, как PP (полипропилен),
PE (полиэтилен), ABS (акрилонитрил-бутадиен-стирен, АБС), PVC (ПВХ) или
PS (полистирен). Естественно, к основному компоненту WPC предъявляются
особые требования.
Их разъяснил Фрэд Фахнер (Fred Faehner), президент фирмы P3 Murphy Forest
Products Corp. «Древесная мука — это хорошо перетертая целлюлозная масса
из дерева с размером зерен порядка 20 мэш (что-то около 850 мкм). Чем
выше число мэш, тем размер зерен меньше».
Обычно мука изготовляется из древесины твердых пород, именно ее предпочитают
производители WPC-изделий. «Это связано с тем, что древесина более мягких
пород, например, хвойная, содержит много ароматических веществ — легко
горючих органических соединений, которые могут воспламениться при повышении
давления в экструдере», — поясняет Фахнер. «Предварительная сушка муки
до содержания влажности менее 1% помогает в производстве». Дополнительные
приемы, которые испоьзуюся в P3 Murphy Forest Products Corp. включают:
Всегда поддерживать как можно более низкую температуру техпроцессов. Во
избежание воспламенения муки рекомендуется температура ниже 200°С.
Всегда создавайте необходимый уровень вентиляции. Влага и пары, выделяемые
в процессе экструдирования, должны свободно покидать экструдер, иначе
нужно снижать температуру и давление.
Повышение индекса текучести расплава смолы уменьшает уровень тепла, выделяемого
на винтовой паре при сдвиге смешиваемых пластов муки и пластика. Также
полезно создавать 2 или 3 зоны смешения по длине винтов в смесителе. Б?льшая
равномерность распределения компоненотов при смешивании снижает температуру
в смесителе.
«Двухвинтовые экструдеры предпочтительнее одновинтовых», — считает Фахнер.
«Однако, если используется одновинтовая машина, то предполагается, что
применяют гранулы или пеллеты из заранее подготовленного компаунда».
Экструдирование отходов древесины
Критический фактор WPC-производства, по мнению Криса Венриха (Chris Weinrich,
ExtrusionTek Milacron), — это подгонка геометрии винтов экструдера к свойствам
компаунда, оптимизация температуры и скорости вращения так, чтобы сбалансировать
поток на законцовке винтов экструдера с течением в фильере.
В соответствии с каждой рецептурой внешние процессы подачи, смешивания,
оплавления, гомогенизации, обжатия должны быть синхронизированы со скоростями
внутренних процессов в обрабатываемом материале, чтобы на выходе получить
бездефектное изделие.
Одна из технологий экструдирования WPC использует конические двухвинтовые
машины. Конические двухвинтовые экструдеры были спроектированы для подачи
под давлением ворсистых, распушенных комочков древесных волокон. От винта
к винту траектория движения одинакова на всем пути к фильере, и частицы
древесной фибры по мере движения уменьшают расстояние между собой. Естественное
обжатие в конической машине сопровождается эффективным смачиванием волокон
полимером. Частицы древесины, будучи полностью покрыты пластиком, позволяют
задавать максимальный вакуум в зоне дегазации расплава без предварительного
вакуумирования массы из муки и древесной фибры.
Такой подход позволяет эффективно использовать древесную массу, полученную
от переработки кустарников и щепы после рубительных машин. То есть, можно
использовать древесную массу, полученную из щепы тонкомера и веток при
расчистке леса и вырубке быстрорастущих кустарников вдоль речных стариков,
в поймах и дельтах рек, а также щепу из вторичного древесного сырья, в
т.ч. из б/у деревянных изделий и строительного деревянного мусора, образованного
при строительстве или после природных катаклизмов, например, ураганов,
наводнений и торнадо. Такой опыт имеется у Fibertec inc., Флорида, занимающейся
выпуском гранул (сырья для WPC-экструзии), где древесная масса получена
в основном после переработки быстрорастущих кустарников после расчистки
берегов многочисленных там малых водоемов. А в Южной Каролине местная
власть даже доплачивает, если фирмы берутся вывезти для утилизации сучья
и ветки после расчистки местных лесов из ценных пород дерева.
