![]() Рис. 1. Куб Apple Store, Нью-Йорк | Именно эти соображения — больше или меньше — побудили взяться за статью. Статья также иллюстрирует использование стекла в конструкционном (структурном остеклении) на примере ряда проектов, построенных в последние годы, а также использования стекла в качестве конструкционного материала для лестниц и ограждений. |
КОНЦЕПЦИЯ «БОЛЬШОЕ СТЕКЛО»
Концепция «Большого стекла» родилась в Нью-Йорке и, первоначально, именно для него. И новостройка Apple Store на 5-й авеню воспринимается сейчас как архитектурный символ города (рис. 1), так сказать, «Большое стекло» для «Большого Яблока»1.
1Примечание редакции. «Большое Яблоко» — иносказательное название г. Нью-Йорк, США
Конструкция стеклянной коробки состоит из ряда поддерживающих
колонн из 10-миллиметрового стекла, на которую опирается решетка из стеклянных
лежней, а на них — панели бокового остекления и крыши. Ребра также выполняют
несущую роль, ужесточая панели при изгибе от ветровой нагрузки.
Это тот случай,
когда рассчитывали, что ребра жесткости (подрядчик — Seele) будут работать совместно и
выступать заедино с листовыми панелями.
Ограничения по производству стекла на момент
строительства (2005–2006) были таковы, что тогда было трудно найти подходящее
стекло размером более 6 м в длину, и не было еще автоклавов, чтобы заламинировать
листы большей длины.
Концепция создания монолитных ребер жесткости со слоями
из стекла из панелей длиной 6 м напоминает ребра, сделанные из фанеры. Этот этап
процесса ламинации пяти стеклянных пластин (подобных по гибкости листам шпона) в
единое ребро должен был обеспечивать перекрытие не менее двух пластин (причем
безо всяких напряжений, изгиба или кручения по соединительному торцу между ними).
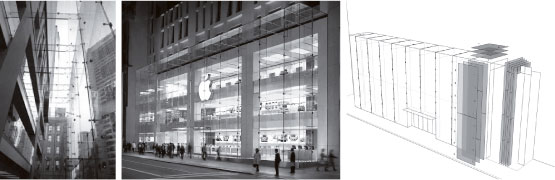
Рис. 2. Атриум здания Apple Store в Сиднее изнутри
Рис. 3. Атриум здания Apple Store в Сиднее снаружи
Рис. 4. Атриум Apple Sydney, скрепленный внакрой соединителями и заламинированный
Полная сборка этих наложенных друг на друга листов затем усиливалась
креплением болтов и постановкой упрочняющих элементов, которые препятствовали сколам —
таким путем формировалась монолитность.
Главная сложность состояла в том, что
нужно было создать как минимум специальный автоклав, чтобы заламинировать стекло,
но ни времени, ни возможности в стеклянной индустрии на это тогда не было. Не
смущаемые этим ограничением, в BGT (консультант и изготовитель стекла, Германия)
обнаружили, что в авиастроении применяется технология ламинирования длинных крыльев,
и их оборудование во многом подобно тому, что применяется для ламинирования стекла
толщиной от 10 мм.
После испытаний, специалисты из BGT дали добро, а потом
использовали авиационные автоклавы для производства ламинированных пакетов для
стеклянного куба.
Здание простояло уже несколько лет, и пока не видно каких-либо
отслоений и других дефектов ламинации стекла.
УНИКАЛЬНО БОЛЬШОЕ СТЕКЛО
Целый ряд проектов с применением больших стекол появился после
куба в Нью-Йорке, причем и для Apple, всякий раз демонстрируя конструкционные
возможности широкоформатного стекла на новом уровне, причем обходясь все меньшим
и меньшим числом соединителей.
Атриум здания Apple Store в Сиднее, Австралия,
перекрывает сбоку три этажа, крышу шириной 4,5 м и идет вдоль всех 20 м фасада
здания (рис. 2, рис. 3).
Здесь сначала развивалась идея использовать цельные
листы размером 13×3 м. Впоследствии для создания монолитного «мега-листа»
(рис. 4) пришли к перекрестной установке панелей из трех листов закаленного и
заламинированного стекла 8×3 м.
Характерно, что заполненные конструкционным
силиконом поперечные швы и промежутки между листами панелей визуально выглядели примерно
одинаково с креплением силиконом ребер жесткости, а с точки зрения прочности
применение соединителей панелей оказались, скорее, перестраховкой.
