При формовании стекла флоат-способом стекломасса через дозирующее устройство
сливается в ванну с расплавом олова, растекается, принимая форму плоскопараллельной
ленты. Заданную ширину и толщину лента приобретает после воздействия на
нее бортоудерживающих машин и усилия роликового конвейера печи отжига.
По длине ванны с расплавом олова ширина и толщина ленты стекла изменяются.
Измерение ширины ленты в ванне расплава на различных этапах формования
доступно и в настоящее время достаточно хорошо изучено.
Информация об изменении толщины ленты в процессе формования ограничена
и носит противоречивый характер. Одни источники говорят о том, что лента
стекла в процессе растекания до места установки бортоудерживающих машин
должна приобрести равновесную толщину. Другие, наоборот, что без ограничения
растекания в стороны бортов ванны расплава можно получить стекло толщиной
до 12 мм.
Измерение толщины ленты стекла в процессе формования затруднено рядом
объективных причин и, прежде всего, необходимостью доступа измерительных
приспособлений к нижней части ленты, погруженной в олово, движущейся и
находящейся в вязкотекучем состоянии.
Сведения о методах измерения толщины ленты стекла в ванне расплава ограничены
и не носят практического характера (пат. США 3356479, а.с. СССР 837944).
Саратовский институт стекла разработал и использовал на промышленной линии
метод определения толщины ленты стекла в ванне расплава на различных этапах
формования. Этот метод достаточно прост и доступен.
Метод основан на принципе, в соответствии с которым через каждое сечение
ванны расплава, перпендикулярное направлению перемещения ленты, в единицу
времени проходит одно и то же количество стекломассы:

где Q — количество стекломассы, кг/ч;
d — толщина ленты, м;
b — ширина ленты, м;
n — скорость продвижения ленты через данное сечение, м/с;
r — плотность стекла, кг/м3.
Толщина ленты в сечении выражается формулой:

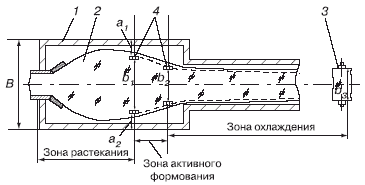
Рис. 1. Схема ванны расплава
Ь1 и Ь2 — ширина ленты стекла в зоне соответственно первой и второй пары бортоудерживающих машин; Ь3 — ширина ленты стекла на выходе из печи отжига; В — ширина ванны с расплавом олова; а1 и а2 — расстояние удаления роликов бортоудерживающих машин соответственно от правого и левого бортов ванны
На рис. 1 приведена схема установки для выработки флоат-стекла и обозначены
измеряемые параметры в соответствии с разработанным методом.
Установка включает в себя ванну 1 с расплавом олова, по которой перемещается
лента стекла 2. Усилие для перемещения ленты создается роликовым конвейером
печи отжига 3. Формование ленты с целью получения заданных геометрических
характеристик осуществляют несколькими парами бортоудерживающих машин
4. Отпечатки от воздействия машин на ленте стекла обозначены пунктирными
линиями.
В процессе измерений все технологические параметры поддерживают постоянными.
Для определения производительности измеряют b3, d3 и n3 (соответственно
ширину, толщину и скорость перемещения ленты на выходе из печи отжига)
и рассчитывают ее по формуле (1).
Ширина ленты в зоне размещения первой пары бортоудерживающих машин при
счете от слива может быть определена как разница между шириной ванны и
суммарным расстоянием удаления роликов бортоудерживающих машин от бортов
ванны:
b1 = B – (a1 + a2) ,
где b1 — ширина ленты в зоне размещения первой пары бортоудерживающих
машин, м;
В — ширина ванны с расплавом олова, м;
а1 и а2 — расстояние удаления роликов бортоудерживающих машин соответственно
от правого и левого бортов ванны, м.
За скорость перемещения ленты принимается линейная скорость ролика или
тракового набора в зоне контакта с лентой стекла. Для этой части ленты
определяется толщина по формуле (2). Толщина средней части ленты в этом
же сечении может несколько отличаться от полученного значения.
Для последующих пар машин выполняются аналогичные измерения и расчеты
при неизменной производительности. Точность определения толщины ленты
зависит от точности измерения параметров, входящих в формулу, и может
составлять ± 3 %. Если необходима более высокая точность, то в формулу
(1) вносят поправку на изменение плотности стекла в зависимости от температуры,
при которой осуществляются измерения.
Измерения толщины выполнены на флоат-установках мощностью 100, 400 и 600
т/сут. На рис. 2 показано изменение толщины на различных этапах формования
при выработке стекла толщиной менее равновесной.
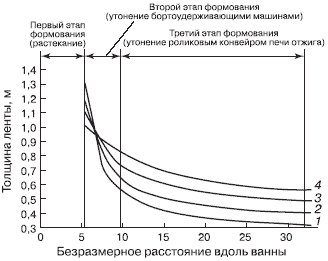
Рис. 2. Изменение толщины ленты стекла в ванне расплава
1, 2, 3 и 4 — толщина ленты на выходе из печи отжига
соответственно 3, 4, 5 и 6 мм
Установлено, что толщина ленты стекла на первом этапе (растекание) составляет
10 мм и более. Только после воздействия бортоудерживающих машин на втором
этапе толщина ленты становится близкой к равновесной. На третьем этапе,
где утонение осуществляют за счет воздействия роликового конвейера печи
отжига, утонение ленты сопоставимо с ее утонением на втором этапе.
Чем меньше толщина вырабатываемого стекла, тем больше толщина ленты на
границе зон растекания и активного формования. В частности при выработке
стекла толщиной 3 мм она составляет 13 мм, а при выработке стекла толщиной
6 мм — примерно 10 мм. Таким образом она в любом случае существенно больше
равновесной толщины. Равновесная толщина реально достигается в зоне воздействия
на ленту бортоудерживающих машин.
Если рассматривать последовательное изменение толщины по зонам формования,
то воздействие бортоудерживающих машин на ленту обеспечивает уменьшение
ее толщины практически вдвое, после чего усилием роликового конвейера
печи отжига она еще раз утоняется от 1/3 до 2 раз.
Таким образом в условиях выработки лента стекла приобретает равновесную
толщину не за счет свободного растекания, а прежде всего в результате
воздействия бортоудерживающих машин.
Следует отметить, что кроме определения толщины ленты в заданных сечениях
разработанный метод может использоваться для решения других задач. В частности
по заданной толщине в зонах формования можно выполнять расчет других параметров
ОАО “Саратовский институт стекла”