AGC has developed a digital twin technology for the glass melting process. It is called CADTANK Online Computation and Optimisation Assistant, or COCOA. The technology combines an online stimulator with a digital prototyping tool. Full-scale operational verification at float furnaces begins in February.
The temperature inside a float furnace and the flow of molten glass change daily depending on the condition of the raw materials and refractories. Dynamic factors make it necessary to adjust the optimum operating conditions of the furnace. This takes time. And the production volume declines during this period.
The COCOA modelling tool can check changes in the temperature distribution inside a float furnace, the flow of molten glass, etc., based on a simulation model automatically generated from the float furnace operation data.
The next step in the development of digital twin technology is the automatic estimate evaluation of information, using a technique called “data assimilation”. The application of data assimilation to the modelling of glass melting processes is expected to improve prediction accuracy. AGC is collaborating with Dr Takemasa Miyoshi of the Data Assimilation Research Team at the RIKEN Center for Computational Science.
To adapt the glass production process to modern needs, the market is making efforts to reduce carbon emissions:
Pilkington UK to produce architectural glass using hydrogen instead of natural gas.
A digital twin is a reproduction of the environment of a real space within a virtual space based on information from the real space.
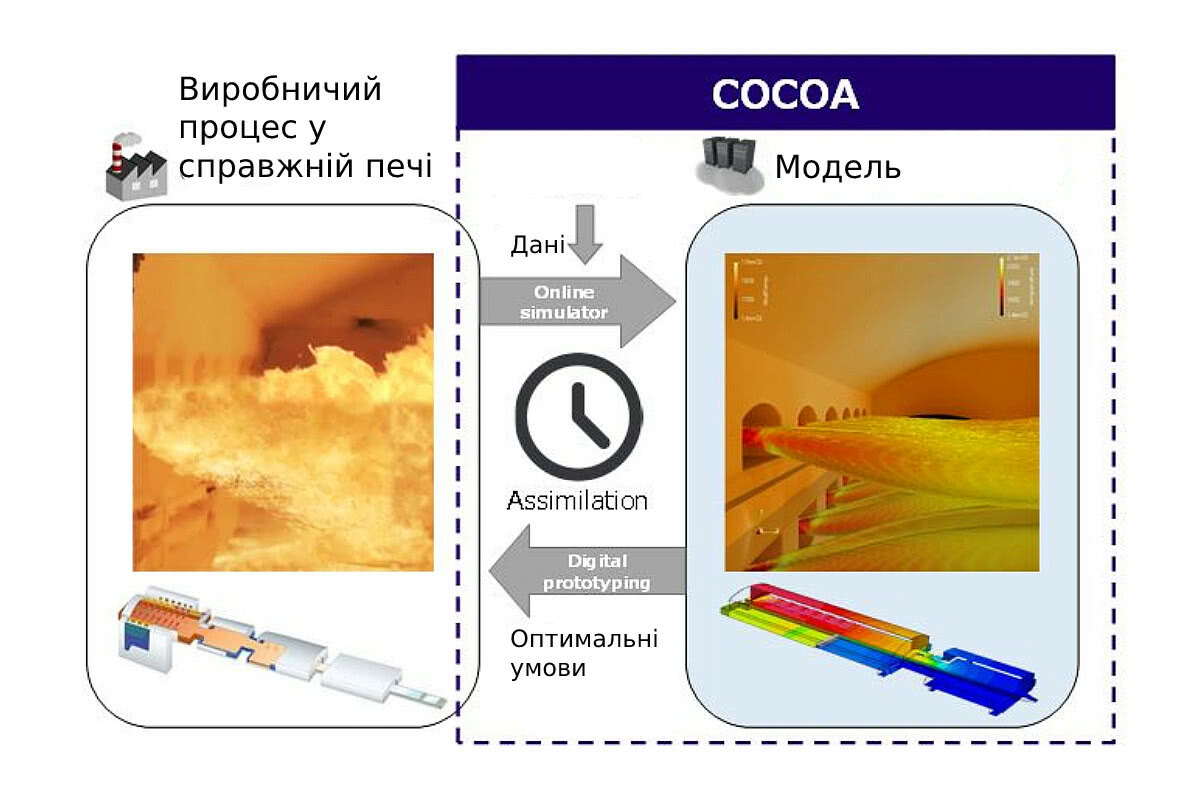
Image: AGC
AGC develops a digital twin technology for float furnaces
ID no: 22549
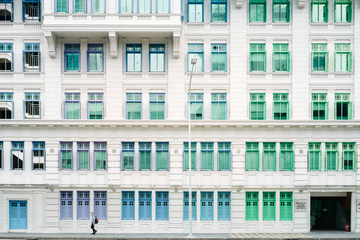
Aug 11, 2025
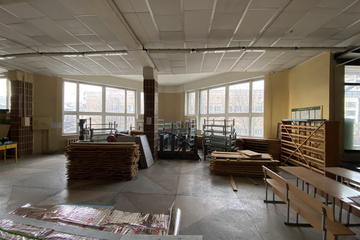
Aug 5, 2025
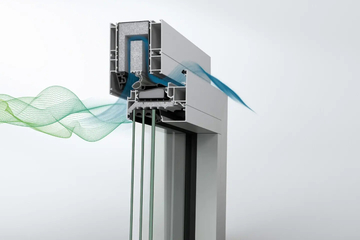
Aug 4, 2025
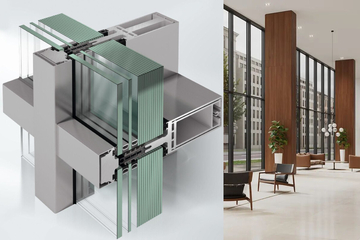
Aug 27, 2025
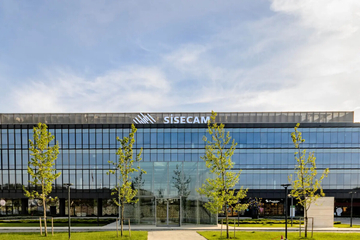
Aug 26, 2025
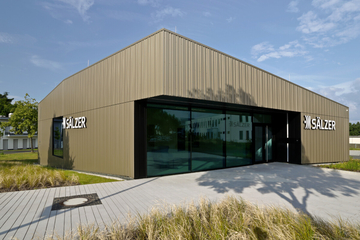
Expert from Schüco showcased the possibilities of secure transparent constructions in the new centre
Aug 20, 2025
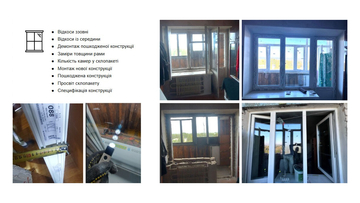
Aug 19, 2025