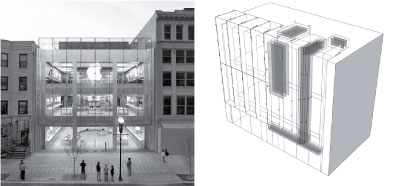
Рис. 5. Здание Apple Store в Бостоне, Массачусетс, США
Рис. 6. Фасад Apple Boston, скрепленный внакрой соединителями и заламинированный
Эти ребра высотой более 13 м выполняют существенную несущую
функцию и визуально формируют здание в единое целое. Подобно тому, как были соединены
внахлест пять панелей стекла высотой 8 м в Сиднее, здесь тоже листы стекла были обрезаны,
наложены друг на друга и заламинированы. (рис. 6). В результате получились ребра,
которые нельзя было перевозить в контейнере, поэтому потребовалась специальная
перевозка на открытой площадке.
В отличие от принципов конструирования, примененных
в нью-йоркском Кубе и в Сиднее, где было дополнительное механическое соединение
листов в панели через выполненные в листах отверстия, в Бостоне промежуточные
ламинирующие слои играли куда большую роль. Использование соединенных ламинацией
панелей из однослойного стекла в «клюшечном» ребре стало ключом к выравниванию
высоких напряжений вдоль «фалды» и в «колене». Эта передача сдвига между пластинами
минимизировала работу, которую должны были выполнять болтовые промежуточные
соединители, практически до нуля, позволив создать ребра, не замутняющие чистоту
линий граней и просвета непрерывного стекла.
Подрядчиком в этих проектах выступила
все та же Seele, в которой решились таки на постройку своего крупноформатного
оборудования. Они сделали у себя автоклав длиной 12 м, что, однако, недостаточно
для изготовления панелей и ребер для проекта, подобного Сиднейскому. Компания Sedak,
основанная Seele для производства стекла, оказалась расторопнее и вовремя заказала
автоклав длиной 15 м.
Помимо изготовления, для таких больших панелей возникают
еще две больших проблемы: доставка и монтаж. Ясно, что с такими панелями обращаются
со всей осторожностью и бережностью. Фирма Seele проинвестировала создание
специального оборудования для обращения с такими панелями — это поистине техническое
чудо. Транспортировка до Сиднея осуществлялась на открытой палубе сухогруза и
заняла 3 месяца.
ЛЕСТНИЦЫ
За последние пять лет автору пришлось поработать с Apple в области
конструирования и постройки стеклянных лестниц в их магазинах-представительствах
по всему миру.
Одной из разработок была самонесущая стеклянная винтовая лестница
для Apple Store на 5-й авеню в Нью-Йорке с использованием перекрещивающихся консолей,
причем центральная часть служила стеклянным лифтом. Лестница охватывала сразу два
этажа.
Другой проект был на 14-й улице Нью-Йорка, и этот проект сначала предназначался
для Бостона. В обоих проектах предполагалось соединить стеклянной лестницей непосредственно
три этажа в два оборота (см. рис. 7–9). В случае лестниц высотой более этажа
проектировщик должен быть уверен, что напряжения с верхних ступеней не влияют на
нижние, и наоборот. Это значит, что должна быть применена система консольных поддержек
к несущей центральной части. В конструкции были также предусмотрены пустотелые
стеклянные ступени и несущее ограждение на специальных самоустанавливающихся поворотных
опорах.
Нижний этаж был специально усилен, чтобы вынести повышенную сосредоточенную
нагрузку от полностью заполненной лестницы.
Основной принцип конструкции
многопролетной лестницы, которая передает вертикальную нагрузку на основание на
самом нижнем этаже, таков:
- вертикальная нагрузка на проступенек прилагается к стеклянной несущей центральной части и ограждению;
- ограждение опирается на стеклянные консольные балки из сдвоенных листов стекла (рис. 10);
- стеклянные консоли крепятся к центральной части и выступают за ее пределы.
- силы, раздвигающие центральную часть и действующие вверх и вниз, максимально уравновешены стяжкой на якорях, заделанных в перекрытия этажей.
Поперечная устойчивость лестниц обеспечивается непосредственной связью между опорным лежнем и промежуточными уровнями до верха благодаря соединителям из нержавеющей стали, скрепляющих элементы центральной части воедино. Эти соединители были спроектированы, чтобы передавать нагрузку строго вниз и компенсировать всевозможные боковые нагрузки и изгибные моменты на элементы центральной сборной колонны.
