Решение задачи эффективной борьбы с образующейся при обработке древесины пылью, и особенно с ее мелкой фракцией, приводит к необходимости с одной стороны, сберечь тепло, т.е. максимально рециркулировать очищенный воздух, с другой стороны обеспечить ПДК пыли в рабочей зоне. Это не только скажется на здоровье рабочих, но и на долговечности оборудования и блоков его управления, качестве выпускаемой продукции. Задача пылеудаления решается применением местных и централизованных аспирационных систем и систем приточной вентиляции.
Эффективное пылеудаление
Производительность удаления пыли определяется конструкцией местного пылевоздухозаборника
(уже готового, сконструированного и установленного производителем деревообрабатывающего
оборудования), а также правильно рассчитанной проектировщиком скоростью
воздуха в каждом вентиляционном канале. Часто производитель самих станков
не утруждает себя разработкой высокоэффективного пылеудаляющего насадка,
именно поэтому приходится изменять, а иногда и заменять конструкцию типового
пылевоздухозаборника, добавляя патрубки и насадки, через которые пыль
удаляется от станка в общую систему аспирации. Добавление же патрубков
приводит к необходимости изготовления коллектора и пересчета объемов и
скоростей удаляемой газопылевой смеси. При этом необходимо обеспечить
минимальную турбулентность воздушного потока вдоль пылевоздухозаборника
и равномерную эпюру скорости по его сечению, и, таким образом, избежать
появления циркуляционных завихрений и «мертвых зон», способствующих оседанию
пыли в самом канале пылеудаления. Пыль, скапливающаяся в воздуховодах,
не только снижает со временем эффективность пылеудаления, но и повышает
пожароопасность в производственных помещениях.
Это не типовая задача вентиляции. Удачная конструкция пылевоздухозаборника
позволяет повысить его эффективность до 98-99%. Оставшиеся (1-2)%, если они не укладываются в нормы ПДК, приходится «разбавлять» за счет воздуха, подаваемого приточной системой. Разработка, изготовление и установка высокоэффективного «укрытия» станка — работа, которая не ограничивается только расчетами. Часто она сопряжена с переделкой казалось бы пригодных и работоспособных конструкций. Важный аспект, влияющий на эффективность пылевоздухозаборника, — это подбор гибкого соединения между подвижной частью до станка и неподвижной общей системой аспирации. При выборе типа рукава для конкретной операции обработки древесины нужно руководствоваться следующими соображениями: при скорости в системе порядка 30 м/сек рукав должен выдерживать разрежение не менее 10 КПа (или 1000 мм вод. ст., или 0,1 бар или 0,1 атм или 0,01 МПа) и, в зависимости от типа удаляемой пыли, быть абразивостойким. |
![]() Традиционный воздухоочиститель из двух циклонов и бункера-накопителя стружки |
Для определения стратегии в решении задачи повышения эффективности очистки воздуха необходимо провести замеры: реальных расходов воздуха всех аспирационных систем; запыленности воздуха в рабочей зоне; количества загрязняющих веществ в системе (до и после фильтрующего оборудования).
Обычно для этого привлекается сертифицированная и аккредитованная
в данном регионе лаборатория. Результаты квалифицированных замеров
позволяют правильно выбрать количество ступеней очистки и подобрать
для каждой ступени подходящее газоочистное (ГО) оборудование. Если в выделяющейся при обработке пыли мелкой фракции мало (менее 5% от всей пыли), то возможен возврат всего очищенного воздуха обратно в цех (рециркуляция) без дополнительной очистки воздуха. Если доля мелкой фракции в древесной пыли велика (более10%) — количество возвращенного воздуха обратно в цех можно рассчитать по количеству пыли и производительности приточной системы. В этом случае количество рециркулируемого воздуха обычно не превышает 50%. При высокой степени очистки или при добавлении третьей ступени очистки возможно 100% очищенного воздуха вернуть обратно и таким образом экономить на нагреве (охлаждении) приточного воздуха. |
![]() Блок тканевых кассетных фильтров фирмы Amtech (США) |
ПРОЕКТИРОВАНИЕ СОВРЕМЕННОЙ рециркуляционной АСПИРАЦИОННОЙ
СИСТЕМЫ ДЕРЕВООБРАБАТЫВАЮЩЕГО ЦЕХА
Аспирационная система деревообрабатывающего цеха предназначена для создания
нормативных санитарно-гигиенических условий труда на рабочих местах у
станков. С помощью аспирационной установки от станков удаляются стружки,
пыль и создаются нормативные санитарно-гигиенические условия труда.