Машинный фактор
По мнению Джона Куармли (John Quarmley), директора Principia Consulting,
одна из важнейших характеристик WPC состоит в том, что их механическая
обработка (и необходимый станочный парк) полностью подобна применяемой
при традиционной деревообработке.
«Вы можете пилить, строгать, забивать гвозди, ввинчивать шурупы, сверлить
и фрезеровать, клеить, крепить клямерами или скобами, как будто вы имеете
дело с цельной древесиной»… «Множество научно-исследовательских и опытно-конструкторских
разработок в области WPC-производства сейчас ведется в направлении разработки
особых добавок в экструдируемую массу, которые образуют внутри WPC-изделия
очень твердую и мелкозернистую пенистую структуру. То есть внутри WPC-детали
имеется огромное количество мельчайших пузырьков — ячеек с воздухом —
и таким образом WPC теперь становится еще более подобным однородной древесине
(липа, бук), в том числе и по поведению при ее механической обработке».
Говоря общо, тот же самый инструмент с твердосплавными пластинами, быстрорежущая
сталь или алмазный инструмент, которыми работают по пластику и дереву,
можно успешно использовать и для обработки WPC. «Вы даже можете специально
сделать изъяны и провести искусственное механическое старение, чтобы придать
поверхности более изысканный с точки зрения дизайнера вид старой глубоко
текстурированной древесины», — делится опытом Маурин Мюррэй (Maureen Murray),
спикер из Trex Co.
«Из-за высокого содержания древесной муки при фрезеровании фасонной поверхности
WPC-изделия вы можете слышать запах именно древесины, как и при обработке
собственно дерева», — добавляет Томо Сакагучи.
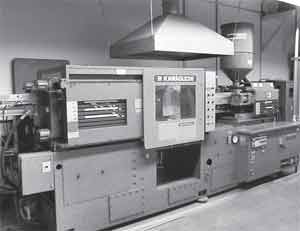
При использовании для литья под давлением древесной муки из хвойных пород, которая содержит значительное количество ароматических веществ — легко горючих органических соединений — термопластавтоматы должны быть оборудованы мощной местной вытяжкой
От скамьи к креслу
Фирма Deck Yard и Country Gardens в St. Charles, штат Иллинойс, была основана
в 1992 году Тедом Палпентом (Ted Palpant) и специализируется на изготовлении
различной садовой мебели, фурнитуры и ограждений, используемых снаружи
и во дворе дома. Палпент использует в своих иделиях смесь Trex Wood Polymer
для погонажа.
«WPC работает по большей части так же, как и дерево, особенно в смысле
применимости», — говорит Тед. «Его можно гнуть, профилировать, скруглять,
шлифовать, резать, т.е. придавать форму теми же методами, что и для дерева
— то есть легко и просто. Но поскольку водопоглощение у WPC практически
отсутствует, этот материал идеален для наружного применения и превосходит
дерево. Например, мы используем WPC-изделия для изготовления садово-парковой
мебели, настилов причалов, мебели и отделки в плавательных бассейнах.
Наша мебель практически постоянно находится на солнце во влажных условиях».
Это породило идею изготавливать мебель для дома, которая не требует ухода
и не боится наружной эксплуатации. Так в ассортименте его фирмы появились
кресла-качалки, которые можно установить на обдуваемой влажным бризом
террасе, комплекты стульев и кресел, используемые и в доме, и в саду.
«Я не думаю, что люди на самом деле стремятся покупать для своего сада
особую мебель, предпочитая иметь и в саду привычное удобство, создаваемое
домашней мебелью. Домашнюю WPC-мебель можно легко вынести в сад, не беспокоясь,
что она будет повреждена дождем или сыростью…»
![]() Популярный у изготовителей мелкого WPC-литья термопластавтомат среднего класса марки ARBURG немецкого производства |
![]() Немецкая фирма Battenfeld выпускает мощные термопластавтоматы со сдвоенной системой смыкания пресс-форм, например, для изготовления дверных полотен, а также специальные WPC-головки для экструдеров |
Заполнение ниш
В местечке Arden, Северная Каролина, где находится производственная база
фирмы Atlas Precision, нашли новую рыночную нишу для своего бизнеса по
производству изделий методом литья под давлением. Используя готовые гранулы
из древесной муки и смеси полиэтилена и полипропилена от производителя
этого сырья, компании Onaga Composites, фирма Atlas Precision выпускает
разнообразную дверную отделочную фурнитуру, пороги и ступени по заказу
сети магазинов изделий для дома Lowe’s home center.
