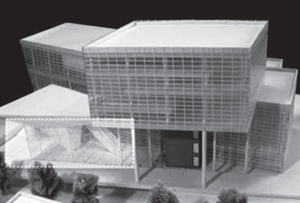
Рис. 1. Модель нового здания INHolland Polytechnic в г. Дельфт
ВВЕДЕНИЕ
Все стеклянные фасады с применением крупноформатных панелей нуждаются в системе стабилизации ветровой нагрузки и от влияния собственного веса. Безрамные фасады демонстрируют визуальную легкость, поскольку дневной свет не затеняется и не отражается металлическими профилями.
В результате экспериментов по проектированию и разработке композитного фасада для высшей школы INHolland Polytechnic в г. Дельфт (Нидерланды) была выбрана система, в которой предварительно натянутые тросы воспринимают усилия от горизонтальной (ветровой) нагрузки на фасад, а специальные стержни несут весовую нагрузку системы.
Как скрученные тросы, так и стержни размещены внутри полости изолирующих стеклопанелей. Предварительно напряженные тросы из арамида помещены внутрь труб, которые находятся между панелями стекла, составляющих однокамерный стеклопакет, а взвешивающие стержни размещены в области на краях, но тоже внутри панели-стеклопакета.
Как происходил процесс разработки, расчета и реализации стеклопанелей с нехарактерными новыми компонентами (изолирующая однокамерная стеклопанель и предварительно напряженные тросы со стержнями), описывается в этой статье.
ЭТАП ПРЕДВАРИТЕЛЬНЫХ ЭКСПЕРИМЕНТОВ
В высшей школе INHolland Polytechnic имеется лаборатория композитов, естественно желающая «возвестить о себе миру».
В 2007 г. там начались эксперименты по разработке стеклянной фасадной системы с применением композитов, к которой подключились специалисты из самой школы, специалисты из Лаборатории композитов, в частности, д-р Микаель Хагенбеек (dr. Michael Hagenbeek), два профессора из Дельфтского технологического университета (проф., д-р Ульрих Кнаак (Ulrich Knaack) и проф., д-р Мик Икхоут (Mick Eekhout)) и ряд инженеров из подрядных и надзорных организаций.
Главная роль отводилась архитекторам-проектировщикам, полагавшим, что фасад их конструкции будет единственным в своем роде и не будет тиражироваться. Однако архитектор Рийк Ритвельд (Rijk Rietveld) из Нью-Йорка имел ряд диких идей, которые трудно было поначалу воспринять. Этап предварительных экспериментов завершился наградой и выделением Голландского исследовательского гранта «SiaRaak», стимулировавшего исследования в политехнической школе.
Цель субсидии — продвинуть композиты и дополнить знания об этих материалах путем их применения в стеклокомпозитных фасадах. И главный вопрос — какие знания и опыт необходимы для применения композитов в стеклянных фасадах и архитектуре?
Композиты сочетают долговечность, неограниченную свободу по приданию различной формы, высокую прочность и жесткость при малом собственном весе. В архитектуре существует стойкий интерес к созданию прозрачных безрамных фасадов с новой необычной формой. Сочетание стекла и композитов ранее ограничивалось применением, например, в сэндвич-конструкцях, и только.
Амбициозные цели программы RAAK предполагали исследования и создание пригодной фасадной стеклокомпозитной конструкции, но также ставились и другие цели — трансфер знаний и обмен опытом в области композитов между конструкторско-проектировочными и архитектурными компаниями с одной стороны, и малыми и средними предприятиями (МСП) и исследовательскими центрами в отрасли композитов — с другой, в том числе для повышения уровня компетентности, также как и для распространения знаний, положительного и отрицательного практического опыта между МСП и ИСЗ (инфраструктура знаний).
Ставилась также отдельная задача по повышению уровня новых практических знаний в образовательном процессе, для чего было организовано взаимодействие с представителями отрасли по выпуску композитов.
Итак, все задействованные стороны в проекте — лаборатория INHOLLAND Composites lab, предприятие INHOLLAND Aerospace Technology, факультет архитектуры Дельфтского технологического университета, департамент строительных технологий, Технический комитет по строительству и недвижимости, Институт клеящих и полимерных составов Дельфтского технологического университета, Гаагский университет прикладных наук.
Команда разработчиков, окрыленная полученным грантом, в течение года занималась «мозговым штурмом», чтобы представить для дальнейшего рассмотрения ряд более или менее реалистичных схем с обязательным применением композитов (чтобы обозначить лидерство Лаборатории композитов не только среди отрасли композитов, но и в области фасадной архитектуры).