Аспирационные установки бывают автономные и централизованные, прямоточные
и рециркуляционные. до недавнего времени на деревообрабатывающих предприятиях
России устанавливались и эксплуатировались преимущественно централизованные
прямоточные аспирационные установки с циклонами. При работе таких установок
пылевоздушная смесь, отсасываемая вентилятором от станков, подается в
циклон, установленный на бункере для древесных частиц. При этом древесные
частицы попадают в бункер, а воздух, очищенный в циклоне от пыли, выбрасывается
в атмосферу [1].
Прямоточные централизованные аспирационные установки с циклоном имеют
ряд существенных недостатков. Во-первых, они очищают пылевоздушную смесь
от пыли только на 70…90% и, выбрасываемый в атмосферу воздух загрязняет
окружающую среду. Во-вторых, в зимнее время года огромные потоки теплого
воздуха выбрасываются из цеха на улицу, а в цех поступает холодный воздух,
который предварительно надо подогреть. Это делает аспирационную систему
цеха чрезвычайно энергоемкой в зимнее время года.
В последнее десятилетие в нашей стране стали широко внедряться централизованные
рециркуляционные аспирационные системы. В таких аспирационных установках
пылевоздушная смесь, удаляемая от станков, очищается рукавными фильтрами
(степень очистки до 99,9%) и возвращается обратно в цех. При проектировании
таких аспирационных установок возникла необходимость решения ряда практических
задач:
На кафедре станков и инструментов Уральского государственного лесотехнического университета ведется работа по решению указанных задач.
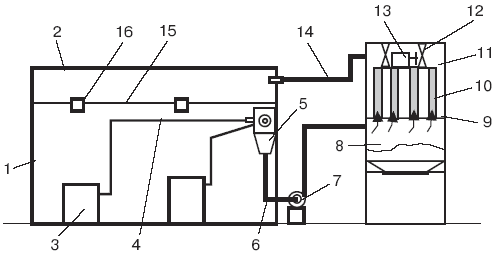
Рис. 1. Схема централизованной рециркуляционной аспирационной системы деревообрабатывающего цеха
На рисунке 1 схематично показан пример поперечного разреза цеха.Аспирационная система содержит стены 1 и крышу цеха 2, деревообрабатывающие станки 3, всасывающие воздуховоды 4, подсоединенные к коллектору-сборнику 5, который соединен воздуховодом 6 с вентилятором 7, смонтированным за стеной цеха. Вентилятор соединен воздуховодом с бункером-накопителем древесных частиц 8.
На верхней перегородке бункера 9 установлены тканевые рукавные фильтры 10, верхние концы которых закреплены на решетке 11, подвешенной на перекрытии бункера на цепях 12. На решетке установлен вибратор 13. Верхняя зона бункера соединена с цехом воздуховодом 14, который входит в цех в пространство, образованное крышей цеха и деревообрабатывающим полнительным потолком 15, в котором выполнены отверстия 16, расположенные над станками 3 [2].
