Коврово-мозаичные плитки
Коврово-мозаичные плитки (белые или цветные тушеные), размером 21 x 21...45
x 45 мм, толщиной 4-5 мм выпускают штучными и в виде ковриков, наклеенных
на бумагу. Они предназначены для наружной и внутренней облицовки стен
зданий. Плитки изготовляют способом непрерывного проката.
Составы стекол. Плитки изготовляют из непрозрачных глушеных стекол.
В качестве глушителей служат соединения фтора (применение сокращается),
фосфора, мелкодисперсный глинозем (табл. 1).
В качестве сырья для введения фосфатов используют двойной суперфосфат
или апатитовый концентрат. Применение мелкодисперсного глинозема позволяет
использовать в качестве основного сырьевого компонента (98-100%) бесцветный
бой строительного и технического стекла. Глинозем — тугоплавкий материал
(температура плавления свыше 2000°С), слабо растворяется в стекломассе.
Белый цвет глинозема не препятствует окрашиванию стекла в различные цвета.
Глушение глиноземом осуществляется в специальных каналах питателей.
Стекловаренные печи. Для производства мозаичной плитки используют
в основном ванные стекловаренные печи прямого нагрева производительностью
6-30 т/сутки в зависимости от числа установленных на печи линий. В зависимости
от состава стекла максимальные температуры варки — от 1370-1400°С (фторсодержащие
составы) до 1560-1580°С (фосфатные составы). В огнеупорной кладке бассейнов
для варки малощелочных глушеных стекол применяют кварцевые брусья.
В зависимости от способа проката (горизонтальный или вертикальный) к выработочной
части печи примыкает или сливной лоток, или струйный питатель. Для производства
цветной мозаичной плитки краситель вводят в состав шихты или используют
для этой цели непрерывное окрашивание в специальном питателе.
![]() Мозаичный пол из плиточного марблита |
![]() Панно из марблита |
Формование плиток осуществляется способом непрерывного проката
на механизированных линиях или способом прессования.
В зависимости от применяемого состава стекла и конструкции прокатной машины
различают два способа подачи стекломассы: с лотка и струйный. Первый способ
применяется при использовании горизонтальной прокатной машины. При этом
стекломасса должна иметь слабую склонность к кристаллизации в интервале
выработки. Второй способ позволяет формовать практически любые составы
глушеных стекол, в том числе с большой склонностью к кристаллизации. Основным
отличием прокатных машин (горизонтальной и вертикальной) является взаимное
расположение первой пары приемных валков с гладкими поверхностями по отношению
к валкам с рифленой поверхностью.
Формование коврово-мозаичной плитки производится в следующей последовательности:
Толщина остаточного стекла, не позволяющая на этом этапе рассыпаться ленте на отдельные плитки —0,5-0,6 мм. Остаточный слой стекла предохраняет режущие выступы рифленых валков от быстрого изнашивания. Самопроизвольное разламывание ленты с нанесенными прорезями производится в конце приемного стола прокатной машины. Ударяясь в лоток, куски ленты рассыпаются на отдельные плитки и по наклонному желобу ссыпаются на движущуюся сетку лера отжига, где медленно охлаждаются.
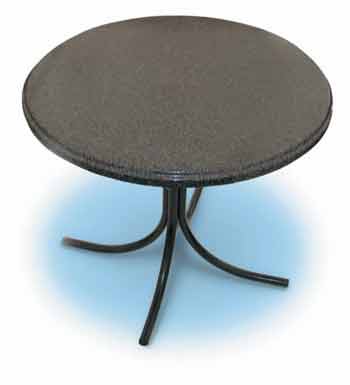
Столешница из марблита
Охлажденную плитку сортируют с помощью механических устройств с перфорированными
решетками (барабанов, вибросит). При этом кондиционные изделия отделяют
от битых. Осуществляется также визуальный контроль по показателям внешнего
вида. Отобранная плитка поступает в приемный бункер машины для механизированного
набора ковров.
