Первым рассматриваемым компонентом является «чистое» сопротивление разрушению
поверхности стекла, которое связано с трещиностойкостью материала и с
параметрами поверхностных микротрещин, вызванных воздействием механической
обработки и влиянием агрегатов закалочной печи и режимами упрочнения.
Вторым компонентом является остаточное напряжение сжатия, созданные в
ходе процесса закалки.
Обсуждаются результаты комплексного исследования конструкционной прочности
пластин и образцов из отожженного и упрочненного стекла. С использованием
специальной методики фрактографии выполнена оценка фактических форм и
размеров исходных микротрещин в фокусе разрушения закаленных стеклянных
элементов, а также на основе линейной механики разрушения рассчитан уровень
«чистого» сопротивления поверхности стекла хрупкому разрушению. Были также
оценены расчетом локальные закалочные напряжения возле выявленного при
испытании «слабого звена» на поверхности закаленного стекла.
Было установлено, что дефектность поверхности упрочненного стекла возрастает
при термической обработке стеклянного элемента, и в результате этого «чистое»
сопротивление стекла снижается по сравнению с прочностью исходного стекла.
Полученные данные о закалочных напряжениях характеризовались меньшей степенью
однородности по сравнению с результатами измерения напряжений оптическим
методом.
Предисловие
Прочность стекла является основой несущей способности и надежности новейших
конструкций архитектурного стекла. Ряд важных результатов по конструкционной
прочности стекла был получен за последние годы [1–4]. Было показано, в
частности, что глубина и геометрические параметры поверхностных микротрещин
имеют значительное влияние на прочность элементов из стекла, а также на
поведение при разрушении деталей при механическом нагружении [1, 2]. Состояние
трещиноватого поверхностного слоя зависит от качества производства базового
стекла и от совершенства обработки стекла в дальнейшем. Поэтому прочность,
в свою очередь, является эффективным параметром для контроля качества
стеклянных элементов.
Прочное ламинированное стекло и другие несущие композитные структуры из
стекла, состоящие из термически упрочненных стеклоэлементов, имеют широкую
сферу применения в современной архитектуре [3]. Но оценка их фактической
прочности на изгиб и надежности характеризуется большой степенью неопределенности,
несмотря на существование специальных строительных норм [1–4]. В отличие
от отожженного стекла, некоторые дополнительные факторы оказывают значительное
влияние на механическое поведение термоупрочненных (HS-стекло) и полностью
закаленных (FT-стекло) стеклянных элементов. Две главные составляющие
определяют уровень прочности термически упрочненного стекла qts, как это
может быть проиллюстрировано уравнением:
qts = qfs + qrs (1)
Первая составляющая qfs — это сопротивление разрушению поверхности или
«чистая» прочность поверхности стекла, связанная с состоянием поверхностных
микротрещин и типом напряжений, вызванных внешними силами. Обычно полагают,
что сопротивление разрушению поверхности стекла равно исходной прочности
отожженного стекла [1, 4]. Но фактические данные о сопротивлении хрупкому
разрушению поверхности закаленного стекла, подкрепленные измерениями для
понимания влияния агрегатов печи и режимов обработки изделий, отсутствуют.
Остаточные напряжения сжатия qrs, обусловленные процессом закалки, это
вторая составляющая прочности упрочненного стекла. Истинный уровень поверхностных
сжимающих напряжений, расположенных вокруг конкретного источника разрушения,
неизвестен. Но он должен быть точно определен для оценки прочности элемента
из упрочненного стекла. Стандартные оптические измерения, выполненные
в соответствии с пунктом B.1.2. стандарта EN 12150-2:2004, не дают ответа
на этот вопрос. В целом соответствующее изменение дефектности поверхности
стекла, а также фактические параметры остаточных поверхностных напряжений
сжатия и их реальное влияние, имеющее место при термической обработке
конструкционных элементов, изучены недостаточно. Поэтому определение прочности
упрочненных стеклоэлементов с учетом фактического вклада обоих указанных
этих компонент — ?fs и ?rs — является сейчас сложной актуальной проблемой
закалки стекла и проектирования строительных конструкций.
Качество технологии закалки стекла играет ведущую роль в решении этой
проблемы. Последние уточненные экспериментальные результаты показали,
в частности, что параметры статистического распределения прочности на
изгиб пластин из HS- и FT-стекла могут по разному зависеть от качества
механической обработки края и закалки под влиянием остаточных напряжений
и различных условий нагружения [3]. Вот почему оптимизация технологии
закалки стекла с использованием экспериментальных данных о параметрах
прочности и разрушения стеклоизделий могут быть важным инструментом для
гарантирования надежности несущих архитектурных конструкций из стекла.