Фирма Atlas Precision подвела итоги нового бизнеса примерно через восемь
месяцев. Менеджер по продажам Роберт Булла (Robert Bulla) говорит: «Наш
успех мы во многом связываем с тем, что заняли определенную нишу в рынке
и смогли резко снизить стоимость прикладных материалов и специализированных
деталей, которые используются в установке дверей, отделке входных групп
и обустройстве крыльцевых ступеней и поручней, в т.ч. для внутренних лестничных
пролетов. Идея использования для этой группы WPC-изделий для конструкционных
целей витала давно, но мы начали использовать композит не только для наружного,
но и для внутреннего применения.
Область, в которой Булла видит дальнейшее продвижение по замене цельного
дерева на WPC-детали, состоит не только в замене цельного дерева, используемого
для конструкционных целей (потолочные балки, дверные полотна и несущее
обрамление, укосины лестничных маршей и прочее), но и в замене на WPC
тех деталей для отделки помещений и мебели, которые ныне стали привычными,
будучи изготовленными именно из пластика (плинтусы, молдинги, раскладки,
завитки, криволинейные ручки и ножки шкафов, диванов, кресел и прочее).
«Методом литья под давлением мы можем предложить производителям мебели
те детали, которые с целью экономии теперь широко изготовляются именно
из пластика, но они будут выглядеть как деревянные. А тем изготовителям,
кто применяет детали из цельной древесины, мы можем предложить изделия,
которые будут гарантированно и легче, и прочнее, и затейливее, но дешевле,
чем цельнодеревянные резные детали». Он добавляет, что «можно к тому же
уменьшить обычную толщину деревянных стенок, перегородок, дверей, если
вместо дерева использовать современные WPC с микровспененной структурой».
На производстве Atlas Precision используется 34 единицы термопластавтоматов
фирм Toshiba и Arburg разного размера смыкаемой плиты и усилием от 38
до 720 тонн. Булла говорит, что в литьевых машинах они обычно используют
сырье с 50% весовым содержанием древесной массы, но поставщик может легко
изменить состав смеси по требованиям производителя так, чтобы как можно
полнее удовлетворить требования заказчика. Для этого производитель сырья
или производитель изделий должен инвестировать определенные средства в
специализированное смесительное оборудование. «Других ихзменений в технологическом
процессе и оборудовании для литья WPC-изделий на термопластавтоматах по
сравнению с обработкой чистых поластиков не требуется», — утверждает Булла.
«Мы установили у себя специальные смесители лишь для того, чтобы самим
оперативно изменять свойства изделий (жесткость, твердость, усилие резания)
по спецификации заказчика. Другое преимущество — мы можем колеровать изделия
в массе, а не только по поверхности, что важно для множества приложений
— например, половицы, ступени, поручни и т.п.)», — добавляет Булла.
Помимо термопластавтоматов Toshiba и Arburg у производителей WPC-изделий
весьма котируются аппараты германской фирмы Battenfeld, которая к тому
же выпускает специальные WPC-головки для экструдеров.
У финиша
«Изделия из WPC марки EmWood можно циклевать, шкурить, покрывать морилкой,
красить, лакировать, полировать теми же иструментами, материалами и способами,
что и изделия из цельной древесины», — отмечает Томо, говоря о финишировании
WPC-изделий.
Благодаря своим свойствам, WPC восприимчивы к пигментированию в самом
процессе производства, что часто оказывается достаточным, и изделия не
требуют дополнительной отделки. Но высокое содержание частиц и волокон
древесины (особенно, если их более 50%) в изделии позволяет покрывать
их морилкой или краской.
«В отличие от пластика, который нелегко окрашивать, WPC-детали можно придать
широкую цветовую гамму. Пигменты часто бывают недостаточно стойкими к
солнечному свету и со временем выгорают. Однако множество химических компаний
предлагают различные добавки, применение которых при окраске WPC как «в
массе», так и снаружи позволяет добиться нужной светостойкости и стабильности
цвета», — подчеркивает Куармли.
