РАЗРАБОТАН НИУПЦ “Межрегиональный институт окна”, Научно-исследовательский
институт строительной физики РААСН с участием компании “illbruck”, СибАДИ,
ООО “Концепция СПК”, фирм “fischer” и “Gealan Werk Fickenscher GmbH”
ВНЕСЕН Госстроем России
ВВЕДЕН В ДЕЙСТВИЕ с 1 марта 2003 г. в качестве государственного
стандарта Российской Федерации
Печатается в сокращении
1 Область применения
Настоящий стандарт распространяется на монтажные швы узлов примыканий
оконных и наружных дверных блоков (далее — оконных блоков) к стеновым
проемам.
Стандарт применяют при проектировании, разработке конструкторской и технологической
документации, а также при производстве работ при строительстве, реконструкции
и ремонте зданий и сооружений различного назначения с учетом требований
действующих строительных норм и правил. Требования стандарта также применяют
при замене оконных блоков в эксплуатируемых помещениях.
Требования настоящего стандарта могут быть применены при проектировании
монтажных швов узлов примыканий витражных и других фасадных конструкций,
а также монтажных швов сопряжений конструкций между собой.
Стандарт не распространяется на монтажные швы узлов примыканий оконных
блоков специального назначения (например, противопожарных, взрывозащитных
и др.), а также изделий, предназначенных для применения в неотапливаемых
помещениях.
3 Термины и определения
В настоящем стандарте использованы следующие термины и определения:
Узел примыкания оконного блока к стеновому проему — конструктивная
система, обеспечивающая сопряжение стенового оконного проема (в том числе
элементов наружного и внутреннего откосов) с коробкой оконного блока,
включающая в себя монтажный шов, подоконную доску, слив, а также облицовочные
и крепежные детали.
Монтажный зазор — пространство между поверхностью стенового проема
и коробкой оконного (дверного) блока.
Монтажный шов — элемент узла примыкания, представляющий из себя
комбинацию из различных изоляционных материалов, используемых для заполнения
монтажного зазора и обладающих заданными характеристиками.
Силовое эксплуатационное воздействие на монтажный шов — воздействие,
возникающее от взаимных перемещений оконной коробки (рамы) и стенового
проема при изменении линейных размеров от температурно-влажностных и других
воздействий,
а также при усадке зданий.
Деформационная устойчивость монтажного шва — способность монтажного
шва сохранять заданные характеристики при изменении линейных размеров
монтажного зазора в результате различных эксплуатационных воздействий.
4 Классификация
4.1 Конструкции монтажных швов узлов примыкания оконных блоков к стеновым
проемам классифицируют по следующим эксплуатационным характеристикам:
— сопротивлению теплопередаче;
— стойкости к силовым эксплуатационным воздействиям;
— воздухопроницаемости;
— водопроницаемости;
— звукоизоляции;
— паропроницаемости.
4.2 Показатели основных эксплуатационных характеристик монтажных
швов подразделяют на классы согласно таблице 1.
Наименование характеристик |
Класс
|
Значение показателя
|
Сопротивление теплопередаче, м2 °С/Вт |
I
II III |
3,0 и более
от 2,1 до 2,9 от 1,2 до 2,0 |
Воздухопроницаемость при dР = 100 Па, м3 /(ч.м) |
I
II III |
Менее 0,1
от 0,1 до 0,5 от 0,6 до 1,0 |
Водопроницаемость (предел водонепроницаемости), Па |
I
II III |
600 и более
от 450 до 599 от 300 до 449 |
Деформационная устойчивость, % |
I
II III |
Свыше 17
от 14,0 до 17,0 от 10,0 до 13,0 |
Звукоизоляция, дБА |
I
II III |
Свыше 40
от 34 до 40 от 28 до 33 |
1 Водопроницаемость классифицируют по пределу водонепроницаемости наружного гидроизоляционного слоя монтажного шва.
2 Показатель деформационной устойчивости монтажного шва принимают по слою, имеющему худшее значение этого показателя
4.4 Стойкость монтажных швов к силовым эксплуатационным воздействиям
классифицируют по показателю деформационной устойчивости. За показатель
деформационной устойчивости принимают величину отношения значения наибольшего
изменения заданного размера монтажного шва (без разрушения или критического
снижения заданных характеристик) к значению заданного размера шва, выраженную
в процентах.