Участники время от времени сталкивались с трудностями, которые препятствовали им осуществить «квантовый скачок» в разрешении задачи.
В результате из-за наличия противоречивых требований все пришли к мнению, что необходимо изучить возможность интегрировать стабилизирующие и поддерживающие тросы и стержни внутрь полости фасадной стеклопанели, представляющей собой изолирующий стеклопакет, который ограничен и уплотнен композитной рамой из четырех специальных спейсеров вместо металлической дистанционной рамки.
Сами композитные спейсеры пронизываются композитными же трубками, в которых натянуты тросы — это и составляло суть изобретения, но от «дикой» идеи до ее воплощения лежал трудный путь тщательного проектирования и изготовления.
В завершение стадии предварительных экспериментов были созданы прототипы: на меньших моделях исследовалось поведение стеклянных панелей и адгезия уплотнителей к композитному спейсеру, герметичность труб и трубчатых крепящих оголовков; на полноразмерной модели сегмента разрабатываемого фасада (6,0 м в высоту и 4,5 м в ширину) со встроенными и предварительно напряженными тросами из арамида1, натянутыми внутри композитных труб между дистанционными спейсерами из композита в полости однокамерного стеклопакета.
1 Арамид (англ. aramid аббр. aromatic polyamide —
ароматический полиамид) — полипарафенилентерефталамид, синтетическое волокно
высокой механической и термической прочности. Состоит из бензольных колец,
соединённых друг с другом через группу -NH-CO-; между водородными и кислородными
отростками молекул соседних цепей образуются прочные водородные связи, обеспечивающие
высокую механическую прочность всего волокна. Наиболее распространены пара- и
мета- изомеры арамида — пара-арамид, известный под торговыми марками Кевлар,
Twaron и др., и мета-арамид, известный под торговой маркой Номекс.
(Прим. редакции)
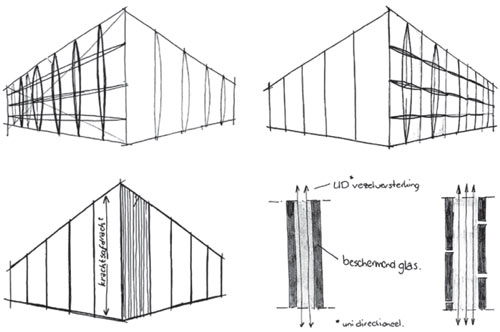
Рис. 2–5. Промежуточные результаты «мозгового штурма»
ЭКПЕРИМЕНТАЛЬНАЯ РАЗРАБОТКА НОВОЙ ФАСАДНОЙ СИСТЕМЫ
Особенности новой фасадной системы включают три пункта:
- Вставка труб из композита, пронизывающих спейсеры вверху и внизу
стеклопакета и ослабляющих и сами спейсеры, и общую устойчивость стеклопанели.
Поскольку кабели пронизывают спейсеры, находясь внутри углепластиковых труб, расположенных во внутренней полости стеклопакета, то необходимо создать надежную герметичность внутренней полости стеклопакета. - Вторая функция труб, как части фасада — передавать собственный вес фасада на
фундамент.
Размеры труб, тросов и спейсеров зависят друг от друга и сочетаются при очень малых допусках размеров.
По контуру фасадного элемента спейсеры из эпоксидного углепластика примыкают к краям стеклянных панелей. Эпоксикарбоновые проставки обладают подходящими характеристиками, например, хорошими показателями термоизоляции, прочности. Однако предстоит еще много поработать, чтобы добиться действительной прибавочной стоимости у углепластиковых спейсеров по сравнению с металлическими. - Противостояние ветровой нагрузке предварительно натянутых тросов, которые
выгибают фасадные элементы наружу, требуют тщательности в расчете углов деформации
панелей и учета возможного разрушения тросов, особенно в местах крепления труб,
при воздействии высокой ветровой нагрузки и постоянной динамической деформации
фасада.
Принципиально фасад высотой 13,2 м работает как парус. Изолирующий стеклопакет имеет незначительную свободу кручения. Одинаковые панели в связке на арамидовых тросах ведут себя как ожерелье. Ветровая нагрузка передается этими тросами. В условиях экстремально сильного ветра, что случается раз в 50 лет, фасад может выгнуться максимально на 330 мм безо всяких проблем.
