Пеностекло — пористый тепло- и звукоизоляционный материал с истинной
пористостью до 85-95%. В зависимости от назначения пеностекло может быть
с замкнутыми или с сообщающимися порами. Для теплоизоляции применяют пеностекло
с замкнутыми порами, а для звукоизоляции — с сообщающимися. В промышленных
условиях производство теплоизоляционного петостекла занимет преимущественное положение.
Кроме этого, в незначительных количествах вырабатывают пеностекло специального
назначения — высокотемпературное, химически стойкое и др.
Производят пеностекло порошковым методом, т.е. спеканием смеси стекольного
порошка с добавками материалов, способствующих образованию газовой фазы
при нагревании (газообразователей).
Подбирая состав стекла и газообразователей, способы их подготовки и технологические
параметры, получают конечный продукт со строго заданными свойствами: малой
средней плотностью, равномерно распределенными мелкими порами, малым коэффициентом
теплопроводности и другими. Для получения пеностекла применяют специально
сваренные стекломассы, а также бой оконного, тарного и других стекол.
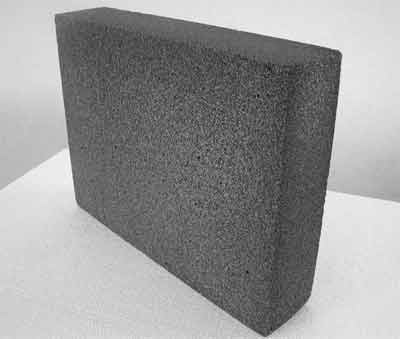
Рис. 1
Блок пеностекла может применяться целиком или разрезаться на детали нужной
формы и объема
Стекло и газообразователи для пеностекла
Получаемое порошковым способом пеностекло имеет много общего с вспененными
жидкостями. Пеностекло представляет собой грубодисперсную систему (твердую
пену), газовая дисперсная фаза которой распределена в меньшей по объему
твердой дисперсионной среде (стекле). Форма ячеек, в которые заключена
газовая фаза, может быть сферической, а чаще всего, благодаря давлению
газов в соседних ячейках — полиэдрической.
При вспенивании стекольного расплава, как и жидкостей, процесс порообразования,
при прочих равных условиях, идет тем совершеннее, и пена бывает тем устойчивее,
чем меньше поверхностное натяжение на границе жидкость-газ. В отличие
от пенообразования в жидкостях, процесс вспенивания пеностекольной массы
идет при повышенной температуре, высокой вязкости стекла, увеличенном
давлении газовой фазы и незначительном изменении поверхностного натяжения.
При подборе стекол и газообразователей для производства пеностекла порошковым
методом исходят из специфических условий пенообразования в высоковязком
стекольном расплаве. Процесс образования пор должен протекать плавно,
постепенно. При этих условиях в большей мере обеспечивается получение
ячеистой структуры, равномерных по размерам замкнутых пор. Условиям плавного
течения процесса порообразования отвечают “длинные” стекла, вязкость которых
мало изменяется в сравнительно большом температурном интервале. Кроме
этого, в процессе пенообразования, протекающего в интервале вязкости 1-10
МПа.с, стекломасса не должна кристаллизоваться. Стекло должно также содержать
окисляющие компоненты SО3, Аs2О3, Sb2О3 и др.
К газообразователям пеностекла предъявляются следующие основные требования:
газовая фаза при нагревании должна выделяться только после полного спекания
стекольного порошка; возрастание давления продуктов разложения газообразователя
в температурном интервале спекания должно быть не резким, а плавным. Из
всего многообразия газообразователей в промышленных условиях находят применение
главным образом углеродистые газообразователи и в меньшей степени некоторые
карбонаты, в частности известняк, доломит. Углеродистые газообразователи
применяют в тех случаях, когда нужно получить теплоизоляционное ячеистое
пеностекло с замкнутыми порами. Для получения пеностекла с сообщающимися
порами применяют известняк. Применяются и углеродистые газообразователи:
кокс, различные виды активной сажи, чешуйчатый графит, карбид кремния.
Углеродистые газообразователи применяются при вспенивании пеностекольных
масс в интервале 780-950°С. Известняк относится к сравнительно низкотемпературным
газообразователям. Температура вспенивания пеностекольных масс, содержащих
известняк 750-780°С.
Для получения теплоизоляционного пеностекла чаще всего применяют стекла,
близкие по химическому составу к составам листовых и тарных стекол с повышенным
содержанием щелочных оксидов. Составы стекол, %: SiО2 — 72-73; Al2О3 —
0,5-2; CaО — 6-8; MgО 1-4; Na2O — 15,5-16,5; SO3 — 0,3-0,5. Для некоторых
специфических условий применения пеностекла могут применяться составы
стекол, значительно отличающиеся от приведенных выше, например, боросиликатные
и малощелочные. Так, для изоляции промышленных холодильных установок рекомендуется
химически стойкое стекло следующего состава, %: SiО2 — 71,6; Al2О3 — 1,3;
В2О3 — 1,9; СаО — 3,7; MgО — 2,8; Na2O — 12,7; SO3 — 0,3; As2О3 — 0,1;
Sb2О3 — 0,2.
