Об этапах и технологических нюансах производственного процесса прибывшим на экскурсию менеджерам, торговым представителям или бизнес–партнерам (их компания Winbau тоже приглашает на экскурсии), рассказывает технический директор ДП «Интергласт» Glast GmbH — Лемешев Александр Викторович.
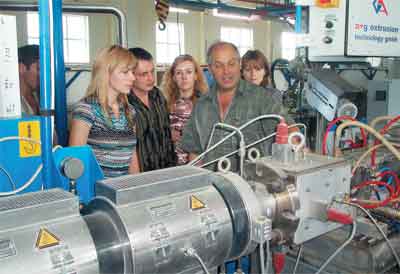
Лемешев А.В.: Последовательно ознакомившись со всеми этапами
производства, вы узнаете обо всех превращениях, которые претерпевает исходное
сырье, прежде чем превратиться в профиль, аккуратно уложенный в паллеты.
В производстве задействован инструмент для выпуска 17 видов профилей.
Этап приготовления смеси
Первый производственный этап — это святая святых, поскольку это этап приготовления
смеси. Для осуществления этой операции необходима четкая и отлаженная
работа нескольких участков производства.
Начинается все с разгрузки и хранения основного компонента для создания
пластикового профиля — суспензионного ПВХ. Все компоненты смеси, из которой
создается ПВХ-профиль Winbau, закупаются у западноевропейских производителей
— в Австрии, Германии, Венгрии, Франции, Бельгии. И хотя приобретаемое
нами сырье — это высококачественный продукт, абсолютно все оно подвергается
жесткому входному контролю. Каждый компонент проверяется на соответствие
технологическим свойствам. В частности, проверяются насыпной вес, влажность
и сыпучесть, то есть те парметры, которые непосредственно влияют на технологический
процесс производства. Например, повышенное содержание влаги в каком-либо
из компонентов влияет на внешний вид и физико-механические характеристики
готовой продукции. Поэтому в производственный цикл попадает только проверенное
лабораторией сырье, которое соответствует всем заданным требованиям, заложенным
в технологическом регламенте.
Затем суспензионный ПВХ с помощью специальных разгрузочных машин поступает
в емкости наружного хранения (3 алюминиевые башни вместимостью 60 тонн
каждая), которые расположены рядом с производственным цехом. В них происходит
накопление суспензионного ПВХ для его бесперебойной и равномерной подачи
на последующие участки подготовки смеси. ПВХ на весы подают по трубопроводу
пневмотранспортом.
Участок подготовки аддитивов
Параллельно в отдельную станцию загружают аддитивы — необходимые добавки
в ПВХ, которые дают возможность переработки поливинилхлоридной смолы на
экструдерах, а также обеспечивают белизну, глянец и физико-механическую
прочность будущего профиля. От качественного и количественного состава
аддитивов зависят характеристики будущего профиля.
Например, в качестве модификатора ударной прочности компания Winbau использует
хорошо себя зарекомендовавший продукт фирмы «Rohm and Haas». В качестве
пигмента используется продукт одного из ведущих производителей в этой
сфере — Kronos Europe S.A/N.V на основе TiO2 с оптимально подобранными
для переработки ПВХ оптическими и технологическими свойствами, показателями
атмосферостойкости и транспортабельности. Рутильный диоксид титана — это
важнейший белый пигмент, который применяют при экструзии ПВХ-профилей
белого цвета или светлых (пастельных) тонов, обладающий высокой термостойкостью.
Он играет роль одновременно пигмента и наполнителя, то есть обеспечивает
непрозрачность, светостойкость, повышение твердости, электрического сопротивления,
поглощает УФ-лучи в области 300-380 нм. Но важно учитывать, что эффективность
светозащитного действия рутильной формы двуокиси титана зависит от оптимальной
дозировки и качества его обработки.
Применение пигментов низкого качества или в неправильной концентрации
чревато ухудшением со временем внешнего вида ПВХ-окон (дисколорация, пожелтение
и пр.). Для достаточной защиты полимера пигменты необходимо добавлять
в количестве не менее 3,5-5 частей на 100 частей ПВХ. ДП «Интергласт»
Glast GmbH строго соблюдает рекомендации по его использованию. Другие
составляющие, которые использует Winbau для создания компаунда, также
высокого качества и только от западноевропейских производителей (BorsodChem
Rt, Chemson, Omya и др.).