Способом прессования по керамической технологии плитку изготовляют в
такой последовательности: бесцветный стеклобой измельчается на вибромельнице
до фракции 100-200 мкм и менее. В зависимости от требуемого цвета в
стеклопорошок вводят пигменты и для лучшего прессования в качестве связки
до 5% парафина. Из полученной пресс-массы на гидравлическом или рычажном
прессе прессуют заготовки требуемого размера, которые устанавливают
на керамическую подложку и подают в печь на термообработку.
В зависимости от зернового состава стеклопорошка и давления при прессовании,
максимальная температура спекания — 750-800°С (используют туннельные,
роликовые печи). Полученные таким путем коврово-мозаичные плитки имеют
огненно-полированную поверхность, четкие грани, равномерную окраску.
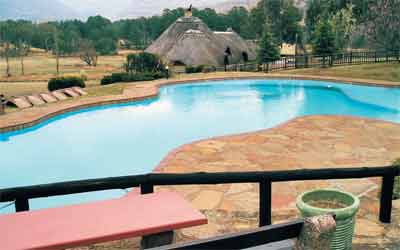
Бассейн с чашей, отделанный марблитовой крошкой на эпоксидном связующем
Изделия из стекломрамора
Стекломрамор — глушеное стекло в виде плит различного размера, однотонное
или с мраморовидным рисунком — получают способами проката. Предназначен
для декоративно-защитной облицовки стен зданий, покрытий полов, антикоррозионной
защиты строительных конструкций, футеровки резервуаров. Цвет изделий
— белый, бежевый, коричневый, зеленый, голубой, синий или белый с мраморовидным
рисунком. Лицевая поверхность кованая, обратная — рифленая.
Составы стекол. В производстве стекломрамора применяют малощелочные
высококальциевые стекла (табл. 2), глушение которых осуществляется за
счет фазового разделения расплава — ликвации.
Глушение стекол происходит за счет выделения огромного количества капель
размером 0,2-0,5 мкм, содержащих высококремнеземистую фазу. Регулируя
введение А12О3 и Na2О, получают стекла разной степени глушения.
Стекловарение и стекловаренные печи. Печи для варки малощелочных ликвирующих стекол должны обеспечивать температуру варки 1580-1600°С. Особенность варки высококальциевого состава — медленный провар шихты в области низких температур (до 1100°С) и высокая скорость варки в интервале температур 1400-1600°С. Это связано с аномальным поведением оксида кальция, который в области низких температур повышает вязкость расплава, а с ростом температур значительно ее понижает. Для варки используют регенеративные ванные печи с поперечным или подковообразным направлением пламени. Для кладки бассейна печи можно использовать брусья из плавленого кварца.
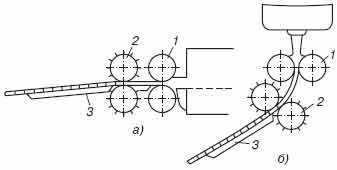
Рис. 1. Способы подачи стекломассы на прокатную машину:
а) с лотка;
б) струйный;
1 — гладкая пара валов,
2 — рифленая пара валов,
3 — приемный стол.
Формование. К ванной печи примыкает питатель со струйной подачей
стекломассы длиной 2-2,5 м, шириной 250-300 мм, глубиной слоя стекломассы
100-150 мм, Стекломасса сливается через обогреваемую платиновую трубку,
регулирующую подачу стекломассы. Формование облицовочных изделий из
стекломрамора осуществляется способом проката. Особенностью формования
изделий из ликвирующих составов стекол является их малая вязкость и
узкий температурный интервал выработки. Для выработки этих стекол применяют
струйный питатель и прокатную двухвалковую машину (рис. 1 а).
Ленту стекла формуют из расплава температурой 1400-1420°С. При необходимости
получения на поверхности плит мраморовидных узоров в питатель через
дозатор подается краситель. Лента стекла из прокатной машины поступает
в роликовую печь для отжига. Ликвирующий состав стекла имеет повышенную
температуру стеклования (до 700°С), что требует проведения отжига при
повышенных температурах (до 800-850°С).