Кевларовые тросы производства Phillystran inc. для крепления телевизионных вышек и радиоантенн состоят из параллельных кевларовых нитей с высоким модулем упругости (т.н. параллельная конструкция), защищенных коэкструдированной полиэтиленовой оболочкой. Эти тросы имеют отличную пожаропрочность и стойкость к переменным нагрузкам. Сейчас они применяются в мостах, башнях и на яхтах.
При инсталляции фасадов стеклянные панели временно крепятся к лесам-подмостям, находящимся внутри, тросы пропускаются сверху вниз, натяжение и контроль уровня натяжения происходит позже.
С точки зрения конструктива и несущих свойств панелей стеклопакетов при размещении тросов внутри полости между стеклами имеется ряд видимых преимуществ. Изнутри имеется множество поддержек для стекла, так что общий уровень деформации от изгиба в целом не высок. В результате оказалось, что в фасаде общей толщиной только 50 мм, состоящего из двух наружных стеклопакетов, обе стороны фасада оставались гладкими и выгибались одинаково.
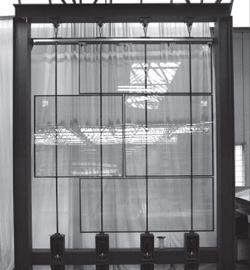
Рис. 6. Общий вид макета
ДОПОЛНИТЕЛЬНЫЕ ИСПЫТАНИЯ
Скорость реального процесса конструирования безжалостна к инженерам-экспериментаторам. Каждому, конечно, хочется испытать и то, и это, и не единожды, чтобы убедиться в надежности объекта проектирования, особенно когда речь идет о моделировании поведения на длительное время. Выбор часто возвращает к ранее испытанным элементам и удерживает от новых и неизвестных конструктивных решений или, в случае необходимости применения новых элементов, требует проведения быстрых испытаний и скорейшего возврата к уровню, обеспечивающему сертификацию, испытания индивидуальных аспектов одного за другим.
Некоторая нерешительность со стороны фирмы AGC была обусловлена сомнениями относительно степени соединения композитных труб с металлической дистанционной рамкой.
Несколько образцов композитных спейсеров для обеспечения воздухонепроницаемости были оснащены металлической рамкой, обращенной наружу стеклопакета.
В конце концов, подразделение по недвижимости INHolland Real Estate приняло решение использовать эту патентованную технологию в качестве первого заказчика для нового здания INHolland practical University в г. Дельфт.
Атриум состоит из трех фасадов. Композитный фасад демонстрирует инновационные возможности по применению композитов в архитектуре. Дальнейшее развитие и реализация фасада выполнялась фирмой Octatube, фасад из композитов сопровождался лабораторией INHolland Composite lab.
РАБОЧЕЕ ПРОЕКТИРОВАНИЕ
Окончанием этапа экспериментов было натурное моделирование на заводе. Для окончательного выбора решения для фасада строящегося здания новой школы Polytechnic School of INHolland был разработан и изготовлен образец как нового безрамнного фасада, так и изготовлен традиционный фасад.
Фирма Octatube настаивала на безрамном тросовом фасаде. В этот момент у фирмы Octatube поменялась роль со специалиста по разработке инновационного фасда на роль партнера по строительству, т.е. субъекта с более высокой степенью ответственности. Это обязывало обратить взгляд в строну имеющихся испытанных и применявшихся ранее систем.
Подрядчики и партнеры по реализации, такие как поставщик стекла AGC (Ashai Glass Company), тоже предстали перед необходимостью гарантировать заявленные характеристики и тоже вернулись к рассмотрению существующих решений и конструкций фасадов. Практика строительства и окончание разработки всегда приводит к некоторому изменению планов.
Лаборатория композитов была нацелена на применение спейсеров из композита, но макетирование показало, что степень адгезии уплотнителя варьируется, показатели не гарантируются, и не обойтись без целого ряда длительных лабораторных испытаний.
Практическое решение было в том, чтобы использовать привычную металлическую дистанционную рамку, металлические трубы и отказаться от тросов из арамида. Пока же Octatube сделал гигантский шаг в своем предложении — разместить противоветровые тросы внутри стеклопакетов (первоначально заказчик вообще отвергал такой вариант).
Во-вторых, мнение проф. Ульриха Кнаака убедило заказчика, и они согласились задействовать арамидовые тросы, но только в сочетании с металлической рамкой.