Целью исследования была оценка реального влияния поверхностной дефектности,
сопротивления стекла хрупкому разрушению и остаточных напряжений на несущую
способность термоупрочненных и полностью закаленных стеклянных пластин
при изгибе. Важной задачей было показать, что вся технология закалки стекла
целиком определяет основные составляющие прочности упрочненного стекла.
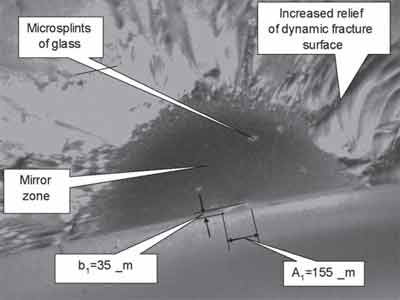
Рис. 1. Микрофрактографический анализ предельных параметров микротрещины на поверхности разрушения закаленного стекла
Таблица 1
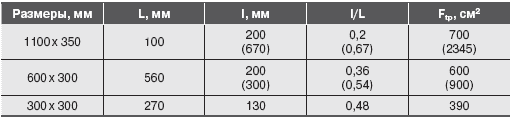
Техника эксперимента
При исследовании были использованы специальные и стандартные образцы из
отожженного и закаленного бесцветного флоат-стекла толщиной h = 4…12 мм:
Образцы были изготовлены на производственной линии на основе печи «Tamglass» HTF-ProE 2136.
Параметры испытаний на изгиб образцов по 4-точечной схеме (расстояние между нижними и верхними опорами — L и l, соотношение l/L и площадь рабочей части Ftp) даны в таблице 1.
Некоторые образцы были испытаны с параметрами, указанными в скобках, чтобы оценить влияние схемы нагружения на результаты испытаний. Показано, что результаты, полученные при разных схемах нагружения, были почти одинаковы для образцов с одинаковой толщиной, и они были сопоставимыми для всех трех типов размеров образцов.
Края образцов были шлифованы и полированы по обычной технологии для строительных стеклянных элементов.
Были использованы гидравлические испытательные машины ZD-4 и ZD-40. Скорость повышения изгибающих напряжений при испытании была в пределах 0,2…2 MПa/с в зависимости от гибкости образца и в соответствии со схемой его нагружения.
Специальный метод фрактографии был применен для изучения глубины и геометрических параметров поверхностных микротрещин — источников хрупкого разрушения в испытанных образцах отожженного и закаленного стекла [1, 2].
На рис. 1 показан метод определения предельных параметров микротрещины, характерных для стадии 1 докритического роста трещины с использованием микрофрактографии поверхности излома закаленного образца, испытанного при изгибе. Было установлено, что докритическая стадия 1 роста исходной микротрещины в закаленном стекле была аналогична установленной ранее на разрушенных образцах отожженного стекла [1]. Главная специфика картины разрушения возле источника излома для закаленных образцов состоит в «треугольной» форме зеркальной зоны, вытянутой вдоль поверхности стекла под влиянием остаточных сжимающих напряжений.
Но эта форма и размеры зеркальной зоны характерны для закритической стадии 3 динамического роста трещины. Увеличенная рельефность поверхности динамического разрушения, указанная на рис. 1, и микроосколки стекла на зеркальной поверхности вызваны повышенной скоростью разрушения под влиянием высокого остаточного внутреннего растягивающего напряжения в закаленном стекле. Более детальное описание анализа предельных параметров микротрещины приведено в [1].
На основе этих экспериментальных данных и линейной механики хрупкого разрушения было рассчитано сопротивление разрушению поверхности стекла qfs по уравнению:
qfs = KIc / Y1 Vb1 , (2)
где KIc — критическое значение коэффициента интенсивности напряжений;
в соответствии с нашими экспериментальными результатами было принято,
что KIc = 0,5 MПaVM для этого стекла;
b1 — предельное значение глубины b1 микротрещины в фокусе разрушения
на докритической стадии 1 роста трещины и образования формы поверхности
излома;
Y1 — геометрический параметр микротрещины в фокусе излома, зависящий
от соотношения b1/A1 на докритической стадии 1 роста трещины; A1 — длина
микротрещины, измеренная вдоль поверхности.
С использованием величины составляющей qfs был оценен фактический уровень
закалочных сжимающих напряжений возле источника разрушения в элементе
из закаленного стекла по уравнению:
qrs = qts – qfs (3)
Поэтому общее решение для оценки прочности термически упрочненных стеклянных элементов при изгибе может быть показано уравнением:
qts = qrs + KIc / Y1 Vb1 (4)
Результаты наших испытаний были проанализированы и сравнены с известными фундаментальными данными по HS- и FT-стеклу, полученными для 15 различных производственных линий [4] и другими результатами [3, 5].