Система работает следующим образом. Образовавшиеся древесные частицы (опилки, стружка, щепа и т.д.) под воздействием воздушного напора, созданного вентилятором 7, отсасываются от станков и перемещаются по воздуховодам 4 в коллектор-сборник 5, а из него выносятся из цеха и через вентилятор по воздуховоду попадают в бункер-накопитель 8. Крупные частицы оседают на дне бункера, а запыленный воздух устремляется в рукавные тканевые фильтры 10. Пройдя через стенки рукавов, воздух очищается от пыли, пыль задерживается на внутренних стенках рукавов. Через каждый час работы рукава встряхиваются вибратором 13 и очищаются от налипшей пыли. Древесные частицы, накопившиеся на дне бункера, выгружаются через нижний люк в автомобильный транспорт и увозятся. Очищенный воздух возвращается по воздуховоду 14 обратно в цех.
В цехе воздух отсасывается от станков, в зоне станков образуется разряжение. В зону разряжения воздух устремляется из отверстий 16. Путь движения струи воздуха в рабочем пространстве цеха сокращен до минимума и измеряется расстоянием от потолка до станка. При этом путь струи не пересекается с рабочей зоной рабочего, и рабочий не подвержен действию сквозняков.
Таким образом, предложенная схема возврата очищенного теплого воздуха к станкам позволяет уменьшить сквозняки в цехе при работающей аспирационной установке и уменьшить количество пылевой взвеси в воздухе.
Расчет рукавных фильтров
Гидравлическое сопротивление рукавного фильтра ?р можно определить по
следующей формуле, Па:
dP = (dPуд*Q) / S
где dPуд — удельное гидравлическое сопротивление, Па.ч/м, для тканевых
рукавных фильтров можно принять ?руд = 10-15 Па.ч/м;
Q — производительность фильтра по воздуху, м3/ч;
S — площадь фильтрации рукавов, м2.
При расчете задаются значением ?р в пределах от 900 до 1200 Па. Из предложенной
формулы находят площадь фильтрации рукавов. Затем задаются диаметром
рукава (120-140 мм) и длиной (обычно 1,5…2,0 м). Находят поверхность
одного рукава, а затем — количество рукавов.
Все рукава следует распределить по блокам. В зависимости от производительности
аспирационной системы количество блоков можно принять от 2 до 4 и более.
На рисунке 2 предлагается схема размещения рукавов в блоке фильтра.
В каждом блоке должно быть одинаковое количество рукавов. В связи с
этим количество рукавов может быть увеличено. Окончательно уточняется
площадь фильтров и их гидравлическое сопротивление.
Для расчета параметров аспирационной системы разработана компьютерная
программа, применяемая в учебном процессе.
Деление фильтра на несколько блоков позволяет ремонтировать и заменять
тканевые рукава без остановки цеха. При этом каждый блок поочередно
может быть извлечен для осмотра и ремонта из фильтра и на его место
ставится заслонка.
Рециркуляционная схема аспирационной системы существенно экономит тепловую
энергию в холодное время года и снижает затраты на охлаждение производственных
помещений в жару. Помимо экономии энергоносителей такая система позволяет
организовать «закрытую» схему воздухооборота с минимальным притоком
внешнего воздуха, который подвергается кондиционированию, то есть оптимизировать
и стабилизировать влажность воздуха в цехах независимо от времени года
или суточных колебаний влажности в атмосфере, что безусловно положительно
сказывается на качестве деревообработки.
Решение S = (dPуд*Q) / dP = 102100 / 1300 = 161,5 м2. 3. Определим поверхность фильтрации одним рукавом S1 = пи*d*l = 3,14 . 0,15 . 2 = 0,942 м2. 4. Необходимое количество рукавов n = S/S1 = 161,5/0,942 = 171,4 шт. 5. Принимаем фильтр, состоящий из 6 блоков по 30 рукавов в каждом
блоке. Тогда потребуется 180 рукавов с площадью фильтрации Sф
= 0,942.180 = 169,56 м2. dP = (dPуд*Q) / Sф = 102100 / 169,56 = 1238,5 Па. |
«Проектирование современной аспирационной системы
деревообрабатывающего цеха»,
Глебов И.Т., Глебов В.В.
(УГЛТУ, г. Екатеринбург, РФ)
на форуме: Международный евразийский симпозиум «Деревообработка: технологии, оборудование, менеджмент».