Позднее после некоторых колебаний AGC дало свои гарантии по системе из металлической рамки, арамидовых тросов, композитных труб и привычной бутил-силиконовой системе уплотнения.
СТРУКТУРНЫЙ АНАЛИЗ ФАСАДНОЙ СИСТЕМЫ
Фасад представляет собой планарную однонаправленную тросовую систему, которая придает устойчивость стеклянному фасаду путем сопротивления деформации благодаря преднапряженным тросам. Различие состоит в том, что эта система имеет значительный прогиб при максимальных допустимых эксплуатационных нагрузках. Остаточные деформации необходимы системе для передачи (ветровой) нагрузки. Система сопротивляется благодаря тенденции каждого троса к возврату на свое место вдоль прямой линии между своими опорами.
Максимальный расчетный прогиб фасадной системы составляет 1/40 к высоте фасада. В этом проекте высота фасада составляла 13 200 мм, т.е. максимальный выгиб составил 330 мм. Это означает к изгибу фасада под углом примерно 1°. Это сохраняет целостность стекла и уплотнителей и минимизирует негативное восприятие деформации фасада обитателями здания.
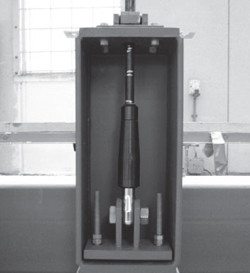
Рис. 7. Деталь макета
Первое впечатление от силы натяжения фасадных тросов можно охарактеризовать, просто глянув на рис. 7. В этой схеме вертикальные и горизонтальные изгибные усилия могут быть определены вычислениями. Ряд предпосылок указан ниже.
Все регулировки должны быть систематическими, последовательными, относиться ко всем тросам сразу, не быть локальными.
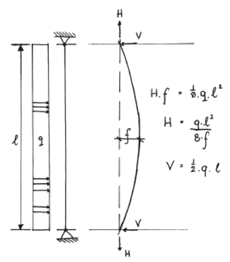
Рис. 8. Первые результаты вычислений с помощью простых формул
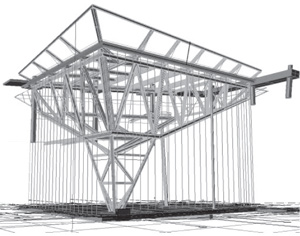
Рис. 9. Трехмерный вид конструкции (сталь-бетон), поддерживающей арамидовые (кевларовые) тросы
Основной вес на окружающие конструкции был сознательно отделен от ветровой нагрузки на фасад. Вес отдельных панелей воспринимается пружинящими шайбами в промежутке между двумя соседними однокамерными стеклянными панелями. Стержни опираются на буртики муфт, которые служат поддерживающими ступеньками. И шайбы подвески, и буртики муфты «утопают» в толщине двухслойного стеклопакета, но все зазоры впоследствии уплотняются. Шайбы подвески — из нержавеющей стали, муфты с буртиками — из POM (polyoxymethylene; полиоксиметилен, полиацеталь).
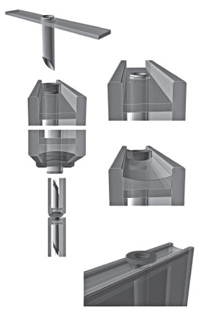
Рис. 10. Детали трубчатых элементов внутри стеклопакета
Весовая нагрузка воспринимается шайбами подвески, поскольку трудно выполнить механическое крепление непосредственно к арамидовому тросу.
Верхняя конструкция должна иметь хорошие условия закрепления, что не обеспечивалось сначала основной несущей структурой из-за того, что все решения по экспериментальному фасаду были приняты позже ее разработки.
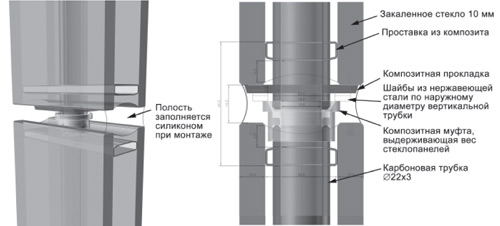
Рис. 11. Детали стекла
С внутренней стороны фасада были построены леса со сплошной
отмосткой, к которой можно было закрепить консольные балки. К этим балкам временно
(на период монтажа) по отдельности крепились стеклянные панели.
Леса со смонтированными на них панелями воспринимали всю ветровую нагрузку на
период монтажа, в то время как весовая нагрузка уже воспринималась через шайбы
и муфты.