4.5 Классификационными признаками паропроницаемости монтажных швов
являются:
— величина и соотношение значений сопротивления паропроницанию слоев (материалов)
монтажного шва;
— величина приращения расчетного массового отношения влаги в материале
центрального слоя шва за период влагопоглощения.
Пароизоляционные свойства монтажных швов могут также характеризоваться
конструктивными признаками. Например, наличием или отсутствием пароизоляционной
прокладки между пенным утеплителем и поверхностью стенового проема.
5 Технические требования
5.1 Общие положения
5.1.1 Монтажный шов состоит из трех слоев, которые подразделяют
по основному функциональному назначению:
наружный — водоизоляционный, паропроницаемый;
центральный — теплоизоляционный;
внутренний — пароизоляционный.
Каждый из слоев монтажного шва может, кроме основных, выполнять и дополнительные
функции (например, наружный слой может иметь существенное сопротивление
теплопередаче), что необходимо учитывать при определении расчетных характеристик
конструкции. Принципиальная схема монтажного шва показана на рисунке 1.
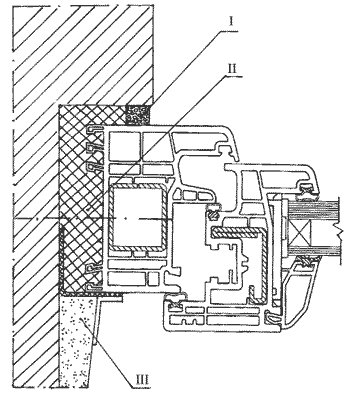
Рис. 1. Принципиальная схема монтажного шва
I — наружный водоизоляционный паропроницаемый слой;
II — центральный теплоизоляционный слой;
III — внутренний пароизоляционный слой
5.1.2 Конструкции монтажных швов устанавливают в рабочей документации
на монтажные узлы примыкания конкретных видов оконных блоков к стеновым
проемам с учетом действующих строительных норм и правил и требований настоящего
стандарта. Примеры конструктивных решений монтажных швов приведены в приложении
А.
5.1.3 Конструкции монтажных швов должны быть устойчивы к различным
эксплуатационным воздействиям: атмосферным факторам, температурно-влажностным
воздействиям со стороны помещения, силовым (температурным, усадочным и
др.) деформациям.
5.1.4 Выбор материалов для устройства монтажных швов и определение
размеров монтажных зазоров следует производить с учетом возможных эксплуатационных
(температурных, осадочных) изменений линейных размеров оконных блоков
и стеновых проемов по показателю деформационной устойчивости. При этом
эластичные изоляционные материалы, предназначенные для эксплуатации в
сжатом состоянии, должны быть подобраны с учетом их расчетной (рабочей)
степени сжатия.
5.1.5 Величина сопротивления теплопередаче монтажного шва должна
обеспечивать температуру внутренней поверхности оконного откоса и конструкции
не ниже требуемой строительными нормами и правилами.
Значения показателей воздухо, — водопроницаемости, звукоизоляции монтажных
швов не должны быть ниже значений этих показателей для применяемых оконных
блоков.
5.1.6 В зависимости от конфигурации поверхностей стеновых проемов
монтажные швы могут быть прямыми (оконный проем без четверти) или угловыми
(оконный проем с четвертью).
5.1.7 С наружной стороны монтажные швы могут быть защищены специальными
профильными деталями: дождезащитными нащельниками, звукоизоляционными
накладками и др.
С внутренней стороны монтажные швы могут быть закрыты штукатурным слоем
или деталями облицовки оконных откосов.
5.2 Требования к наружному слою
5.2.1 Наружный слой монтажного шва должен быть водонепроницаем
при дождевом воздействии при заданном (расчетном) перепаде давления между
наружной и внутренней поверхностями монтажного шва.
5.2.2 Для устройства наружного слоя рекомендуется применение материалов,
обладающих адгезией к поверхности оконных проемов и коробок оконных блоков.