Последние разработки в области технологий финиширования WPC открывают
широчайшие перспективы. Мюррей, например, считает, что по применению WPC
в интерьерах и для мебели нынешние производители находятся лишь на вершине
айсберга.
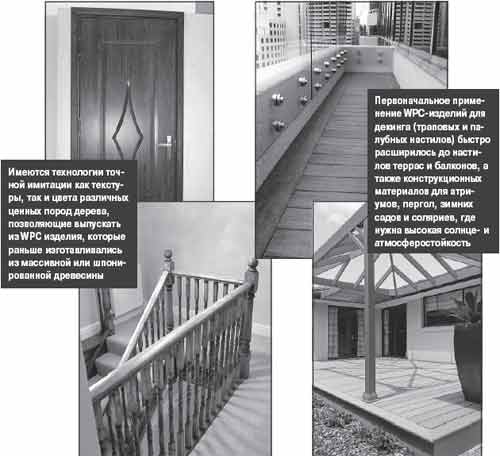
Спрос на WPC-погонаж прирастает не менее чем на 15%
в год
Увеличению спроса на WPC-изделия, безусловно, способствовали запретительные
меры в ЕС и США по ограничению и запрету использования химических пропиток
для защиты пиловочника для наружных отделочных изделий от влияния погоды,
насекомых и грибков.
По данным отчета Робина Маргулиса (Robyn Margulies), аналитика фирмы Freedonia,
прирост спроса в США на WPC-погонаж в 2005 году составил не менее 1,6%,
продажи достигли 5,1 млн. погонных футов, что превысило 10% от общего
спроса на погонаж в США. Несмотря на превалирование деревянных изделий
в этом сегменте, доля WPC-погонажа устойчиво увеличивается, постепенно
заменяя дерево, но особенно быстро — чистый пластик.
Помимо ограничительных мер и запретов на химически пропитанное дерево,
быстрый рост применения WPC-изделий объясняется и тем, что имеется уже
почти тридцатилетний положительный опыт по эксплуатации первых WPC-образцов.
Именно положительные результаты показали, что долговечность и стойкость
WPC-материалов выше деревянных, что они требуют лишь незначительного ремонта
после случайных механических повреждений, а способность к окрашиванию
позволяет «освежить» или изменить внешний вид и продолжить эксплуатацию.
Другая сторона медали — технологии утилизации WPC-изделий. Здесь наработаны
2 подхода — дробление и гранулирование WPC-отходов (например, при переделке
здания или после природных катастроф — торнадо, ураганов) и использование
их в составе асфальто-полимерной смеси для формирования стойкого поверхностного
слоя дорожного покрытия (опыт Германии), и подмешивание до 30% «вторичных»
WPC-гранул в смесь для производства неответственных с точки зрения внешнего
вида или окрашиваемых WPC-изделий (опыт США).
Однако основные отходы WPC-материалов формируются сейчас лишь случайным
образом, в основном за счет природных катаклизмов, когда имеются массовые
разрушения малоэтажного жилья. Т.е. пока не имеется устойчивой ресурсной
базы «вторичного» WPC-сырья и поиска других экономичных путей его переработки
соответственно. По большей части переработка WPC-отходов пока состоит
в сжигании вместе с другими отходами пластиков на обычных мусоросжигающих
заводах для когенерации тепло- и электроэнергии.
В поисках высокоприбыльных лесопользования и деревообработки
Очень показателен почти двадцатипятилетний опыт превращения древесных
отходов в деньги, имеющийся у калифорнийской компании Weaver Industries,
Inc., которая занимается обрезкой и расчисткой заповедников, коммерческих
лесонасаждений и обрезки деревьев на домашних участках. Ее президент Тим
Уивер (Tim Weaver) и его брат Рэнди (Randy Weaver) начали с основания
фирмы Weaver Tree Service, которая помимо оплаты за основную деятельность
занималась поставкой древесной щепы энергетическим компаниям. Бизнес процветал,
пока действовали правительственные субсидии, но в 1994 году они прекратились,
и фирма потеряла в течение года трех из четырех своих потребителей, потому
что энергетическим компаниям стало выгоднее использовать традиционное
энергетическое сырье, чем лесную щепу. Они предпочитали покупать древесные
отходы с лесопилен — чистые стружку и опилки, которые были дешевыми отходами
деревообрабатывающих предприятий — чем продукт компании — щепа с корой
и загрязнениями грунтом после работ по расчистке леза, вывоза, дробления
и сушки сучьев, веток и тонкомера.
