Получение, контроль и транспортировка шихты
Отвешивание и смешивание материалов. На стекольных
заводах для отвешивания сырьевых материалов используют весы разнообразных
конструкций. По принципу действия весы бывают стационарными, отвешивающими
только один сырьевой материал; подвижными, отвешивающими все материалы
поочередно (весы-тележка, весы на монорельсе); стационарными автоматическими
и полуавтоматическими, отвешивающими все сырьевые материалы поочередно
(весы снабжены бункером, в который подаются материалы из расходных бункеров);
автоматическими, устанавливаемыми под каждым бункером.
В настоящее время на крупных заводах сырьевые материалы отвешивают на
автоматических весах, причем весы, транспортные средства и смеситель связаны
системой автоматики, обеспечивающей их синхронную работу. Взвешенные в
соответствии с рецептом шихты сырьевые материалы перемешивают в смесителях.
Контейнерные смесители исключают операцию выгрузки шихты. Их целесообразно
применять при малом объеме производства и варке небольших количеств различных
стекол (например, при варке окрашенных стекол в горшковой печи, свинцового
хрусталя и т.п.)
Для приготовления шихты при механизированном производстве применяют тарельчатые
смесители. В смесителях типа СТ сырьевые материалы через приемную воронку
загружают на вращающуюся чашу-тарелку. Перемешивание материалов осуществляется
при одновременном вращении чаши-тарелки и установленных с эксцентриситетом
по отношению к оси смесителя лопастей или катков, имеющих самостоятельный
привод. На стекольных заводах цикл смешивания в тарельчатых смесителях
автоматизирован.
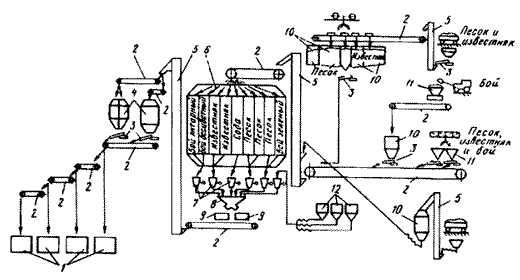
Рис. 1. Схема технологической линии приготовления шихты с линейным расположением бункеров сырьевых материалов
1 — бункера сырьевых материалов;
2 — автоматические весы;
3 — сборочный конвейер;
4 — бункер рукавного переключателя;
5 — смеситель;
6 — шнек;
7 — вагонетка (кюбель, конвейер) для транспортировки шихты к стекловаренной печи;
8 — расходный бункер;
9 — элеватор.
В автоматизированных линиях приготовления шихты применяется линейная
система расположения бункеров сырьевых материалов, под которыми расположены
стационарные автоматические весы. Один из примеров такой линии приведен
на рис. 1. Из расходных бункеров 1 сырьевые компоненты после взвешивания
на автоматических весах 2, ссыпаются сборочным конвейером 3 в бункер рукавного
переключателя 4, из которого попадают в один из смесителей 5, где они
перемешиваются и увлажняются. Из смесителя шихта выгружается в бункер
шнека 6 и транспортируется элеватором 9, который пересыпает ее в расходные
бункера 8, откуда она транспортируется к механизированному загрузчику
стекловаренной печи вагонетками 7 или транспортером.
Возможна башенная компоновка дозировочно-смесительного отделения, при
которой материалы после каждого отвеса направляются непосредственно в
смеситель, что позволяет избежать лишней транспортировки шихты и пыления.
На рис. 2 приведена технологическая схема высокопроизводительного цеха
приготовления шихты для четырех печей, в которых варят стекло разных цветов
с использованием кондиционных сырьевых материалов.