Сопротивление отслаиванию (адгезионная прочность) ленточных и пленочных
материалов должно быть не менее 0,3 кгс/см, а прочность сцепления герметиков
(не менее 0,1 МПа (1,0 кгс/см2).
5.2.3 Материалы наружного слоя должны быть устойчивы к воздействию
эксплуатационных температур в диапазоне:
— для швов обычного исполнения ( от минус 35 °С до 70 °С;
— для швов морозостойкого исполнения (от ниже минус 36 °С до 70 °С.
Примечание — Нижний предел отрицательных эксплуатационных температур,
подтвержденный результатами испытаний, указывают в сопроводительной документации
(паспорте) на материал наружного слоя.
5.2.4 Изоляционные материалы наружного слоя (не защищенные при
эксплуатации от воздействия солнечных лучей) должны быть устойчивы к УФ
облучению (суммарная доза облучения лицевых поверхностей при проведении
испытаний (не менее 5 ГДж/м2).
5.2.5 Материалы наружного слоя не должны препятствовать удалению
парообразной влаги из центрального слоя шва. Значение коэффициента паропроницаемости
материала наружного слоя — не менее 0,15 мг/(м.ч.Па). Применение пароизоляционных
материалов в качестве материалов наружного слоя не допускается, кроме
случаев применения герметизирующих материалов в комбинации со штукатурным
раствором, обеспечивающим требуемую паропроницаемость наружного слоя.
5.3 Требования к центральному слою
5.3.1 Центральный изоляционный слой должен обеспечивать требуемое
сопротивление теплопередаче монтажного шва. Величина сопротивления теплопередаче
должна находиться в диапазоне значений этого показателя для стены и оконной
конструкции.
5.3.2 Заполнение монтажного шва теплоизоляционными материалами
должно быть сплошным по сечению, без пустот, разрывов, щелей и переливов.
Расслоения, сквозные зазоры, щели, а также раковины с наибольшим размером
10 мм не допускаются.
5.3.3 Сопротивление паропроницанию центрального слоя монтажного
шва должно находиться в диапазоне значений этого показателя для наружного
и внутреннего слоев.
5.3.4 Адгезионная прочность сцепления монтажных пенных утеплителей
с поверхностями оконных проемов и коробок оконных блоков должна быть не
менее 0,1 МПа (1,0 кгс/см2).
5.3.5 Водопоглощение пенных утеплителей центрального слоя при полном
погружении за 24 ч не должно превышать 3 % по массе.
5.3.6 В необходимых случаях для предотвращения воздействия влаги
со стороны стенового проема на центральный изоляционный слой (в плоскости
возможного конденсатообразования) допускается установка пароизоляционной
ленты между внутренней поверхностью стенового проема и монтажным швом.
5.4 Требования к внутреннему слою
5.4.1 Пароизоляционные материалы внутреннего слоя монтажного шва
должны иметь коэффициент паропроницаемости не более 0,01 мг/(м.ч.Па).
5.4.2 Пароизоляционные материалы внутреннего слоя должны иметь
сопротивление отслаиванию (адгезионная прочность) от поверхностей, образующих
монтажный зазор, не ниже значений, установленных в 5.2.2 для материалов
наружного слоя.
5.4.3 Конструкция и материалы внутреннего слоя должны обеспечивать
надежную изоляцию материалов центрального слоя от воздействия водяных
паров со стороны помещения.
Пароизоляционные материалы по внутреннему контуру монтажного зазора должны
быть уложены непрерывно, без пропусков, разрывов и непроклеенных участков.
5.5 Общие требования к материалам
5.5.1 Материалы, применяемые в конструкциях монтажных швов, должны
соответствовать требованиям стандартов, условиям договоров на поставку
и технической документации, утвержденной в установленном порядке.
5.5.2 Материалы, применяемые для устройства монтажных швов, подразделяют
по диапазону рабочих температур, при которых допускается производство
монтажных работ, на материалы:
— летнего исполнения (от + 35 °С до + 5 °С);
— зимнего исполнения (с рабочими температурами ниже + 5 °С).
5.5.3 Материалы наружного слоя должны быть стойкими к длительному
атмосферному воздействию.
Материалы, применяемые для устройства различных слоев монтажного шва,
должны быть совместимы между собой, а также с материалами стенового проема,
оконной коробки и крепежных деталей.