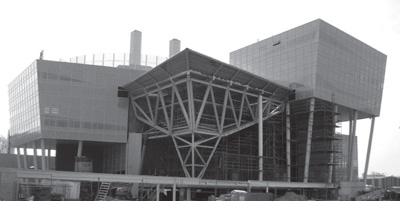
Рис. 12. Момент строительства (2009 г.)
При монтаже использовались дистанционные прокладки, позволяющие задать при монтаже правильный шаг разрядки по вертикали и по горизонтали. Однако они играли явно вспомогательную роль, поскольку панели хорошо центрировались муфтами, соединяющими трубы, проходящие внутри стеклопакетов, в которых протягивались натяжные тросы.
ЗАКЛЮЧЕНИЕ
Может показаться не совсем верным, что обещанные результаты и примененная для этого фасада технология в большей степени обязаны именно композитным материалам. В то же время, при более тщательном рассмотрении, окажется, что эта составная конструкция была создана в результате использования преимуществ и характеристик, присущих именно композитным материалам.
В процессе экспериментов были определены все параметры для этой несерийной конструкции. В этом процессе независимые группы действовали вместе и добились результата, несмотря на разноречивые собственные устремления. И все же нельзя сочетать экспериментальное строительство со строгими и короткими сроками реального строительства. Очень важно двигаться строго последовательно, пусть и малыми шагами, но шаг за шагом.
В целом отметим следующее. Были установлены общие требования к данной конструкции: обязательное применение композитов, ничто не должно выступать за края стеклопанелей.
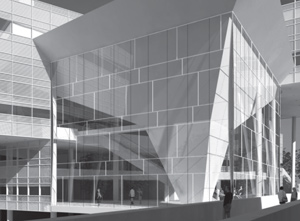
Рис. 13. Внешний вид тросового фасада (изображение от Rietveld Architects)
В результате долгих препирательств сторон, участвующих в проекте, удалось остановиться на варианте, который было на самом деле достаточно трудно реализовать, поскольку все несущие элементы должны были быть выполнены внутри двухслойных панелей-стеклопакетов, те есть уместиться в межстекольном зазоре 30 мм.
На стадии анализа осуществимости проекта было признано, что данную конструкцию можно выполнить средствами и технологиями, имеющимися на рынке.
Затем некоторые элементы конструкции фасада были проработаны более тщательно, особое внимание уделялось результатам тестирования долговременного поведения конструкции и ее стойкости. Здесь самые главные факторы — воздействие температуры и влажности на пластик композитов, примененных в фасаде, постоянно действующая переменная нагрузка.
Для изучения поведения реальной конструкции был создан действующий макет размером 3,6 м на 5,0 м. Макетирование не только подтвердило работоспособность конструкции, но и позволило отработать все трудности сборки, а также обеспечило необходимой технической информацией. Например, что вполне возможно сделать фасад с очень малыми допусками, менее 1 мм.
Разработанный фасад характеризуется рядом нововведений: концепция в целом, преднапряженные тросы с в трубах, размещенных между двумя стеклами изолирующей панели (стеклопакета), — это уникальное в мире решение. Применение здесь композитов — тоже, между прочим, эксклюзивный подход. Общий вид фасада — тонкое безрамное остекление высотой 13 200 мм. Это означает, что создан очень тонкий фасад с соотношением толщины к высоте более 1:300.
Стадии начала строительства предшествовал «мозговой штурм» по разработке общего дизайна и концепции, выразившийся в создании рабочего макета-прототипа. Скорость рабочего проектирования была достаточно высока по сравнению со скоростью интеллектуальных процессов при разработке проекта.
Первоначальная «дикая идея» была в итоге трансформирована во вполне работоспособный проект, способный быть передовым в течение десятилетий. Процесс проектирования требовал пошагового выполнения множества испытательных процедур, которые гарантировали бы надежность и долговечность реальной конструкции.
Заказчик, желавший помимо прочего за счет реализации этого проекта улучшить свой имидж, проявил достаточную терпеливость в отношении некоторых непредвиденных задержек. Постройка фасада от идеи до воплощения займет в целом ряд лет.
Проф., д-р Мик Икхоут (Mick Eekhout),
Octatube International bv,
Технологический университет, г. Дельфт, Нидердланды
Петер Ван де Роттен (Peter van de Rotten),
Octatube International bv,
г. Дельфт, Нидердланды
По материалам доклада на Glass Performance Days, июнь 2009 г.,
Тампере, Финляндия.