Количество отходов зависит от породы, сортности, размеров и влажности
раскраиваемых пиломатериалов, характера готового изделия и составляет
от 20 до 85% объема пиломатериалов. На разных предприятиях при выпуске
однородной продукции количество отходов неодинаково. Это зависит как
от используемых пиломатериалов, так и от технологии производства. Влажность
отходов определяется влажностью обрабатываемой древесины. В зависимости
от влажности отходы могут быть сухие (до 15%), полусухие (16–30%), влажные
(31% и более). Влажность отходов имеет большое значение для дальнейшего
их использования, а также для учета.
По использованию мелких древесных отходов (опил, станочная стружка, дробленка
и т.д.) предпринимались попытки получения плитных материалов: пьезотермопластики,
лигноуглеводные древесные пластики, арболит, фибролит, опилкобетон. Однако
для получения указанных материалов требуется размольное, сушильное, формирующее,
транспортное оборудование. К тому же все эти материалы имеют высокую плотность
и требуют использования цементов высоких марок.
Целью данных исследований являлось изучить возможность получения древесно-минерального
композиционного материала из смеси мелких древесных отходов и щелочных
силикатов.
Для приготовления древесно-минеральной композиции использовали древесные
отходы (опил, станочная стружка) и жидкое стекло, с добавками инициатора
твердения. В качестве инициатора использовался технический гексафторсиликат
натрия.
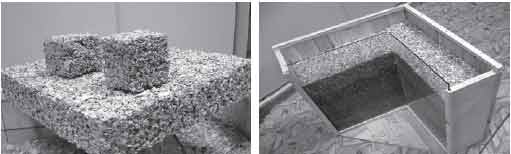
Рис. 1. Теплоизоляционный материал в виде блоков и с использованием заполнения стенового пространства
Предлагаемый теплоизоляционный материал (рис. 1.) можно изготовить, используя
любые мелкие древесные отходы (отходы лесопиления, станочная стружка и
опилки) и щелочные силикаты. Смешивая указанные компоненты, получают текучую
массу, которой можно заполнить межстеновые полости, любые пустоты в межкомнатных
перегородках и других подобных конструкциях.
Влажность древесных частиц может быть 2–180%. Ограничений по количеству
коры нет.
Результаты исследований по получению теплоизоляционного материала представлены
на графиках (рис. 2–5 ).
На рис.2 представлена зависимость предела прочности при сжатии от количества
вводимого в жидкое стекло гексафторсиликата натрия после суточной и трехсуточной
выдержки при температуре 18-20°С. Полученные данные говорят о том, что
предел прочности при сжатии увеличивается до 1,75 и 2,5 кг/см2. В связи
с этим можно рекомендовать добавлять в жидкое стекло гексафторсиликат
натрия в количестве 10%.
При изготовлении композиционного материала важное значение имеет определение
соотношения древесного заполнителя и жидкого стекла, что обусловливает
необходимую прочность материала при сжатии.
Из рис.3 можно заметить, что ?сж напрямую зависит от количества жидкого
стекла, добавляемого в древесный заполнитель. Рассматриваемые соотношения
(от 1:0,5 до 1:4) позволяют сделать вывод о том, что соотношение древесины
к щелочному силикату 1:3 позволяет получить прочность материала при сжатии
на уровне 9,8 кг/см2.
Сравнительная характеристика композиционного теплоизоляционного материала
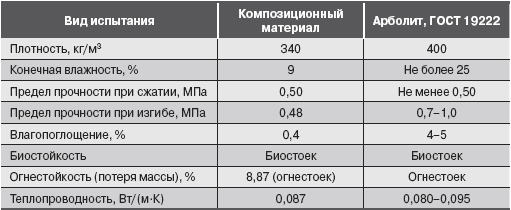
На рис.4. представлена кривая обезвоживания жидкого стекла с добавкой
гексафторсиликата натрия. Ясно видно, что влага выделяется из образца
при температуре до 200°С. Образец же представляет собой сильнопористую,
полупрозрачную массу, с коэффициентом рефракции 1,44 у стекла =?1,477.
В результате удаления влаги наблюдаются усадочные явления и вспучивание
образца. При нагревании выше 200°С до 500°С не наблюдается изменений в
микроструктуре образца.