Свойства пеностекла
Пеностекло при теплопроводности, равной теплопроводности лучших теплоизоляционных
материалов, превосходит их по ряду других показателей. Пеностекло влагопаронепроницаемо,
обладает высокой механической прочностью, негорюче и удовлетворяет высоким
санитарно-гигиеническим требованиям, так как оно биологически стойко —
не гниет и не плесневеет. Средняя плотность различных видов пеностекла
колеблется от 160-180 до 200-300 кг/м3.
Механические свойства пеностекла зависят от его средней плотности и диаметра
пор и составляют для мелкопористого пеностекла со средней плотностью 180-200
кг/м3:
— сопротивление сжатию: 0,88 МПа;
— сопротивление изгибу: 0,59-0,69 МПа;
— сопротивление растяжению: 0,44-0,49 МПа.
Теплопроводность пеностекла определяется соотношением твердой и газообразной
фазы. Чем больше содержание газообразной фазы, т.е. чем больше пористость
пеностекла, тем меньше его теплопроводность. Коэффициент теплопроводности
пеностекла со средней плотностью 160-180 кг/м3 находится в пределах 0,07-0,08
Вт/(м °С) при 20°С.
Водопоглощение теплоизоляционного пеностекла равно 3-5%, звукоизоляционного
— 65-75% по объему. Коэффициент звукопоглощения акустического пеностекла
при частоте 200-400 Гц составляет 0,4-0,5. Морозостойкость пеностекла
высокая. Насыщенные водой образцы пеностекла без существенного изменения
прочности выдерживают до 50 циклов попеременного замораживания при — 30°С
и оттаивания при 20°С.
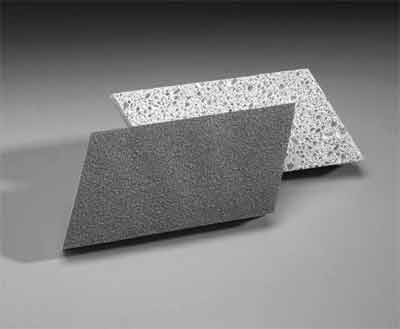
Рис. 2.
Резаное пеностекло обладает разной фактурой поверхностного слоя и вдоль
реза, может быть разной формы и применяться в качестве облицовочного материала
Производство пеностекла
Для получения теплоизоляционного пеностекла со средней плотностью 160-180
кг/м3 применяют порошки стекла с удельной поверхностью около 6000 см2/г
и углеродистые газообразователи с такой же или значительно большей удельной
поверхностью: кокс, антрацит, сажу.
Процесс производства пеностекла начинается с варки стекла заданного состава
в ванной печи. Варку стекла проводят без осветления. Хорошо проварившуюся,
но не осветленную стекломассу гранулируют и направляют на помол. Пеностекольную
шихту составляют либо совместным помолом и смешиванием предварительно
дозированного стекла и газообразователя, либо раздельным помолом компонентов
шихты и последующим их смешиванием. Чаще применяют совместный помол и
смешивание пеностекольной шихты. При совместном помоле стекла и углеродистых
газообразователей, в особенности сажи, помол стекла значительно ускоряется
вследствие действия углеродистых газообразователей как поверхностно-активных
веществ. Помол и смешивание компонентов пеностекольной шихты производят
в многокамерных трубчатых мельницах.
Для проведения вспенивания пеностекольную шихту засыпают в формы из легированной
стали, которую накрывают крышкой, зеркально повторяющей ее очертания.
Кроме этого типа форм в производстве пеностекла применяют и другие виды
форм. Перед засыпкой пеностекольной шихты внутреннюю поверхность формы
покрывают меловой или каолиновой пастой. После засыпки поверхность шихты
разравнивают, а в некоторых случаях шихту в форме уплотняют путем вибрации,
предотвращающей прилипание пластичной стекломассы к стенкам форм в процессе
вспенивания. В формы засыпают до 4-5 кг пеностекольной шихты. Вспенивание,
отжиг и охлаждение пеностекла можно производить одностадийным и двухстадийным
способами. При одностадийном способе вспенивание пеностекольной массы,
отжиг и охлаждение блоков производят в формах в непрерывно действующей
туннельной печи. При двухстадийном способе блоки пеностекла после завершения
вспенивания извлекают из форм и направляют на отжиг и охлаждение в печь
отжига, аналогичную печам для стеклоизделий. Наиболее распространен двухстадийный
способ. Он требует меньшего числа форм, облегчает автономное регулирование
температурного режима вспенивания, улучшает условия отжига пеностекольного
блока.