Долговечность материалов (срок службы), применяемых для устройства монтажного
шва, должна быть не менее 20 условных лет эксплуатации (показатель долговечности
вводится в действие с 01.01.2005 года).
5.5.4 Материалы, применяемые в конструкциях монтажных швов, должны
иметь санитарно-эпидемиологическое заключение органов Госсанэпиднадзора.
5.5.5 Материалы для устройства монтажных швов должны хранится в
сухих отапливаемых вентилируемых помещениях с соблюдением условий хранения,
указанных в нормативной документации на эти материалы.
5.5.6 Требования к крепежным элементам и их установке приведены
в приложении Б.
5.6 Требования к размерам
5.6.1 Номинальные размеры монтажных зазоров для устройства швов
устанавливают в рабочих чертежах узлов примыканий оконных блоков к стеновым
проемам.
5.6.2 При установлении размеров монтажных швов учитывают:
— конфигурацию и размеры оконного проема, коробки оконного блока и подоконной
доски включая их допустимые предельные отклонения;
— предполагаемые изменения линейных размеров оконных проемов и блоков
в процессе их эксплуатации от температурно-влажностных деформаций и усадок;
— технические характеристики материалов монтажного шва, исходя из обеспечения
необходимого сопротивления эксплуатационным нагрузкам (например, размер
наружной изоляционной ленты подбирают исходя из расчетной степени сжатия,
позволяющей обеспечить получение заданных значений водо- и паропроницаемости);
— температурный режим производства монтажных работ.
5.6.3 Номинальные размеры и конфигурация оконных проемов должны
соответствовать установленным в рабочей проектной документации. Рекомендуемые
предельные отклонения от номинальных размеров высоты и ширины проема:
+15 мм. Отклонение от вертикали и горизонтали не должно превышать 3,0
мм на 1 м, но не более 8 мм на всю высоту или ширину проема. Отклонения
от вертикали и горизонтали должны находиться в поле допусков отклонений
по высоте и ширине.
Рекомендуемые размеры монтажных зазоров (с учетом допустимых предельных
отклонений) при монтаже оконных блоков по ГОСТ 23166 приведены на рисунке
2.
Рисунок 2. Размеры монтажных зазоров (швов) при установке оконных блоков из различных материалов по ГОСТ 23166
1 При монтаже деревянных оконных блоков
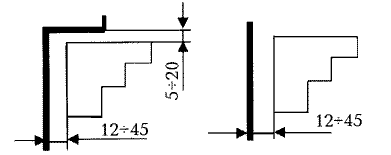
2 При монтаже оконных блоков из алюминиевых и ПВХ профилей
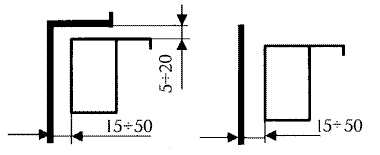
а) оконные блоки из алюминиевых сплавов при размере стороны до 2000 мм
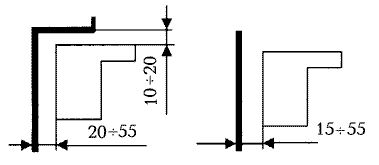
б) оконные блоки из ПВХ профилей белого цвета при размере стороны до 2000 мм, а также алюминиевые оконные блоки при размере стороны от 2000 мм до 3500 мм.
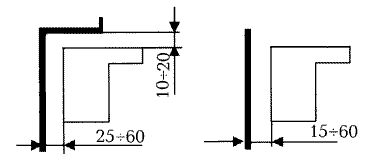
в) оконные блоки из ПВХ профилей белого цвета при размере стороны от 2000 мм до 3500 мм, а также из профилей других цветов при размере стороны до 2000 мм.
5.6.4 Предельные отклонения от габаритных размеров коробок оконных
блоков устанавливают в нормативной документации на изделия.
Отклонения от вертикали и горизонтали деталей коробок смонтированных оконных
блоков не должны превышать 1,5 мм на 1 м длины, но не более 3 мм на высоту
изделия.