На рис.?5 представлены кривые влагопоглощения древесины сосны и композиционного
материала. Опытные образцы изготавливались в соотношении 1:3 (древесина
— щелочной силикат), но древесные частицы брались разной исходной влажности
(2%; 8%; 80%; 240%). Видно, что влагопоглощение композиционного материала
несколько больше, чем сосны. Это можно объяснить тем, что композиционный
материал состоит из развернутой поверхности. Материал является открыто
пористым. Повышенное влагопоглощение у композиционного материала можно
объяснить и тем, что вначале происходит неполное твердение геля кремнезема,
который еще не утратил способность поглощать влагу из воздуха.
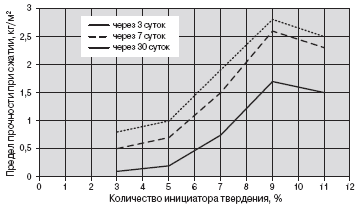
Рис. 2. Влияние количества инициатора твердения на предел прочности при сжатии
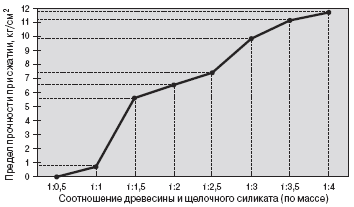
Рис. 3. Предел прочности при сжатии образцов полученного материала
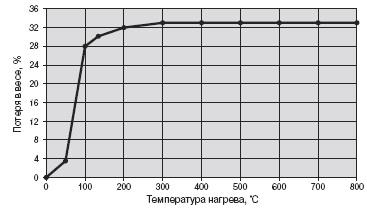
Рис. 4. Обезвоживание при нагреве затвердевшего жидкого стекла с добавкой мелких древесных частиц с большой долей кремнефтористого натрия
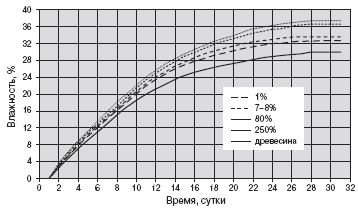
Рис. 5. Влагопоглощение испытуемых образцов материала
Выводы
Экспериментальные данные позволяют утверждать, что имеется возможность
получить теплоизоляционный материал с использованием щелочных силикатов
при соотношении древесины и щелочного силиката 1:3. В то же время появляется
возможность утилизировать мелкие древесные отходы в широком влажностном
диапазоне и исключить образование свалок, нарушающих экологический баланс
любой местности.
Добавление к щелочным силикатам гексафторсиликата натрия в количестве
10% создает условия для более полного выделения геля кремнезема, который
по мере обезвоживания цементирует древесный заполнитель.
Предел прочности при сжатии приближается к значению показателя для такого
материала, как фибролит. Полученный композиционный материал транспортабелен
и у него достаточная технологическая прочность при сравнительно небольшой
плотности (250-300?кг/м3).
Предлагаемый композиционный материал устойчив к биологическому разложению,
экологически безопасен, обладает меньшей возгораемостью, чем массивная
древесина.
Предлагаемый теплоизоляционный материал (теплопроводность 0,087) можно
использовать в домостроении для теплоизоляции межкомнатных перегородок.
С точки зрения вопросов по изготовлению данного материала, то его производство
не требует сложного технологического оборудования.
Библиографический список
Бухаркин В.И., Свиридов С.Г., Умняков П.Н. Использование древесных отходов
для производства арболита. — М.: 1975. — 192 с.
Вьюнков С.Н. Технология древесных плит с использованием связующего на
основе жидкого стекла. — М.: 1999. — 151 с.
Коробов В.В. Комплексное использование низкокачественной древесины и отходов.
— М.: 1973. — 241 с.
По материалам доклада Говорова Г.Г., Ветошкина Ю.И.,
Корюковой Ю.А., УГЛТУ,
г. Екатеринбург, на III Международном евразийском симпозиуме «Деревообработка:
технологии, оборудование, менеджмент XXI века» в рамках I Евро-Азиатского
лесопромышленного форума, 30 сентября – 3 октября 2008 г., г. Екатеринбург,
РФ