При двухстадийном способе пеностекольная шихта в металлических формах
проходит термическую обработку по следующему режиму. В печи вспенивания
(рис. 3 б) при 800-850°С шихта нагревается и вспенивается. Нагрев длится
около 60, вспенивание — 20-30 мин. Затем формы с пеностеклом резко охлаждают
в течение 15-20 мин. Дальнейший процесс стабилизации при 600°С длится
30-40 мин. Таким образом, через 125-150 мин термическая обработка в печи
вспенивания заканчивается, пеностекольные блоки извлекают из форм и помещают
в лер отжига. Отжиг и охлаждение пеностекольных блоков до 30°С весьма
длительный и ответственный этап термической обработки пеностекла.
В отличие от массивного стекла температуру при отжиге пеностекольных блоков
нужно снижать вначале быстрее, затем медленнее. От 600 до 500-450°С может
быть принята скорость 1-1,5 °С/мин, затем до полного охлаждения (до 30°С)
— 0,6-0,7°С/мин.
Более рациональным и экономичным является отжиг пеностекла, осуществляемый
в три этапа с трехкратным изменением скорости охлаждения. Скорость охлаждения
на первом этапе термообработки (650-560°С) может меняться в достаточно
широких пределах от 1 до 5 °С/мин и более. Основную роль в отжиге пеностекла
играет второй этап термообработки (560-480°С), скорость охлаждения на
нем не должна превышать 0,5-2 °С/мин. Напряжения, образовавшиеся на третьем
этапе термообработки (480-30°С), носят временный характер и поэтому могут
достигать предела прочности на растяжение слоев пеностекла. Поэтому скорость
охлаждения на третьем этапе можно принять от 1 до 5°С/мин.
При одностадийном способе, вспенивание и отжиг осуществляется в одной
печи, и режим отжига соответствует вышеописанному. Двухстадийный способ
подразумевает проведение вспенивания и отжига в отдельных печах с транспортировкой
изделий по воздуху. В результате имеет место резкое изменение температуры
(термоудар) в верхнем интервале отжига (при 650°С), которое может привести
к разрушение изделий. Для сохранения прочности изделий, продолжительность
перекладки не должна превышать 3 минуты.
Блоки пеностекла после отжига поступают на обработку для придания им прямоугольной
формы путем спиливания неровностей и шлифования поверхностей.
Пеностекло можно также производить в виде непрерывной ленты в печи вспенивания
длиной около 20 м. Шихту засыпают в лотки, изготовленные из жаростойкой
стали, выполненные в виде поддонов шириной 1000 мм и длиной 1600 мм; причем
по длинной стороне имеются выступы высотой 100 мм, которые образуют боковые
стенки желоба. Формы устанавливают на направляющие и с помощью толкателя
продвигают вдоль печи.
В результате последовательной стыковки лотков вдоль печи вспенивания образуется
сплошной желоб или периодически перемещаемая подложка, на которой вспенивается
лента пеностекла. Ленту пеностекла по выходе из печи распиливают на блоки,
затем они поступают на отжиг. Освобожденные от пеностекла поддоны при
помощи роликового конвейера, проходящего под печью, перемещаются обратно
к загрузочному концу печи вспенивания.
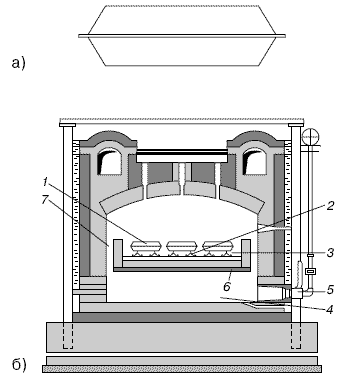
Рис. 3. Форма (а) и печь для вспенивания стекла (б) — поперечный
разрез;
1 — формы; 2 — ползуны; 3 — направляющие; 4 — подовые топки;
5 — горелки; 6 — жаростойкие плиты; 7 — вертикальные каналы
Применение пеностекла
Пеностекло в качестве теплоизоляционного материала пока недостаточно распространено
в гражданском и промышленном строительстве, что незаслуженно. Пеностеклом
изолируют полы, потолки, междуэтажные бетонные перекрытия. Крошку пеностекла
используют для теплоизоляции кровли зданий. Блоки пеностекла могут применяться
для изоляции холодильных камер и других низкотемпературных емкостей и
хранилищ.
Достаточная прочность блоков пеностекла позволяет, в отличие от других
изоляционных материалов, производить теплозащитную кладку стен без применения
специальных креплений и металлической сетки. Пеностекло в качестве тепловой
изоляции можно применять от температур глубокого холода до 450°С. Интерес
к пеностеклу в качестве конструкционного строительного материала и материала
со специальными уникальными свойствами в мире увеличивается повсеместно
по мере актуализации вопросов энергосбережения и теплозащиты в строительстве.
Технология стекла и стеклоизделий — Владимир, Транзит-Икс, 2003.