Емкости внутреннего хранения. Здесь происходит окончательная гомогенизация
готовой смеси. Смесь выдерживается не менее 24 часов.
Участок подготовки аддитивов — это целый комплекс устройств, включающий
в себя разгрузочное устройство, емкости для хранения компонентов, дозаторы
и весы, которые служат для подготовки композиционных добавок, придающих
ПВХ-профилю необходимые свойства.
Дисплей, на котором выставляются режимы и параметры на экструзионную машину.
Экструзионная линия
Покомпонентное смешивание ингредиентов
Далее происходит покомпонентное смешивание ингредиентов через систему
подготовки смеси. Здесь установлена компьютерная программа. Благодаря
полной автоматизации процесса для обслуживания участка достаточно 2-х
человек. На электронных весах взвешиваются малые добавки, и отмеренная
порция подается в смеситель. Туда же подается поливинилхлоридная смола.
Ее точно взвешенная порция перемешивается в течение определенного времени
в горячем смесителе. В процессе смешивания компоненты разогреваются до
120°С и происходит гомогенизация смеси.
В процессе приготовления композиции оператор участка смешивания контролирует
множество технологических параметров, а также температурный и временной
режимы. Все параметры наглядно отображаются на экранах компьютерных мониторов.
Таким образом осуществляется постоянный автоматический контроль процессов
смешивания.
Затем композиция из горячего смесителя передается в холодный смеситель,
где при перемешивании и принудительном охлаждении масса должна остыть
до 40°С.
Из холодного смесителя остывшая смесь по автоматической системе пневмотранспортных
магистралей подается в следующий цех — в емкости внутреннего хранения,
где происходит дозревание смеси.
Процесс экструзии
Готовая композиция по запросу экструдера равномерно подается на линию
в загрузочный бункер, и начинается процесс экструзии.
На одной экструзионной линии происходят все этапы: от поступления смеси
в экструдер до упаковки профиля в паллеты. Линия состоит из экструдера
с фильерой, сухого калибратора, калибровочного стола с водяным охлаждением
и вакуумным насосом, маркировочного устройства, приемных тянущих валков,
приспособления для нанесения защитной пленки, пилы, опрокидывающего лотка
и устройства для упаковки готовой продукции. Весь процесс полностью автоматизирован.
В производстве ПВХ-профиля торговой марки Winbau используют одно- и двухлучевые
экструзионные линии.
Двухлучевая машина перерабатывает в смену (за 12 часов) 6 тонн смеси (10
кубов). В целом производственные мощности завода составляют 900 тонн в
месяц. Кроме того, осенью введут новое оборудование, которое позволит
еще больше увеличить мощности.
Дозатором смесь посредством шнеков подается в рабочий цилиндр экструдера,
имеющий отдельный электропривод.
Шнеки — это главный узел всей профильной экструзионной линии. Они забирают
сыпучий ПВХ-компаунд от загрузочного отверстия, продвигая материал от
одной зоны цилиндра к другой, способствуют достижению состояния пластификации
смеси и равномерно подают ее в виде гомогенного расплава к фильере. Продвигаясь
по каналу шнеков, материал разогревается до температуры 160°С (температура
фильеры 200°С) посредством внутреннего вязкого трения и тепла, подводимого
от электронагревателей, расположенных на корпусе рабочего цилиндра. Масса
нагревается в трех зонах:
1) зона питания (загрузки) — участок, на котором перерабатываемый
материал находится в твердом состоянии;
2) зона сжатия (плавления) — участок, на котором почти полностью
происходит плавление материала;
3) зона дозирования — участок, на котором материал находится в
расплавленном вязкотекучем состоянии.
Для отвода избыточного тепла и для соблюдения нужного температурного режима
служит система воздушного охлаждения, состоящая из вентиляторов, системы
воздухопроводов и заслонок.
Смесь продавливается (экструдируется) через фильеру, которая и задает
геометрию будущего профиля.