Стекломрамор, полученный с помощью двухвалковой прокатной машины, имеет
кованую верхнюю и рифленую нижнюю поверхности. После отжига ленту стекломрамора
разрезают на листы требуемых размеров.
Для изготовления плит стекломрамора размером 140 і 250 мм с огненно-полированной
поверхностью применяют способ одновалкового проката. Сущность способа
— в свободном растекании расплава стекла под действием сил тяжести и
поверхностного натяжения до определенной толщины на одновалковой роторной
прокатной машине без верхнего формующего вала. Машина представляет собой
автомат непрерывного действия. Основной элемент ее — ротор диаметром
1400 мм. К нему по всей окружности приварено два ограничительных борта,
определяющих ширину вырабатываемых плит. Длина плит ограничивается выступами,
расположенными по ширине ротора между бортами.
Принцип работы машины состоит в следующем: на вращающийся с частотой
0,33-1,0 мин–1 ротор подается струя стекломассы с температурой 1420±10°С.
Свободно растекаясь по поверхности ротора между бортами до определенной
толщины, стекломасса образует непрерывную ленту. Резка ленты в пластичном
состоянии осуществляется металлическим ножом, движущимся возвратно-поступательно
перпендикулярно ленте стекла. Окончательное разделение ленты стекла
на плиты осуществляется с помощью механизма отломки, расположенного
в конце передаточного конвейера. Плиты поступают в лер отжига, после
чего подвергаются контролю качества и упаковке.
Облицовочные изделия на основе окрашенного листового
стекла
Марблит — листовое окрашенное стекло, преимущественно тушеное.
Производится в виде панелей различного размера путем периодического
проката. Лицевая сторона панелей может быть гладкой, узорчатой, шероховатой.
Обратная сторона имеет мелкую продольную нарезку или рифление для закрепления
листа при облицовке. Марблиты изготовляют самых разнообразных цветов:
молочные, черные, серые, кремовые, зеленые, розовые, мраморовидные и
др. К числу высокопроизводительных и перспективных способов изготовления
марблита следует отнести непрерывные способы проката и формования на
расплаве металла.
Стемалит — листовое стекло, декорированное с одной стороны легкоплавкими
силикатными красками разнообразной расцветки. Панели на основе стемалита
широко применяют в современном строительстве как эффективные элементы
наружной и внутренней облицовки разнообразных объектов строительства.
На рис. 2 показана многослойная строительная панель с использованием
стемалита.
Производится закаленный и отожженный стемалит. Закаленный стемалит по
сравнению с отожженным обладает более высокой (в 2 раза) прочностью,
но разрушается при механической обработке. Отожженный стемалит, уступая
по прочности закаленному, хорошо подвергается механической обработке.
Технология изготовления закаленного стемалита сводится к следующему.
Листы стекла с обработанными краями для очистки их поверхности промывают
слабым раствором соляной кислоты или других реагентов и направляют в
моечную машину, в которой используют обезжиривающие реагенты. Далее
одну сторону листа покрывают слоем силикатной краски с помощью краскораспылителей
или специальных приспособлений (по технологии трафаретной печати). Стекло
окрашивают на специальной непрерывно действующей конвейерной установке,
сблокированной с туннельной сушилкой непрерывного действия.
Листы стекла с высушенным слоем краски подвешивают зажимами к подвижной
раме транспортирующей тележки и передают в нагревательные вертикальные
печи щелевого типа, обычно применяемые в производстве автомобильного
закаленного стекла. В этих печах стекло нагревается до температуры закалки
(620-650°С) в течение 3-4 мин, одновременно происходит закрепление расплавляющейся
краски на поверхности листа. Разогретые листы стекла на выходе из печей
обдувают в специальных обдувочных решетках воздухом, поступающим от
вентилятора, в результате чего осуществляется закалка, а следовательно,
существенное упрочнение листов стемалита.