5.7 Требования к подготовке поверхностей монтажного зазора
5.7.1 При подготовке оконной конструкции и проема к монтажу должны
соблюдаться требования 5.6.3, 5.6.4.
5.7.2 Кромки и поверхности наружных и внутренних откосов не должны
иметь выколов, раковин, наплывов раствора и других повреждений высотой
(глубиной) более 5 мм. Дефектные места должны быть зашпаклеваны водостойкими
составами. Пустоты в проеме стены (например, полости на стыках облицовочного
и основного слоев кирпичной кладки, в местах стыков перемычек и кладки,
а также пустоты, образовавшиеся при удалении коробок при замене окон)
следует заполнять вставками из жестких утеплителей или антисептированной
древесины.
Поверхности, имеющие масляные загрязнения, следует обезжиривать. Рыхлые,
осыпающиеся участки поверхностей должны быть упрочнены (обработаны связующими
составами или специальными пленочными материалами).
5.7.3 Перед установкой в монтажном шве изоляционных материалов
поверхности оконных проемов и конструкций должны быть очищены от пыли
и грязи, а в зимних условиях (от снега, льда, инея с последующим прогревом
поверхности.
5.7.4 Общие требования по производству работ при устройстве монтажных
швов приведены в приложении В.
7 Методы испытаний
7.4 Внешний вид и качество установки элементов и устройство слоев
монтажного шва оценивают визуально с расстояния 400-600 мм при освещенности
не менее 300 лк.
7.5 Определение прочности сцепления (адгезии) герметизирующих лент
и прокладок к элементам конструкций при периодических испытаниях при производстве
работ осуществляют в следующей последовательности:
— с помощью специального режущего инструмента (например, резака) подрезают
край ленты, установленной на поверхность монтажного стыка;
— край ленты зажимают в специальном захвате и через динамометр отрывают
по нормали к поверхности сцепления, фиксируя при этом силу отрыва.
Отслоение ленты должно происходить при усилии не менее 0,3 кг/см.
7.6 Методы приемосдаточных и периодических лабораторных испытаний
7.6.2 Воздухо, -водопроницаемость монтажных швов определяют по
ГОСТ 26602.2.
Испытания проводят с использованием специального устройства, конструкция
которого представлена на рисунке 3. Устройство представляет из себя кассету
(например, деревянную) с установленной в нее глухой панелью. Внутренний
профиль брусков кассеты имитирует размеры и конфигурацию откосов оконного
проема.
Панель представляет из себя коробку оконного блока, обшитую с двух сторон
листовым материалом (например, водостойкой фанерой по НД).
Поверхности кассеты и панели должны иметь водостойкое покрытие.
Зазор между кассетой и образцом оконного блока, а также конструкцию и
технологию устройства монтажного шва принимают согласно конструктивному
решению узла примыкания, принятому в проектной документации.
Устройство устанавливают в проем испытательной камеры на герметизирующих
прокладках.
7.6.3 Звукоизоляцию определяют по ГОСТ 26602.3. Для проведения
испытания используют устройство по 7.6.2. Внутренний объем панели обшивают
листовым звукопоглощающим материалом и заполняют сухим песком. Устройство
устанавливают в проем испытательной камеры на звукоизоляционной замазке.
Конструктивное решение панели должно обеспечивать звукоизоляцию не менее
40 дБА.
7.6.4 Устойчивость наружного изоляционного слоя к воздействию ультрафиолетового
облучения определяют, используя режим испытаний, приведенный в ГОСТ 30673
(облучение в аппарате “Ксенотест”). Испытания проводят на трех образцах
материалов изоляционного слоя длиной не менее 200 мм. Результат испытания
признают удовлетворительным, если после испытаний на поверхности каждого
образца отсутствуют разрывы, трещины, раковины, расслоения и потеки.
7.6.7 Сопротивление отслаиванию (адгезионную прочность) пленочных
и ленточных материалов наружного и внутреннего изоляционных слоев определяют
по ГОСТ 10174. Прочность сцепления герметиков с основой определяют по
ГОСТ 26589, метод Б (при этом один из склеиваемых образцов изготавливают
из алюминиевого сплава или поливинилхлорида толщиной 3-5 мм).