Важные моменты, которые необходимо учитывать при экструзии ПВХ-профилей Хотя принцип создания пластикового профиля и кажется простым, все
стадии экструзии и связанные с ними установки должны быть тщательно
скоординированы, чтобы обеспечить получение качественного материала.
Очень важно, например, правильно выдерживать режимы разогрева и
охлаждения, поскольку возможно искажение формы профиля уже в ходе
экструзии из-за неравномерного температурного режима. |
Участок калибровки и охлаждения
Из фильеры расплав попадает в вакуумный калибратор, где при помощи вакуумной
формовки и охлажденной воды в калибраторе происходит первоначальное охлаждение
профиля. Так профилю придается окончательная форма.
Затем профиль нужно зафиксировать (остудить), и он поступает на участок
вторичного охлаждения, где на него подается холодная вода. Происходит
это в водяной ванне. Профиль охлаждается по всей поверхности в циркулирующей
воде в прозрачном резервуаре.
На замкнутой системе оборотного водоснабжения следует остановиться подробнее.
С участка экструзии вода поступает в теплый бассейн, потом подается в
холодильник, охлаждается и сбрасывается в холодный бассейн. При этом вода
проходит через системы очистки и умягчения. Из этого бака вода при помощи
насосов подается на смесители и экструзионные линии для охлаждения профиля.
Все происходит автоматически. Система позволяет не только непрерывно работать
на охлаждение всех экструзионных линий, но и использовать тепло воды для
обогрева производственных помещений завода.
Производство штапика
Аналогичным образом производится штапик, на точно таком же экструдере
с программным обеспечением и температурными режимами. Для получения уплотнителя
профиль с помощью фенов вновь разогревается, и расплав эластичной композиции
уплотнителя, выходящий из фильеры ко-экструдера, присоединяется к нему,
а затем происходит дальнейшее охлаждение профиля сложного сечения.
Участок маркировки и распила
С участка вторичного охлаждения профиль равномерно вытягивается и подается
для маркировки. Специальным устройством на профиль наносится дата изготовления,
информация о том, какая смена и бригада принимала участие в изготовлении,
обозначение системы профиля. Затем на профиль наклеивается защитная пленка.
Последний штрих в процессе изготовления профиля — в конце линии установлена
пила, отрезающая профиль необходимого размера (по 6 м). Срабатывает концевой
выключатель, и пила выполняет цикл отрезания. Распиленный профиль укладывают
в паллеты, проводят необходимые испытания, на основании которых заполняется
паспорт с присвоением номера партии.
С каждой паллеты нарезаются образцы для испытаний. Запакованные паллеты
с профилем отправляют на склад готовых изделий. Так создается профиль.
В целом в производстве задействован инструмент для выпуска 17 видов профилей.
Таковы основные этапы производства. Теперь задавайте вопросы.
Двухлучевой экструдер. Экструдер состоит из рабочего цилиндра и шнеков,
привода, загрузочного устройства, системы смазки и охлаждения, системы
нагрева рабочего цилиндра, системы дегазации рабочего цилиндра, электросилового
шкафа, системы защиты от перегрузок и системы автоматического контроля
технологического процесса.
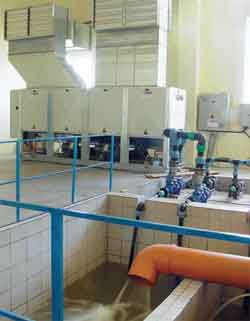
Водоснабжение
Нанесение защитной пленки
На фотографии зафиксирован момент комплектации штапика. Инструментом подается
расплав эластичной композиции уплотнителя, и в следующее мгновение выходит
укомплектованный штапик. Для создания уплотнителя компания Winbau использует
немецкую композицию Rottolin-Werk, созданную на основе PVC/NBR.
Экскурсанты: Вы говорите о полной автоматизации процесса. Можете конкретизировать?