Потеряв несколько миллионов долларов на энергетической щепе, компания
реинвестировала прошлую прибыль, перепрофилировала свою деятельность и
сменила название. Помимо диверсификации деятельности (компания начала
заниматься прививкой саженцев для садовых хозяйств, пересадкой целых деревьев,
рекультивацией земель до уровня «зеленая лужайка» или «молодой лес») в
компании был разработан целый ряд технологий производства новых продуктов,
получаемых переработкой древесной щепы. Компания закрыла ряд своих отделений
по рубке отходов древесины в щепу по всему штату, сконцентрировавшись
на двух производственных площадках во Фресно и Ливерморе в Центральной
Калифорнии. Было решено извлекать сверхприбыль, занимаясь производством
полезных продуктов из щепы и опилок, в основном для сельского хозяйства.
За $7500 фирмой был приобретен цилиндрический сортировочный грохот с размером
сита 20 и диаметром 2 м, на котором рассортировывалась щепа. Компания
стала сама закупать и вывозить щепу и опилки из лесопилен и у деревообработчиков,
предлагая собирать отходы производства в свою возвратную тару, доплачивая
фирмам за то, если щепа была чистая. Основу прибыли компании составляют
теперь такие продукты, как подстилка для скота, мульча, ленточные материалы
для посадки семян, наполнители «песочников» детских площадок, покрытия
арен ипподромов и для производства мебельных щитов из ДСП. Эти изделия
получают в результате сортировки разной щепы и смешивания ее с собственной
лесной щепой. Еще одно направление — перемалывание строительного мусора
из гипсокартона и гранулирование вместе с древесной щепой. Этот продукт
используется в сельском хозяйстве для нормализации щелочных и засоленных
земель.
Но не меньшую прибыль компания получает от производства таких изделий
тонкой переработки древесных волокон, опилок в древесную муку и пыль,
как наполнители шпатлевочных паст, грунтующих составов, массы для поизводства
бумаги и, главное, древесной основы для производства WPC-материалов.
Теперь фирма перерабатывает до 300?000 тонн различных видов щепы и опилок
в год на двух своих площадках и от 1500 до 2000 м3 деревной массы в неделю
на третьей, новой площадке в г. Верналис. «Продажей энергетической щепы
мы зарабатывали примерно $15 на тонне. Сейчас мы зарабатываем прибыли
на каждой тонне древесной массы в среднем впятеро больше. Хотя примерно
2,5% объема нашего производства по-прежнему занимает энергетическая щепа
и деревянные пеллеты для отопления в быту», — резюмирует Ренди Уивер.
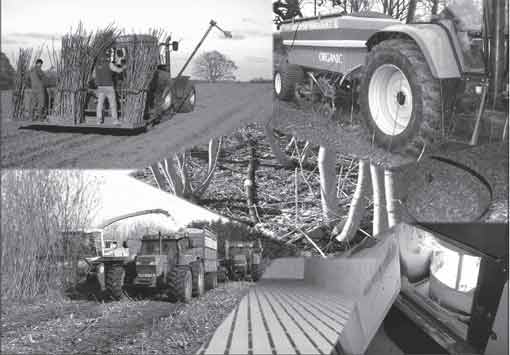
Еще один серьезный источник производства сырья для WPC — выращивание быстрорастущих лиственных кустарников на малопродуктивных землях. На фото виден весь цикл работ (против часовой стрелки): посадка семян, укладка хлыстов саженцев в борозду, машинная уборка тонкомера, производство WPC-изделий, сжигание неиспользованных отходов для получения энергии, использование зольных остатков для удобрения и мульчирования грунта.