Технология изготовления отожженного стемалита отличается от закаленного
тем, что после сушки керамической краски листы стекла в горизонтальном
положении поступают на сетку непрерывно действующего агрегата, где происходит
обжиг краски и отжиг стекла.
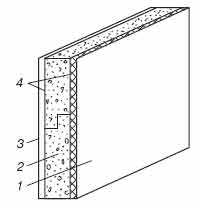
Рис. 2. Многослойная панель с использованием стемалита:
1 — стемалит (красочное покрытие с внутренней стороны); 2 — пеностекло
или стекловолокнистые плиты; 3 — отделочный материал (сухая штукатурка
и т.п.); 4 — клеевые соединения.
Ситаллы
Очень популярным отделочным материалом являются ситаллы. Ситаллом называют
искусственный поликристаллический материал, полученный кристаллизацией
стекла соответствующего химического состава и обладающий лучшими по
сравнению с этим стеклом некоторыми физико-химическими свойствами. Ситаллы
состоят из множества более или менее мелких кристаллов, связанных между
собой межкристаллической стекловидной прослойкой.
Для превращения стекла в ситалл необходимы два условия: во-первых, стекло
должно иметь нужный химический состав и, во-вторых, процесс кристаллизации
такого стекла должен осуществляться по особому режиму. Первое условие
обеспечивает образование таких кристаллических фаз, которые определяют
свойства ситалла. Второе условие относится, в основном, к режиму термической
обработки исходного стекла при его превращении в ситалл. Термическая
обработка позволяет образовать в стекле зародыши кристаллизации и обеспечить
их превращение в микрокристаллы с переходом стекла в более или менее
закристаллизованное состояние.
Ситаллы состоят из кристаллической и остаточной стекловидной фаз. Размер
кристаллов, как правило, менее 1 мкм, а их концентрация может меняться
в значительных пределах (20-90% по объему).
Ситаллы, как правило, получают из расплавов, застывающих в стекловидной
форме и способных при повторном нагревании выделять определенные кристаллические
фазы. В некоторых случаях ситаллы получают и с помощью порошкового способа,
сходного с применяемым в керамике. Однако при получении ситаллов при
меняют не кристаллические, а стекловидные порошки, которые при нагревании
кристаллизуются и спекаются в монолитный материал полукристаллического
строения, следовательно, технология ситаллов непосредственно связана
с технологией стекла.
Катализированная кристаллизация. Для реализации процесса превращения
стекла в ситалл нужно сначала выбрать химический состав стекла, образовать
в нем центры кристаллизации, а затем на этих центрах вырастить кристаллы
большего или меньшего размера.
Центры кристаллизации могут возникать самопроизвольно или появляться
в результате внесения посторонних частиц извне. Первый механизм получил
название гомогенного, второй — гетерогенного зародышеобразования.
При массовой объемной кристаллизации стекол важную роль играют вещества,
существенно ускоряющие скорость процесса — катализаторы кристаллизации.
Механизм образования центров кристаллизации в зависимости от состава
стекла и типа катализатора может быть различным — за счет образования
зародышей кристаллов (микрокристаллических частиц размерами менее 100
А) и т.н. микроликвационный механизм (образование капель размером не
более 100 А по всему объему стекла).
Ситаллы выпускаются в основном в виде плиточного материала разных размеров
и окраски. Их выкладывают по такой же технологии, что и керамическую
плитку, однако, ситалловая плитка — не намокает.
Интерес к облицовочным изделиям из стекла для строительства, отделки интерьеров и производства мебели в мире увеличивается, поскольку это соответствует современным тенденциям в архитектуре, технологии строительства и дизайне (см. “Окна. Двери. Витражи” №1-2007, стр. 84-88).
Технология стекла и стеклоизделий — Владимир, Транзит-Икс, 2003.