Лемешев А.В.: Да, конечно. Мы используем новейшие системы контроля процесса производства ПВХ-профилей, улучшающие производительность оборудования и качество продукции. В частности, используем оборудование фирмы «Krauss-Maffei», которая усовершенствовала систему своих микропроцессоров, установленных на экструзионных линиях. Кроме увеличения скорости обработки данных, в производственную линию включен высокоскоростной модем, через который все характеристики процесса экструзии поступают на главный сервер и могут отслеживаться как оператором, так и автоматически. При этом допущенные ошибки анализируются, и исполнительным механизмам выдаются команды для их устранения. Таким образом, система «человек-машина», отслеживая главные параметры работы линии (вращающий момент шнеков, температура и давление расплава ПВХ по зонам, тянущее усилие вытяжных устройств и т.д.), позволяет эффективно вести процессы экструдирования одновременно на нескольких линиях и своевременно устранять возникающие неполадки и сбои.
Экскурсанты: Используете ли вы вторично технологические отходы?
Лемешев А.В.: Вторично для сырья мы ничего не используем. Технологические отходы после запуска экструзионных линий, образцы профиля после испытаний, обрезки профиля, поступающие со сборочных производств, и прочие отходы экструзии направляются в дробильное отделение. Здесь установлена современная высокопроизводительная дробильная установка фирмы Herbold Meckesheim GmbH. Передробленные отходы мы отдаем клиентам, которые делают вагонку. В производстве оконного профиля мы используем только первичное, качественное сырье.
Экскурсанты: В чем отличие профилей разных торговых марок?
Лемешев А.В.: Приведу такой простой пример. Можно добавлять в смесь мел 65 ТК, можно другой. Мы используем мел 95 ТК. Понятно, что различие заключается, как минимум, в качестве мела. В обеспечении технических характеристик ПВХ-профиля существенную роль играет и дисперсность мела: карбонат кальция с поверхностной обработкой, придающей ему гидрофобные свойства, имеющий величину частиц менее 2 мкм и белизну 95%, способствует длительному сохранению ударной вязкости и начального цвета жесткого ПВХ. Компания Winbau в рецептуре использует мелкодисперсный мел в строго заданных количествах, что обеспечивает оптимальный эффект. В целом, многое зависит от качества сырья, его происхождения и используемого количества согласно рецептуре.
Экскурсанты: У одного из наших производителей возникла такая проблема — у него при сварке профиля теряется 5 мм, и на местах сварки образуется желтизна (поджаривается профиль). Температуру он перестроить не может, так как если поставит ее ниже — не сможет сваривать другой профиль. Как вы можете это прокомментировать?
Лемешев А.В.: Желтые пятна — признак перегрева. Необходимо сократить
время расплава и время выдержки — до 20-30 секунд на расплав и 20-30 секунд
на охлаждение (склеивание). Давление воздуха на прижиме должно быть 6,
на сжатии
4 бара. За этим тоже нужно следить. У нас, например, был такой случай.
К нам пришел производитель с претензией, что профиль не сваривается. Я
лично поехал к ним на производство, сам сделал сварной шов, вернулся в
нашу лабораторию и отдал на испытания. По результатам мы получили прочность
сварного шва в 2 раза больше, чем был у переработчика, который пришел
с претензией. То есть, если возникает проблема со сваркой профиля, это
говорит не о том, что плохой профиль или плохо работает сварочное оборудование,
а о том, что его нужно правильно настроить на профиль. В филиалах нашей
компании есть технологи, которые обладают необходимыми знаниями и опытом
и выезжают при необходимости к партнерам на производство. Все нужно настраивать
индивидуально. Если, например, температура помещений ниже 18°С, то нужны
уже совсем другие параметры сварки.
Экскурсанты: Теряет ли профиль свои качества при изготовлении арок?
Лемешев А.В.: Не теряет. Для того чтобы сделать арку нужно полностью
заполнить все камеры. Есть два способа изготовления арок: сухая гибка
(инфракрасным облучением) и мокрая гибка (глицерином). Когда профиль согнули,
он охлаждается и сохраняет принятую форму, при этом полностью сохраняются
все его свойства. Мы проводили испытания профиля у себя на заводе и установили
оптимальную для профиля Winbau температуру гибки — 125-130°С и время размягчения
— 25-35 минут. На практике профиль Winbau можно радиусно изогнуть вплоть
до 250°, что подтвердили проведенные нами эксперименты.
В завершение хотелось бы отметить, что наращивание производственных мощностей
продолжается, соответственно, объем выпуска продукции и ассортимент будут
расти.