Рука помощи
Одним из поставщиков высокочистой древесной пыли для калифорнийской компании
Weaver Industries, Inc. уже значительное время является фабрика Elk Grove,
Калифорния, одна их четырех, принадлежащих фирме Decore-ative Specialties
of Irwindale, Калифорния, занимающихся производством дорогих дверей для
офисов и деталей отделки апартаментов из цельного дерева.
Деревообрабатывающая фабрика Elk Grove оборудована мощной системой приточно-отточной
вентиляции, в состав которой входят четыре отточных вентилятора по 100
кВт и один приточный агрегат на 185 кВт. Система собирает от 40 до 60
м3 древесной пыли тонкой фракции в день.
Проблема состояла в том, что необходимо было снизить огромные затраты
на электроэнергию, используемую вентсистемой, и регулярную очистку самой
системы вентиляции. Причем производителям древесных отходов в Калифорнии
запрещено сжигать древесную пыль и твердые древесные отходы на собственных
энергетических установках, а необходимо продавать их производителям пеллет
или другим переработчикам древесных отходов.
Фирма Decore-ative Specialties решила эту проблему, с одной стороны, установкой
системы управления Ecogate, а с другой — лучшим способом утилизации самой
древесной пыли.
Джек Олбрайт (Jack Albright), вице-президент северного региона деятельности
Decore-ative Specialties, поясняет: «Для эффективного пылеудаления нам
необходимо откачивать 500 м3/мин воздуха через коллекторы пылеудалителей
на двух основных ветвях, расположенных в двух удаленных зданиях. Система
Ecogate не только закрывает неиспользуемые заслонки, но и регулирует поток
в главном канале вентиляционной шахты».
По словам Олбрайта, система Ecogate позволяет экономить 27% энергии на
пылеудаление в одном здании и 30% — в другом. На другой фабрике Decore-ative
Specialties стоят сразу два контроллера Ecogate, «входы которого подключены
буквально к каждому станку, благодаря чему мы экономим до 30% ресурса
станков, а наши счета за электроэнергию уменьшились на 13%-16%», уточняет
Олбрайт.
Второй «рукой помощи» оказалась компания Weaver Industries, Inc., которая
у Decore-ative Specialties отдельно выкупает и увозит тонкую древесную
пыль (для переработки в сырье для WPC) и древесную стружку, предварительно
перемолотую ею в щепу. Это покрывает еще порядка 30% общей стоимости электроэнергии
на пылеудаление.
«Еще один плюс кроме снижения себестоимости — у нас на предприятии не
остается лищней щепки или древесной пылинки, нам не нужны площади под
отвалы», — говорит Олбрайт, «…у нас все идет в дело, но при этом мы заняты
только своим бизнесом и не создаем подсобных хозяйств по переработке отходов».
WPC-материалы: основные Pro & Contra Сравнение свойств WPC и цельной древесины показывает, что недостатки WPC можно трактовать и как преимущества, в зависимости от поставленной задачи. Pro Contra Источник: Компания Atlas Precision, «На пороге новых рыночных возможностей», 2008 |
Заключение
Древесные отходы — сопровождающий деревообработку недостаток. Раньше были
два пути борьбы с ним — собирать (в отвалы) и удалять (сжигать). Теперь
открылся третий путь — использование. Как для производства прогрессивных
WPC-изделий, так и для выпуска других видов товарной продукции: от экологического
возобновляемого топлива до продуктов для рекультивации и повышения плодородия
земель, производства отделочных и утеплительных строительных материалов
и совершенно новых видов изделий.
По данным исследования, проведенного на базе Alpine Trucking and Specialty
Woods в г. Игар (Eagar), штат Аризона, разного рода деревообрабатывающие
производства переводят в стружку и опилки от 24% до 67%, а в среднем —
до половины (48%) объема обрабатываемой древесины. Понимание технологических
особенностей производства полезных продуктов переработки тонкомеров, технологических
дров, древесной щепы и опилок приводит к осознанию экологической и экономической
выгоды, которую можно получать уже сейчас, и которая увеличивается из
года в год, и станет единственным путем развития отрасли переработки древесины
в будущем.
С. Шовкопляс
По материалам конференций Агентства по использованию лесных ресурсов USDA
Forest Service и публикацям «Forest Products Journal» и «Wood & Wood
Products»,
США, 2002-2008 г.