Таблица 2
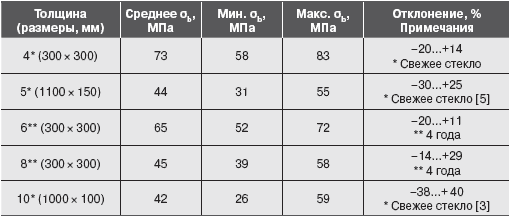
Сопротивление разрушению поверхности отожженного
и закаленного стекла
В табл. 2 показаны некоторые результаты по прочности на изгиб отожженного
стекла, полученные для различного состояния стекла и с использованием
разных образцов. Были испытаны образцы, изготовленные из листов свежего
стекла. Некоторые образцы до испытаний хранились 4 года в лабораторных
условиях.
В дополнение были использованы некоторые данные по прочности отожженного
стекла других авторов [3, 5].
Главная тенденция — это снижение прочности отожженного стекла при увеличении
толщины стекла (рис. 2).
Длительное хранение и небрежное обращение являются неприемлемыми для
прочной продукции из упрочненного стекла. Низкое исходное качество стекла
и недостаточный уровень механической обработки края стеклянных элементов,
плохо проконтролированные при переработке стекла, являются причинами
низких значений среднего и очень низкого уровня минимальной прочности
на изгиб — до 25…30 МПа. Это было убедительно показано Веером при статистически
достоверных испытаниях [3].
Рис. 3 показывает, что сопротивление поверхности разрушению qfs для
пластин из закаленного стекла ниже, чем исходная прочность отожженного
стекла qb. Это результат дополнительного подрастания наибольших поверхностных
микротрещин под влиянием термической обработки и контактных условий
при взаимодействии с твердыми элементами оборудования линии закалки.
Было показано, что при обычных условиях закалки глубина наибольших поверхностных
микротрещин может увеличиться в 3–5 раз по сравнению с исходной глубиной.
В результате этого уменьшается сопротивление разрушению поверхности
закаленного стекла, и нижняя граница экспериментальных значений qfs
слабо изменяется от 30 MПa для 4 мм до 20 MПa для стекла с толщиной
12 мм. Поэтому нежелательно использовать оценку прочности на изгиб закаленного
стекла qts, основываясь на результатах испытаний qb исходного отожженного
стекла. Согласно уравнению (1), фактическая прочность элементов из HS-
и FT-стекла может значительно изменяться в зависимости от качества процесса
закалки и эффективности контроля состояния поверхности стеклоизделия,
используемого в реальной производственной практике.
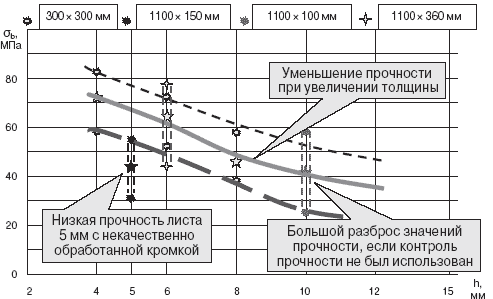
Рис. 2. Качество и прочность на изгиб отожженного стекла в зависимости от толщины пластин
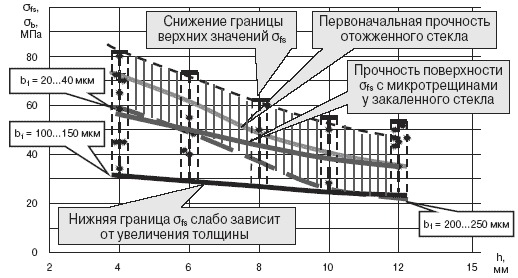
Рис. 4 показывает экспериментальные результаты прочности на изгиб ?ts для FT-стекла и малое влияние сопротивления разрушению поверхности упрочненного стекла qfs на их изменение в зависимости от различной толщины стекла.
Главным образом на прочность при изгибе закаленного стекла влияет уровень закалочных напряжений. Вид зависимости от толщины для прочности закаленных образцов не коррелирует с формой кривой изменения сопротивления разрушению упрочненного стекла. Вследствие того, что уровень закалочных напряжений значительно выше, чем сопротивление поверхности разрушению, нижняя граница значений прочности закаленных образцов qts повышается до 160…180 MПa для более толстого стекла, тогда как механическое сопротивление поверхности стекла qfs снижается до 20…30 MПa.