7.6.8 Для определения адгезионной прочности пенных утеплителей
устанавливают величину усилия, требуемого для разрушения связи между утеплителем
и конструкционным материалом при действии растягивающих сил, направленных
перпендикулярно плоскости контакта.
Число образцов для испытаний — не менее 5.
7.6.8.1 Аппаратура и приспособления
Машина разрывная, обеспечивающая разрушение образца со скоростью движения
активного захвата (10±1) мм/мин и позволяющая измерить значение разрушающего
усилия с погрешностью не более 1 %;
Специальное приспособление, установленное в зажимах испытательной машины.
Приспособление должно обеспечивать совпадение продольной оси образца с
направлением прилагаемого усилия.
7.6.8.2 Образцы для испытаний
Образцы изготавливают путем заливки и вспенивания утеплителя в металлической
форме с внутренним диаметром (51±0,5) мм и высотой не мене 30 мм, в днище
которой укреплен диск из конструкционного материала (например, из поливинилхлорида
или алюминиевого сплава). Внутренние цилиндрические поверхности формы
смазывают консистентной смазкой. Поверхность диска должна быть обезжирена.
После вспенивания и отвердевания утеплитель путем механической обработки
доводится по диаметру до размеров диска (50±0,5) мм, а по высоте ( до
(30±1) мм. Допускается использовать прямоугольные образцы размером ((50
і 50 і 30) ± 0,5) мм. Полученные таким образом два образца попарно склеиваются
эпоксидным клеем.
7.6.8.3 Порядок проведения и обработка результатов испытания
Склеенный образец с помощью приспособлений устанавливают в зажимах машины.
Испытания проводят при температуре (20±2) °С и при скорости движения захватов
машины (10±1) мм/мин.
Растяжение проводят до разрушения или отслоения образца от подложки, при
этом фиксируют наибольшую нагрузку, достигнутую при испытаниях.
Обе части испытанного образца подвергают визуальному осмотру для определения
характера разрушения (по утеплителю, адгезионному шву или смешанного характера).
Прочность сцепления утеплителя с конструкционным материалом s, МПа (кгс/см2),
вычисляют по формуле
s =Pmax / S (1)
где Pmax — максимальное усилие при отрыве или разрушении образца, кгс.
S — площадь поперечного сечения образца, см2.
За результат испытаний принимают среднеарифметическое значение результатов
испытаний образцов.
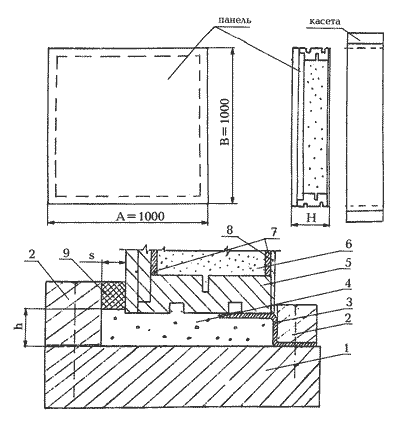
Рисунок 3 Устройство для испытаний монтажных швов на воздуховодопроницаемость и звукоизоляцию
А, В, Н — размеры панели
s, h — размеры зазоров под монтажный шов.
1 — кассета с накладными брусками;
2 — накладные бруски;
3 — паронепроницаемая лента;
4 — пенный утеплитель;
5 — коробка панели;
6 — заполнение панели (например, звукоизоляционный материал);
7 — звукопоглощающая прокладка;
8 — обшивка панели;
9 — водоизоляционная прокладка
7.6.9 Деформационную устойчивость монтажного шва определяют по
максимальной величине его деформации под воздействием силы, направленной
перпендикулярно к плоскости монтажного шва, при которой сохраняется его
целостность. Допускается проводить этот вид испытаний монтажного шва на
пенном утеплителе.
Число образцов для испытаний — не менее 3.
7.6.9.1 Аппаратура и приспособления
Машина разрывная, обеспечивающая разрушение образца со скоростью движения
активного захвата (10±1) мм/мин и позволяющая устанавливать значение разрушающего
усилия с погрешностью не более 1 %;
Специальное приспособление с обоймой для размещения образцов монтажного
шва. Приспособление при проведении испытаний должно обеспечивать совпадение
поперечной оси образца с направлением прилагаемого усилия (рисунок 4).