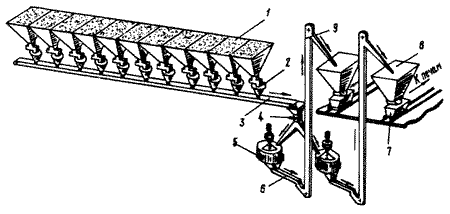
Рис. 2. Технологическая схема приготовления шихты с использованием башенного расположения бункеров сырьевых материалов для четырех стекловаренных печей
1 – стекловаренные печи;
2 – конвейеры;
3 – питатели;
4 – бункера шихты;
5 – подъемники;
6 – блок бункеров сырьевых материалов;
7 – автоматические весы;
8 — сборный бункер;
9 — смесители;
10 – промежуточные бункера сырьевых материалов;
11 – дробилка;
12 – бункера для красителей.
На заводах, выпускающих небольшие партии бытовых изделий из различных стекол, для приготовления шихты целесообразно использовать контейнеры. Шихту с применением контейнеров можно приготовить на поточной линии (рис. 3). В этом случае контейнеры последовательно проходят первый и второй весовые участки и участок ручного ввода малых добавок (красители, обесцвечиватели и т.п.). Далее контейнеры подаются на участок смешивания шихты, закрепляются в специальных устройствах, вращаются в течение определенного времени, после чего транспортируются к стекловаренной печи.
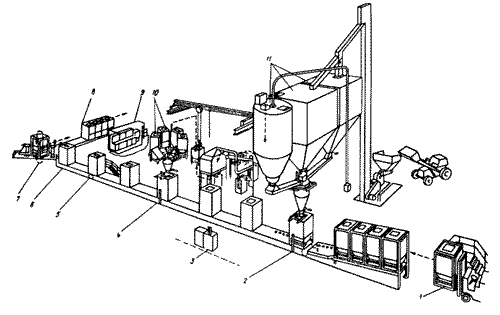
Рис. 3. Технологическая схема дозировочно-смесительного отделения с применением контейнеров
1 — контейнер;
2 — первый весовой участок;
3 — распределительный щит;
4 — второй весовой участок;
5 — участок ручного ввода малых добавок;
6 — участок подачи контейнера вилочным загрузчиком на участок смешивания;
7 — участок смешивания материалов в контейнерах;
8 — участок транспортировки контейнеров к стекловаренной печи;
9 — щит управления;
10 — бункера для сырьевых материалов;
11 — бункера для песка и стекольного боя.
Контроль качества шихты. Готовую шихту контролируют
на соответствие заданному химическому составу, влажность, однородность.
Допустимые отклонения от заданного состава компонентов в отдельных отвесах
не должны превышать по песку, соде, поташу ± 1%, по карбонатам кальция
и магния, сурику, глету, влаге ± 0,5%. При работе автоматизированных линий
требования по отклонениям состава компонентов шихты ужесточаются, что
вызывает необходимость применения кондиционных сырьевых материалов. Применение
быстродействующих рентгеновских анализаторов для экспресс-анализа шихты
и стекла в сочетании с компьютерной системой расчетов по составу шихты,
позволяют создать систему управления качеством шихты. Все расчеты проводятся
на основе вводимых в компьютер данных по химическому составу стекла и
компонентов шихты, их количеству, влажности, точности дозирования. При
этом коррекция рецепта шихты должна проводиться при изменении состава
сырьевых материалов с учетом того, что допустимые колебания содержания
оксидов в стекле не должны превышать 0,2-0,3%.
Транспортировка готовой шихты. Приготовленную
шихту и стекольный бой подают к стекловаренным печам в контейнерах, кюбелях,
бункерных вагонетках. При больших объемах подача шихты к стекловаренным
печам осуществляется ленточными конвейерами. Возможна подача шихты пневматическим
транспортом. При этом расстояние от места приготовления шихты до стекловаренной
печи должно быть возможно более коротким. Поэтому для современных заводов,
особенно стеклотарных, характерна единая компоновка дозировочно-смесительного
отделения и машино-ванного цеха.
Окончание статьи читайте в журнале |
Технология стекла и стеклоизделий