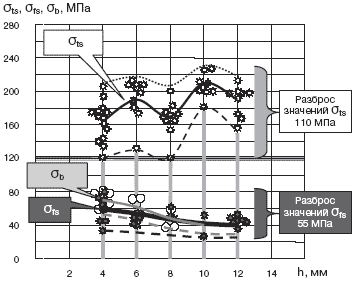
Рис. 4. Сопротивление поверхности разрушению и прочность на изгиб закаленного стекла в зависимости от толщины образцов
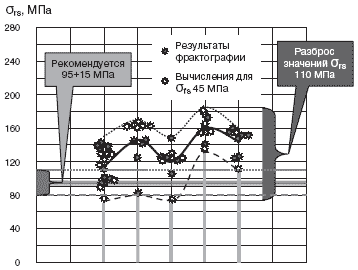
Рис. 5. Остаточные напряжения сжатия в образцах упрочненного стекла и качество закалки
Качество обработки стекла и прочность упрочненного
стекла
Рис. 5 показывает, что влияние термического упрочнения на прочность
упрочненного стекла с различной толщиной в первую очередь зависит от
уровня закалочных поверхностных напряжений сжатия qrs, прямо связанных
с качеством закалки и конкретным режимом термической обработки.
Чрезмерный фактический уровень закалочных напряжений сжатия (до 180
МПа вместо рекомендованных 80…110 МПа) и высокий разброс этих напряжений
(до 110 МПа) являются причинами избыточной прочности на изгиб и большой
дисперсии испытанного закаленного стекла. Чем выше остаточные напряжения
сжатия, тем выше прочность упрочненного стекла.
Отсутствие надлежащих механических испытаний стеклоизделий в рассмотренных
условиях производства и неэффективность стандартных средств неразрушающего
контроля поверхностных сжимающих напряжений в соответствии с EN 12150-2:2004
являются важными причинами неопределенности в оценке несущей способности
при конструкционном применении стекла. Это показано на рис. 6.
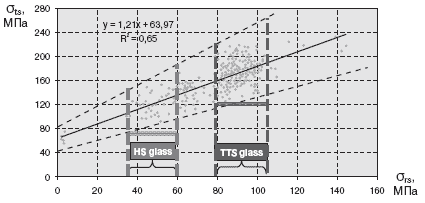
Рис. 6. Результаты Чиавонато [4] по прочности на изгиб термоупрочненного (HS)
и полностью закаленного (TTS) стекла в зависимости от поверхностных напряжений сжатия qrs , измеренных с использованием лазерного измерителя GASP в соответствии с EN 12 150-2:2004
Заключение
В статье показано, что вся технология термического упрочнения стекла
полностью определяет базовые составляющие прочности закаленного и термоупрочненного
стекла. Этими базовыми составляющими являются сопротивление разрушению
поверхности стекла и закалочные поверхностные напряжения сжатия, которые
должны быть точно контролируемы для обеспечения несущей способности
конструкционных стеклянных элементов в архитектуре. Новая экспериментальная
методика для точной оценки обеих составляющих изгибной прочности упрочненного
стекла, развитая в данном исследовании, может быть использована для
оптимизации технологических режимов закалки в перерабатывающей стекольной
промышленности.
Благодарности
Настоящее исследование выполнено благодаря финансовой поддержке Национальной
Академии наук Украины по научно-техническому проекту №9 и при технической
помощи Компании «Альтис-Гласс» — промышленного партнера по проекту.
Ссылки
Rodichev Yu.M., Netychuk A.V., Bodunov V.P., Yevplov Yu.N. Bending Strength
and Fracture of Glass Materials under the Different Loading Conditions,
«Glass Performance Days» Conf. Proc., Tampere, Finland, 2007. — PP 615–618.
Rodichev Yu.M., Influence of technology and scale effect on bending
strength of thermally strengthened flat glass elements. Journal «Translucent
constructions». — Sankt-Petersburg. — N 3 (59) 2008 — PP 43–51.
Veer F.A., Louter P.C., Bos F.P. The strength of architectural glass.-
Challenging Glass. Conference on Architectural and Structural Applications
of glass.-Faculty of Architecture, Delft University of Technology —
May 2008 — PP 419–428.
Schiavonato M., Mognato E., Redner A.S., Stress measurement, fragmentation
and mechanical strength — Proceedings of International Conference «Glass
Processing Days 2005» — Tampere, Finland — PP 92–95
Сorti R., Kaonpдд A., Nikkilд A.-P. Effect of different edges treatments
on the 4-point bending strength of normal and tempered glass — GPD-2005
Conf. Proc — Tampere — Finland — 2005 —PP 50–53.
Юрий Родичев, к.т.н.,
Институт проблем прочности им. Г.С. Писаренко НАН Украины, Киев, Украина,
Николай Трегубов, д.т.н., Kонстантиновское КНПП «Кварсит»,
Koнстантиновка, Донецкая область, Украина.
По материалам доклада на научно-практической конференции в рамках
Glass Performance Days 2009, Тампере, Финляндия