Специальное устройство для подготовки образцов пенного утеплителя и их
установки в испытательной машине (схема устройства представлена на рисунке
4а).
7.6.9.2 Образцы для испытаний
Образцы монтажного шва для проведения испытаний получают путем послойного
заполнения обоймы специального приспособления изоляционными материалами
в соответствии с проектным решением и технологией производства монтажных
работ (рисунок 4).
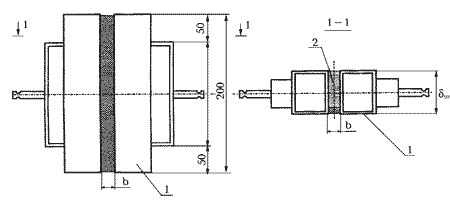
Рисунок 4 Схема приспособления для испытания монтажных швов на деформационную устойчивость
b — толщина шва;
1 — обойма из алюминия или нержавеющей стали толщиной 3 мм;
2 — образец испытываемого монтажного шва.
Образцы пенного утеплителя для проведения испытаний получают путем заполнения
им корпуса устройства, представленного на рисунке 4а. Внутренний диаметр
корпуса, определяющий размер образца — (60+0,2) мм, высота внутренней
полости корпуса — 30 мм (без учета толщины ограничительных пластин). Внутренняя
поверхность корпуса должна быть смазана консистентной смазкой. На дно
корпуса устройства до заливки пены устанавливают алюминиевую пластину
диаметром (60–0,2) мм. Вторую пластину диаметром (65–0,5) мм устанавливают
в верхней части корпуса в виде крышки и жестко фиксируют любым способом.
Заливку пены производят в отверстие диаметром 8 мм в боковой стенке корпуса.
Для удаления излишка пены предусматривают такое же отверстие с другой
стороны корпуса. После заливки пены образец выдерживают не менее суток,
после чего образец вынимают из корпуса.
7.6.9.3 Порядок проведения испытания
Обойму с образцом монтажного шва (или образец пенного утеплителя) устанавливают
в захватах машины. Образец, представляющий собой цилиндр отвердевшей пены,
зажатый между двумя алюминиевыми пластинами, устанавливают в захватах
машины. Испытание проводят при температуре (20±2) °С путем последовательных
растяжений и сжатий образца. Величину растяжения и сжатия в миллиметрах
устанавливают исходя из назначения монтажного шва. Производят не менее
20 циклов растяжения(сжатия образца. Между каждым циклом производят выдержку
образца без нагрузки не менее 20 мин.

Рисунок 4а. Схема устройства для подготовки образцов и испытания пенного утеплителя на деформационную устойчивость
I — положение пластин при заданной (начальной) толщине образца (h1);
II — положение пластин при наибольшем сжатии образца (h2);
III — положение пластин при наибольшем растяжении образца (h3);
1 — корпус устройства;
2 — образец материала;
3 — алюминиевые пластины толщиной не менее 2,0 мм;
4 — смазка.
7.6.9.4 Оценка результатов испытания
После завершения испытания визуально осматривают поверхности образцов.
Результат испытания признают удовлетворительным, если каждый образец не
имеет сквозных расслоений и разрушений.
Деформационную устойчивость j, %, определяют по формуле
j = ( Dh / h1 ) * 100, (2)
где Dh — размер перемещения пуансона (разница между толщиной образца при
растяжении и сжатии), мм;
h1 — заданная (начальная) толщина образца, мм.
7.6.10 Устойчивость монтажного шва к воздействию эксплуатационных
температур определяют по материалам наружного изоляционного слоя. Оценку
морозостойкости производят по температуре хрупкости по ГОСТ 7912 (диаметр
изгиба 400 мм) и теплостойкости по ГОСТ 2678.
7.6.11 Долговечность (срок службы) монтажного шва определяют по
НД и методикам, утвержденным в установленном порядке. Совместимость материалов
подтверждают испытаниями на долговечность монтажного шва.
8 Гарантии производителя работ
Гарантийный срок монтажного шва устанавливают в договоре между производителем
работ и заказчиком, но не менее 5 лет со дня подписания акта сдачи-приемки.