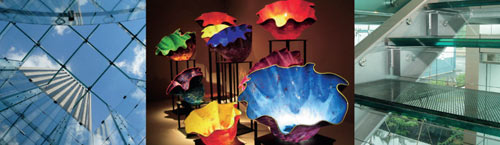
Новые изделия, отмечает Ульрих Кремс (Ulrich Kriems), обычно
создаются раньше, чем возникает технология их изготовления. В этом же случае все
случилось наоборот. Сначала был разработан техпроцесс, которого явно не хватало
в ряду способов обработки стекла.
Работая на одном малом предприятии,
специализировавшемся на выпуске точных изделий из стекла для производства
высококачественных дисплеев и других изделий на базе органических светодиодов
(OLED), которые вставляются затем в плоскую панель экрана, Ульрих обратил внимание,
что для производства таких деталей необходимо выполнить небольшие зубчатые
углубления толщиной примерно 1 мм на краях детали.
Для этого раньше
использовалась только технология пескоструйной обработки (пескоструйное 3D
эрродирование). Стекло прикрывалось липкой пленкой, а через отверстия в ней
было возможно обработать открытые участки.
Процесс был не настолько дорог
или трудоемок, сколько песок, с огромной скоростью бомбардировавший стекло,
оставлял в нем микротрещины, существенно уменьшавшие ударопрочность стеклянного
изделия. Стекло экранов было, таким образом, в состоянии «вот-вот треснет».

Ульрих Кремс решил пойти другим путем. Почему бы не обрабатывать стекло подобно тому, как поступают с пластиком? Это позволило бы упростить обработку желобчатых углублений. В поисках решений его команда натолкнулась на модное слово «термоформирование». При этом процессе материал нагревается до мягкости, становится податливым, а затем прессуется воздухом или газом под давлением, приобретая желаемую форму. Это хорошо известный и давно запатентованный способ, как и глубокая вытяжка для стекла. Но он не очень подходит для массового производства.
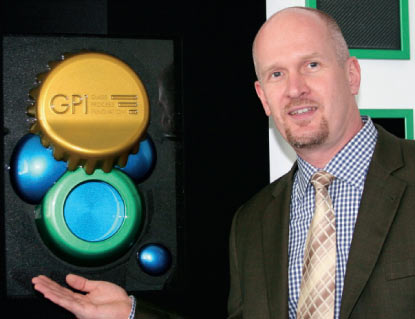
Ульрих Кремс (Ulrich Kriems) из GPInnovation GmbH успешно перенес технологию термоформирования с пластика на стекло.
На фото VDMA: Кремс рядом с некоторыми образцами трехмерных изделий из листового стекла
Кремс утверждает: «Не было никаких описаний подходящего нам
оборудования. И нам пришлось разрабатывать все с самого начала». Когда первые
желобки были изготовлены новым способом спустя два года с начала разработок, на
это оборудование не нашлось ни единого заказчика. Новые детали были на 100%
совместимыми с изготовленными по-старому. «Что обиднее всего — у нас был отличный
техпроцесс, который полностью подходил к требованиям заказчиков, но ни один из них
не хотел его приобретать».
Сейчас, спустя уже семь лет, Кремс основал свое
собственное предприятие. Он добился успеха в переносе технологии термоформирования
(глубокая вытяжка), применяемой для пластиков, для обработки стекла. За ряд прошлых
лет он полностью сформировал набор технологического оборудования и вместе со своими
бывшими коллегами создал предприятие GPInnovation GmbH в Потсдаме (Германия).
«Мы можем формировать сколь угодно сложную трехмерную поверхность на стекле,
— говорит Кремс и добавляет. — В отличие от методов, применявшихся ранее, я
разработал «существенно лучшее преобразование». Мы достигаем существенно большей
силы при вдавливании стекла в форму-изложницу. Теперь очень маленькие радиусы
и даже острые кромки — не проблема». По большей части, подходят любые типы стекла.
Кремс уточняет: «Это уникальный, единственный в мире подобный техпроцесс для получения
изделий сложной формы из тонкостенного листового стекла для различных целей».

![]() Сегмент бытовой электроники — пока самое широкое поле для применения нового процесса. Корпуса смартфонов и мобильных телефонов, выполненные из гнутого 3D-стекла, уже заменяют пластиковые изделия. Фото: GPInnovation GmbH |
Единственное ограничение нового метода — создание
машин и оборудования. Имеющееся у Кремса оборудование позволяет изготавливать
детали с размерами до 850×850 мм. Скоро появится агрегат, который сможет
обрабатывать детали размером до 2×1 м. Толщина стекла при этом — от
0,3 до 40 мм! Требуемое оборудование по технологии термоформирования для изделий
таких размеров поставит фирма Linn High Therm GmbH. Эта немецкая фирма специализируется
на промышленных печах и сотрудничает с Кремсом в области разработки оборудования
для термоформирования, имея 13% акций фирмы GPI. Еще 13% принадлежат частному
инвестору Хорсту Линну (Horst Linn) из группы «Business-Angel-Netzwerk». |
«В моем процессе нет нацеленности на строго определенный сегмент
рынка», — говорит Кремс. Теперь мы видим огромный интерес со стороны совершенно
различных областей промышленности, прежде всего со стороны производителей бытовой
электроники. Производители смартфонов уже искали технологии по производству
трехмерных деталей из стекла. Корпус, в том числе для мобильных телефонов, сделанный
из стекла, — легко изготовить. К технологии проявился интерес даже со стороны
основных мировых фирм-производителей стекла. «Они для себя открыли совершенно
новый рынок, но при этом открылся и совершенно новый рынок для производителей машин
и оборудования», — подчеркивает Кремс.
Он и Линн ожидают развития долгосрочного
спроса на технологическое оборудование для единичных изделий и для массового
производства на общую сумму, далеко превышающую «трехзначное число миллионов».
Йоахим Шмидт (Joachim Schmidt), исполнительный директор Германской ассоциации
инженеров-машиностроителей (VDMA), отвечающий также и за оборудование по стеклу,
тоже видит «существенный потенциал данной технологии». По его мнению, GPI
представляет собой «выдающийся пример весьма плодотворного сотрудничества между
машиностроителями и их заказчиками. «Мы всецело «за» подобные начинания и всячески
их поддерживаем», — сказал Шмидт.

![]() Производство строго контролируется: профиль и контур изделий строго измеряется на GPI прецизионными измерительными приборами. Фото: VDMA |
Бизнес-модель этой молодой компании достаточно
проста. Производство в Потсдаме будет расширяться и вдобавок будут продаваться
лицензии третьим сторонам. Главный вопрос в этом случае — как защитить свое «ноу-хау».
Кремс и его партнер не оставляют ни единого шанса тем, кто хочет «содрать» технологию,
причем как минимум в среднесрочной перспективе. |
Предоставлено: VDMA glass