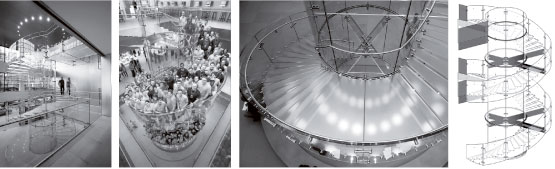
Рис. 7. Спиральная лестница на два этажа, 14-я улица, Нью-Йорк
Рис. 8. Спиральная лестница Apple, Бостон, на 3 этажа под нагрузкой
Рис. 9. Консоли-противовесы (рис. 10) выступают за пределы центральной несущей части, ограничивая лестничную площадку
Важным элементом расчетов и исследований был расчет и изучение
поведения подшипниковых узлов в местах контакта со стеклом, проведенный специалистами
Seele. Имея полную картину расчетов и экспериментов, мы все же ограничили несущую
нагрузку для всех элементов по сравнению с допустимой в строительных кодексах
(например, ASTM в США) для стекла примененных типов, чтобы увеличить запас прочности.
Позже мы убедились в правильности работы спроектированных подшипниковых
самоустанавливающихся опор в местах контакта со стеклом, поэтому теперь мы бы
увеличили допустимую несущую нагрузку для новых подобных конструкций.
При
проектировании подобных лестничных конструкций очень важно провести ее частотный
и модальный анализ и проверить резонансные свойства. Цель — обеспечить собственную
частоту колебаний всей системы выше 4 Гц, и не допустить резонанса как всей конструкции,
так и ее элементов в пределах нижних частот. Однако стекло в этом смысле — благоприятно
жесткий материал.
К ВОПРОСУ О РАЗМЕРАХ
Вопрос, а стоит ли производителям переходить на производство
стекол больших размеров, чем обычно, стоит обсудить дополнительно.
Все используемое
стекло поступает в виде кускового сырья, которое выпускается на флоат-линиях. То
есть первое ограничение исходит от производителей сырого стекла. Длина и ширина
этого стекла обычно ограничивается размерами около 6×3 м, некоторые выпускают
листы длиной до 8 м и очень редко — до 12 м. Эти большие размеры очень редко производятся,
не чаще двух раз в год. Они нетипичны по размерам и не пользуются устойчивым спросом.
К тому же обращаться с этим листовым стеклом очень трудно, и неизбежен частый бой.
Многие производители и перешли бы на выпуск 12-метрового стекла, если бы спрос
существенно увеличился, поскольку большинство из них на самом деле ограничены только
размерами своих стеклоподъемников.
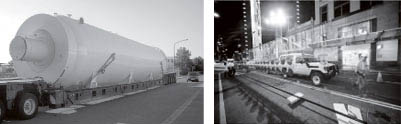
Рис. 11. Доставка автоклава длиной 15 м
Рис. 12. Подготовка к монтажу Jumbo-панели
Во-вторых, имеются ограничения при обработке стекла. Большинство
печей для термообработки и закалки стекла, установленных в последние годы, значительно
увеличились в размерах (до 80 м в Европе и до 14 м в Китае).
Ограничения по ширине
— в основном 2,7 м и очень редко зев печи пропускает стекло максимальной шириной 3 м.
Автоклавы тоже не растут по размерам, хотя автору известен, по меньшей мере, один
производитель, обрабатывающий панели с допустимым размером листов 15×3 м.
Перевалка и доставка — вот самый трудный участок по применению широкоформатного
стекла, становящийся пока самым главным ограничивающим фактором.
Обычно не
выпускают краны с размерами захватов, обеспечивающими перевалку листов размером
больше, чем под у закалочной печи. Доставка обычно ограничена размерами морского
контейнера, для которого 15 м — предел. Доставка на открытой палубе несет высокий
риск, но большую стоимость занимает риск боя при дальнейшем транспортировке и монтаже.
И, в конце концов, самый важный фактор — экономический.
В мире есть всего несколько
клиентов, которые не задрожали бы, услышав цену того, сколько на самом деле стоит
фасад из крупногабаритных стекол. При увеличении размеров сверх обычных на порядок
возрастают все стадии изготовления — и по времени, и по цене.
Аппетиты должны расти
медленно, чтобы у людей, инвестирующих подобные разработки, появился устойчивый интерес.
Тем более что вопросы о размерах сейчас менее актуальны, чем вопросы остекления
энергосберегающих и самообеспечивающихся зданий.
Применение же стекла обычных
размеров в качестве основного конструкционного материала в несущих конструкциях
(фасады, лестницы, мосты, этажные перекрытия, крыши) — вот настоящий Клондайк и
мегатренд на годы вперед и для строителей, и для производителей стекла.
Дипл. инж. Джеймс О’Калахэн (James O’Callaghan),
дипл. инж.
Марчин Марчевка (Marcin Marchewka).
По материалам доклада на Glass Performance Days,
июнь 2009 г., Тампере, Финляндия